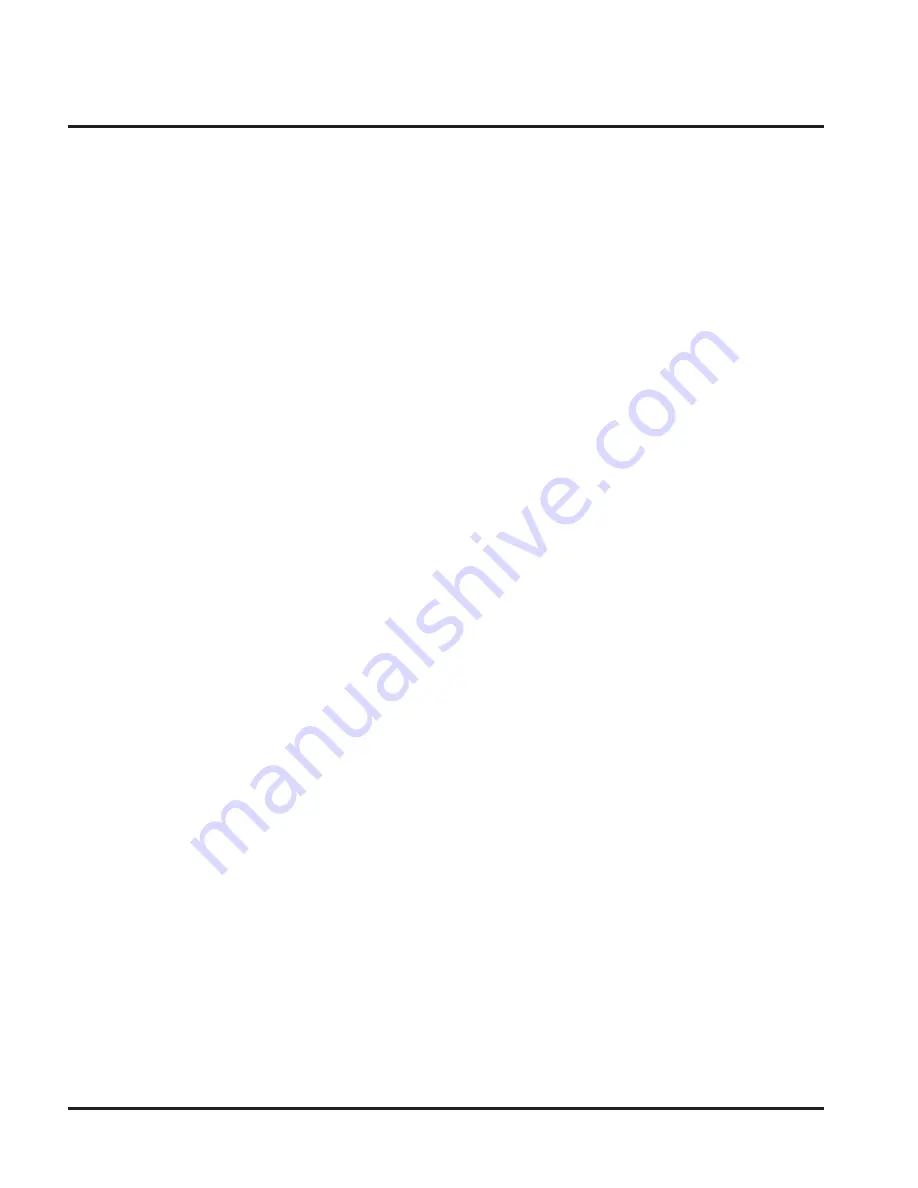
6
Battle Ax Light - Skid Loader OM
Safety Rules
These are general safety considerations. Additional
precautions may be necessary to operate your
machine in a safe manner. Be certain you are operating
your machine in accordance with all safety codes,
OSHA rules and regulations, insurance requirements
and local, state, and federal laws.
•
Read and observe all warnings decals on the machine
before attempting to operate the attachment. Do not
attempt to operate this attachment unless all factory
devices and decals are in place. Keep safety decals
clean of dirt and grime. Keep all guards, shields and
decals in place.
• Remove from area of operation all foreign objects
such as bottles, rocks, wire, etc., that might become
tangled in the rotor, causing damage to the machine
or be thrown striking other objects.
• Do not allow any people and animals within 300 feet
of the machine and attachment during operation.
• Do not allow anyone to operate the attachment
until he or she has read the owner’s manual and is
completely familiar with all safety precautions. Keep
the work area clear of all unauthorized personnel.
• Do not allow persons under the influence of alcohol,
medications, or other drugs that can impair judgment
or cause drowsiness to operate or maintain the
machine.
• Always use an approved roll bar and seat belt for
safe operation. Overturning a machine without a roll
bar and seat belt can result in injury or death.
• Use the handholds and step plates when getting on
and off the machine to prevent falls. Keep steps and
platform cleared of mud and debris.
• Always have an operator in the machine while the
attachment is in operation. Never leave the machine
and attachment running and unattended.
• Operate the attachment only from the operator’s
seat.
• Keep your feet on the pedals, (floor plates) seat belt
fastened snuggly and seat bar lowered, (if equipped),
when operating the attachment.
• The adjustable push bar could contact the machine
in some positions. Before starting the power unit,
set the push bar in the most forward position, then
slowly rotate the attachment back while an assistant
checks for clearance. Repeat this process in the
other settings to determine which positions are
usable with your machine.
• Never attempt to make any adjustments while the
attachment is running or the key is in the “ON”
position in the machine. Before leaving the operator’s
position, disengage power to the attachment, shut
off engine and remove ignition key.
• Disengage auxiliary hydraulics and place all machine
controls in neutral and engage the parking brake
before starting the engine.
• Become familiar with and know how to operate all
safety devices and controls on the machine and
attachment before attempting to operate. Know how
to stop the machine and attachment before starting
it.
• Repeated impact of the knives with hard objects can
cause excessive wear and damage to the skid-loader
or attachment. Be sure to maintain recommended
ground clearance as specified in this manual.
• Should excessive vibration occur, disengage the
auxiliary hydraulics immediately and shut off engine.
Do not continue to operate the attachment until the
problem has been determined and corrected.
•
Do not start, operate, or work on this attachment until
you have carefully read and thoroughly understand
the contents of this manual and the operator’s
manual for your machine.
• Keep children, bystanders and other workers off
and away from the machine and attachment during
operation. No riders allowed.
• Before inspecting, cleaning, lubricating, adjusting
or servicing any part of the attachment, always
exercise the Mandatory Shut-Down Procedure.
See “Mandatory Shut-Down Procedure” on page
5. After service has been performed, be sure to
restore all guards, shields and covers to their original
position.
• Make sure the operator’s area is clear of any
distracting objects. Keep work areas clean and free
of grease and oil to avoid slipping or falling.
Safety Instructions
Summary of Contents for Battle Ax Light
Page 2: ......
Page 4: ......
Page 8: ...2 Battle Ax Light Skid Loader OM...
Page 32: ...26 Battle Ax Light Skid Loader OM...
Page 33: ...27 Battle Ax Light Skid Loader OM PARTS IDENTIFICATION Parts Identification...
Page 57: ...51 Battle Ax Light Skid Loader OM Appendix Torque Specifications Inches Hardware and Lock Nuts...
Page 59: ......