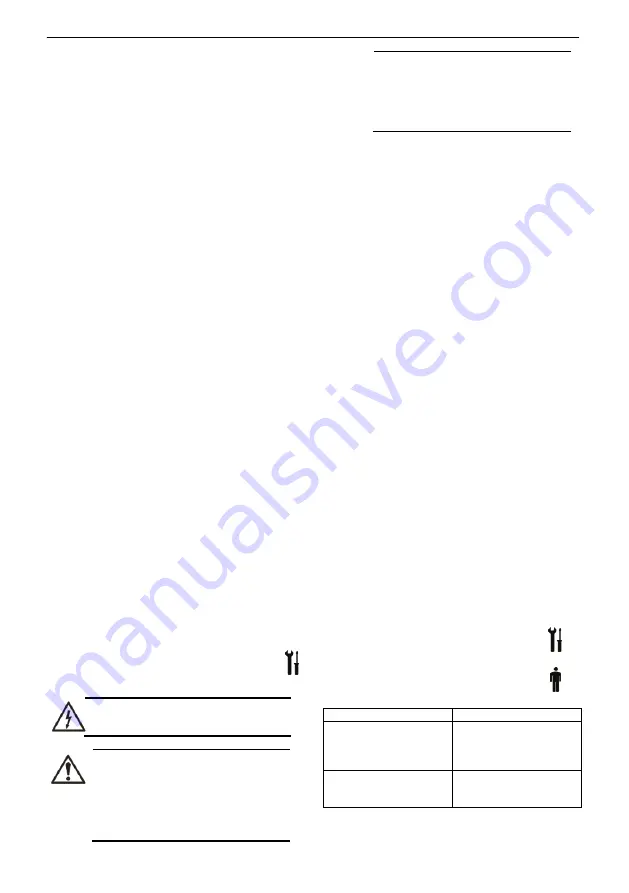
en - Original instructions
25
1. Locate the arrows on the adaptor or the motor
fan cover to determine the correct rotation
direction.
2. Start the motor.
3. Quickly check the direction of rotation through
the coupling guard or through the motor fan
cover.
4. Stop the motor.
5. If the rotation direction is incorrect, then do as
follows:
a) Disconnect the power supply.
b) In the terminal board of the motor or in the
electric control panel, exchange the position of
two of the three wires of the supply cable.
c) Check the direction of rotation again.
5.3 Start the pump
The responsibility to check the correct flow and the
temperature of the pumped liquid rests with the
installer or owner.
Before the pump is started, make sure that:
Only liquids with conductivity >1000
[pS/m] (Refer to PD CLC/TR 60079
–32–
1:2015) are used.
The maximum liquid temperature (t
max
)
stated on the pump nameplate must
never be exceeded.
The combination of the pump and the
dry-running protection is described in the
Explosion
Protection
Document
according to the 1999/92/EC Directive.
The pump does not leak before start and
during operation.
The pump is vented before start after
periods of idling the equipment.
The pump is correctly connected to the
power supply.
The pump is correctly filled according to
instructions in
The on-off valve located downstream
from the pump is closed.
1. Start the motor.
2. Gradually open the on-off valve on the
discharge side of the pump.
At the expected operating conditions, the pump must
run smoothly and quietly. If not, refer to
6
Maintenance
Precautions
Electrical Hazard:
Disconnect and lock out electrical power
before installing or servicing the unit.
WARNING:
Maintenance and service
must be performed by
skilled
and
qualified
personnel only.
Observe
accident
prevention regulations in
force.
Use suitable equipment
and protection.
Make sure that the drained
liquid does not cause
damage or injuries.
6.1 Service
If the user wishes to schedule regular maintenance
deadlines, they are dependent on the type of
pumped liquid and on the operating conditions of the
pump.
Contact Xylem or the Authorised Distributor for any
requests
or
information
regarding
routine
maintenance or service.
Extraordinary maintenance may be necessary to
clean the liquid end and/or replace worn parts.
Motor bearings
After approximately five years, the grease in the
motor bearings is so aged that a replacement of the
bearings is recommended. The bearings must be
replaced after 25000 operating hours or according to
the
motor
supplier
maintenance
instructions,
whichever is shorter.
Motor with regreasable bearings
Follow motor supplier maintenance instructions.
6.2 Inspection checklist
Check for leakage of the mechanical seal. Replace
the mechanical seal if leakage is found.
6.3 Disassemble and replace the pump
parts
For more information about spare parts and
assembly and disassembly of the pump, contact
Xylem or the Authorised Distributor.
Repair and/or maintenance of the pump must only
be carried out by Xylem or the Authorised
Distributor.
7
Troubleshooting
7.1 Troubleshooting for users
The main switch is on, but the electric pump
does not start.
Cause
Remedy
The thermal protector
incorporated
in
the
pump
(if
any)
has
tripped.
Wait until the pump has
cooled
down.
The
thermal protector will
automatically reset.
The protective device
against dry running has
tripped.
Check the liquid level in
the tank, or the mains
pressure.
Summary of Contents for ESHS ATEX
Page 90: ...it en fr de es nl 90...
Page 94: ...it en fr de es nl 94 6 7 8...
Page 95: ...it en fr de es nl 95 9 10 11...
Page 101: ......