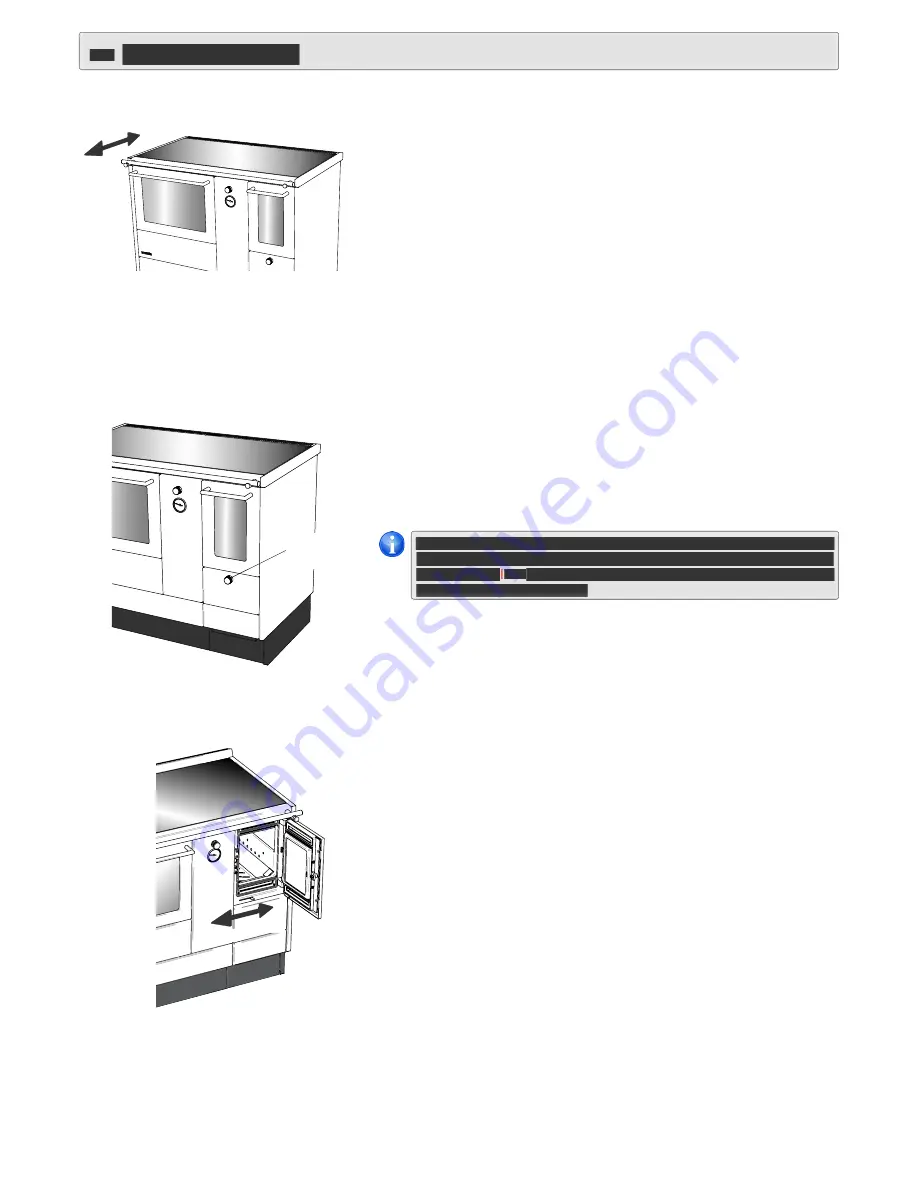
Page 14
Start-up fl ap
To facilitate initial heating, all LOHBERGER stoves are equipped with a start-up
fl ap. Opening the start-up fl ap provides a direct route from the fi rebox chamber
to the fl ue pipe. The fl ue gases then need not take the “long” route through
the oven, but enter the fl ue pipe while still hot, rapidly establishing a fl ue drau-
ght. Once there is suffi cient draught in the fl ue and the initial heating phase is
completed, close the start-up fl ap again.
It is incorporated in the hand rail on the side opposite to the combustion cham-
ber. Pulled out is open; pushed in is closed (Figure 20).
Caution: The start-up fl ap must only remain open during the initial heating
phase. If the start-up-fl ap remains open when heating, this will cause the stove
to overheat and damage stove components. An open start-up fl ap will also
result in increased fuel consumption.
Air control
The AquaTherm appliance is fi tted with an automatic output controller. This
device serves to “restrict” the supply of combustion air; but this has only a
limited effect on the output. It is defi nitely not suitable for compensating an
excess of fuel. A certain amount of fuel requires a certain amount of oxygen for
optimum combustion. If the wood is supplied with less air than is required for
clean and effi cient combustion, less energy is generated in the appliance (pro-
tecting the appliance to a great extent from overheating) – the unused “wood
gas”, however, escapes through the fl ue.
The result: low effi ciency and high environmental load.
Remedy: load the stove only up to the recommended fuel level.
Primary air control
The supply of the primary air required for combustion is controlled with the
rotary knob below the fi rebox door (Figure 21). This determines the rate of
burning and therefore the heat output of the stove.
In position “0” the controller is closed, no combustion air is supplied. In posi-
tion “1” minimum air supply is provided; select this position for slow-burning
operation. Turning the rotary knob to position “6” means maximum air supply,
necessary especially during the heating-up phase.
Air settings see Table on page 18
Secondary air control
The supply of secondary air (combustion air fl owing over the fuel from the top)
produces combustion that matches the fuel being used and keeps down the
pollutant emissions. The secondary air fl ows through openings in the rear wall
of the combustion chamber as well as from below and at the top along the
combustion chamber door (along the viewing window, if present) over the fuel
into the combustion chamber.
The secondary air is controlled with the secondary air slider which is visible
in the lower area after opening the fi rebox door (Figure 22). Moving the slider
towards the outer wall of the appliance reduces the incoming secondary air
fl ow; moving towards the oven increases it.
Air settings see Table page 18
Figure 20
Figure 21
Figure 22
open
closed
Max.
Min.
Control knob for
primary air