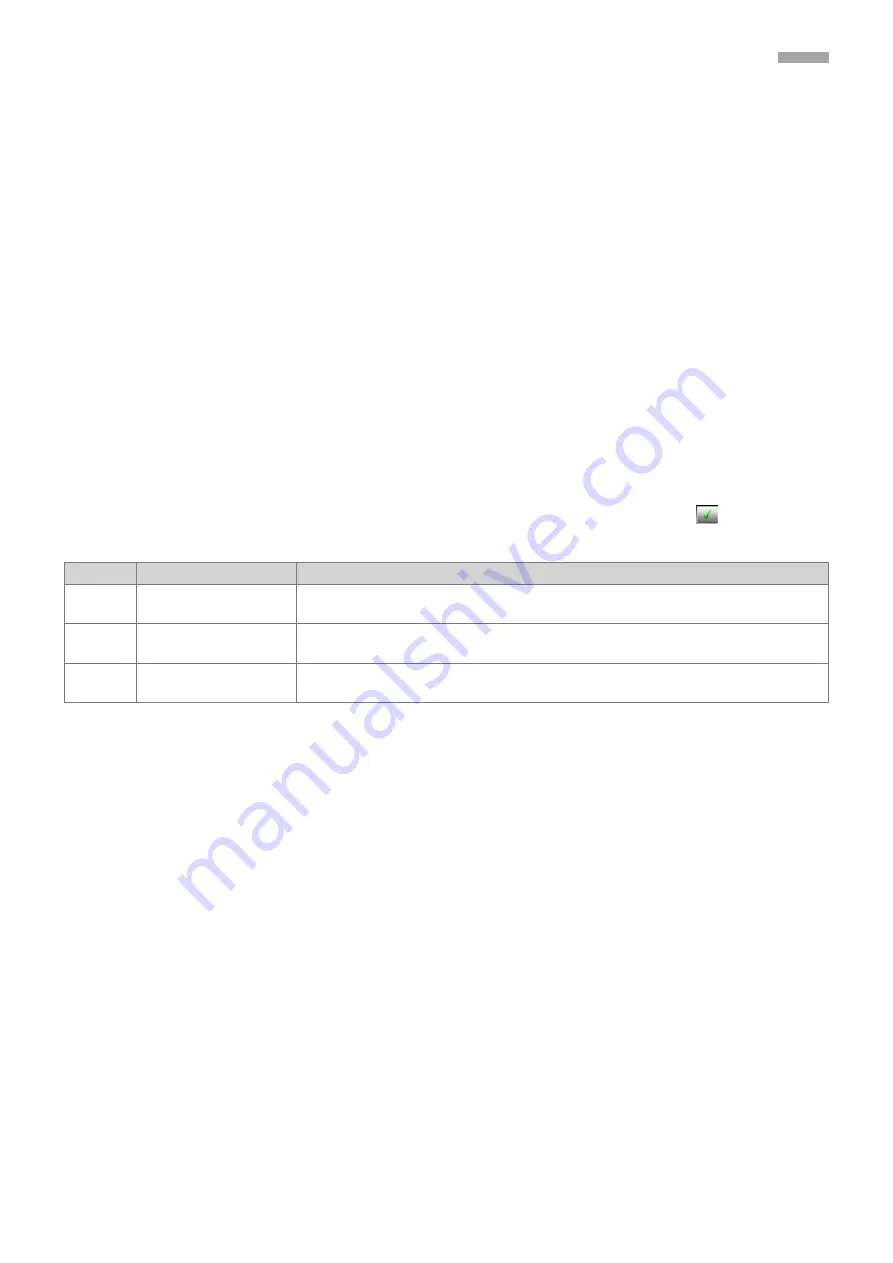
21
3N1
SYSTEM SETUP
System Setup
First Power Up
After completing the installation and safety checks for the Savio machine, power on the machine and both machine sides.
The following happens:
1. The SCU starts up.
If not, check the SCU power connection.
2. Within one minute, the LEDs of the SH of at least the first section show a running light.
3. The SCU downloads the SE-Unit software to SE-Units that are connected. This takes some minutes.
While downloading, the red LEDs of all SH blink simultaneously.
Caution:
During download, do not interrupt power!
Settings
Caution:
Touch the touch screen with bare finders only. Do not use any object or tool to touch the screen. Do not push hard on
the screen, nor hit it with a heavy or sharp object. Remove the protection foil of the SCU display (touch screen).
Next table lists the settings to be done. Enter the system or user password when it is requested. The system password is known
by Savio and Loepfe installers only. The default user password is “123”. Save settings by pressing OK or
.
Setting
Where?
Do what?
Date and
Time
Setup
menu >
System
Date / Time
Select the current date, set current time and select the time zone.
Number
of spindles
Service
menu >
Machine
Configuration
>
Side(s)
Enter the number of spinning units of each machine side.
Note:
After saving the settings, the picture in the
Machine Overview
page is adapted.
Number
of piecers
Service
menu >
Machine
Configuration
>
Side(s)
Enter the mumber of piecers.
Note:
3N1 can generate Q-reports per piecer.
Note:
Other configuration settings are set in accordance with or by the customer.
System Test
Cable Test
Now all detector LEDs should show a running light, which indicates that they are addressed by the SCU.
Power off and check cabling if sections fail to scan. Power on. A download will be started for newly connected
SE-Units.
Q-Lock Test
1. On the SCU, click Service, Diagnostics and open the Tests page.
2. In Left, click Start forced locks and enter rotor number 1 and the last rotor number of the machine side.
3. A Q-lock signal will start from spinning unit 1, left side. Both Q-detector LEDs will light up, and as a consequence, after ±8
seconds, the red light of the corresponding spinning unit will be on (machine must be running).
4. Write down the detector number if the order is wrong.
5. The sequence stops at the last spinning unit of this same side.
6. Same procedure for the right side.
7. Correct cable errors.
8. Repeat the Q-lock test until detector LEDs and stop lamps light up correctly.
9. Reset the detector LEDs: click Setup, Production and then click Lot Change for the side/s under test.
Summary of Contents for YARNMASTER 3N1
Page 1: ...YARNMASTER 3N1 46376003en Fitting Instruction RIFA RS40...
Page 2: ......
Page 4: ...4 3N1 INHALTSVERZEICHNIS...