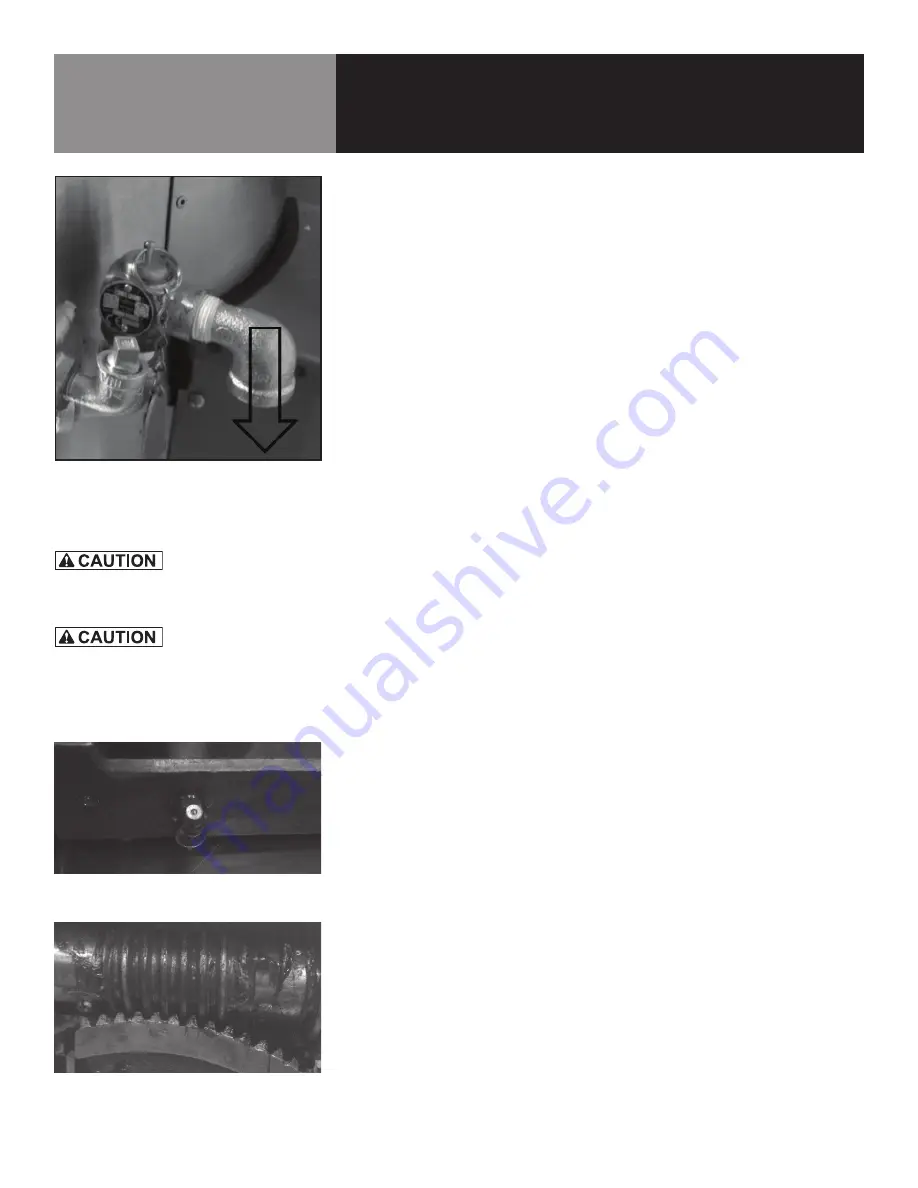
OM-LKT-45G 15
Maintenance
4. jacket Filling
The jacket was charged at the factory with the proper amount of treated
water. You may need to restore this water because it was lost as steam during
venting. Every day, before you turn on the unit, make sure the water level is
approximately in the center of the water level sight glass (See Photo 10-2 on
page 10).
a. If you are replacing water lost as steam, use distilled water.
do not use
tap water.
If you are replacing treated water that was drained from the
jacket, contact LoLo Service Support at 877-246-5656.
b. Allow the kettle to cool completely. Remove the pipe plug from the jacket
fill assembly.
c.
Open the gate valve and pour in the distilled.
TIP
: Using a funnel will help
you in this process. Hold the pressure relief valve open while you pour, to
let air escape from the jacket.
NOTE
: The low water light (red indicator lamp) comes on when the level
drops below the minimum line on the sight glass. Refill with distilled water
until the level returns to between the MIN and MAX marks on the water
sight glass.
d. Close the gate valve and replace the pipe plug.
e. Air that gets into the jacket during the filling operation must be removed,
because it will make heating less efficient. Follow the procedure in
Jacket Vacuum - Removing Air From Jacket to restore a negative pressure
(vacuum) reading.
ImPORTANT
: If most or all of the jacket water is lost due to a leak, contact
LoLo at 877-246-5656 or your LoLo authorized service provider. The
source of the leak will need to be determined and repaired; and the kettle
jacket refilled with chemically treated water.
5. lubricate Tilt mechanism
The gear housing has fittings for lubrication of moving parts. The gears do
not run in oil, so periodic lubrication with grease is necessary. Frequency of
lubrication depends on operating conditions, but
it should be done at least
once every six months.
a. Use a #2 grade LGI lithium grease to add grease through Zerk fittings on
gear housing until it flows out of the bearings around the trunnion shaft.
b. Place liberal amounts of grease on the gear to cover the arc that is in
contact with the worm gear.
c.
Keep the inside of the control console clean and dry.
Photo 15-1
Make sure that the open end of
the elbow on the pressure relief valve
is directed downward.
KEEP gREASE AwAY FROm ElECTRICAl
PARTS lOCATEd NEAR ThE gEARS.
TO AvOId INjURY, REAd ANd FOllOw
All PRECAUTIONS STATEd ON ThE
lAbEl OF ThE wATER TREATmENT
COmPOUNd.
Photo 15-2
Add grease through Zerk fittings.
Photo 15-3
Liberally grease the large gear segment
where it contacts the worm gear.