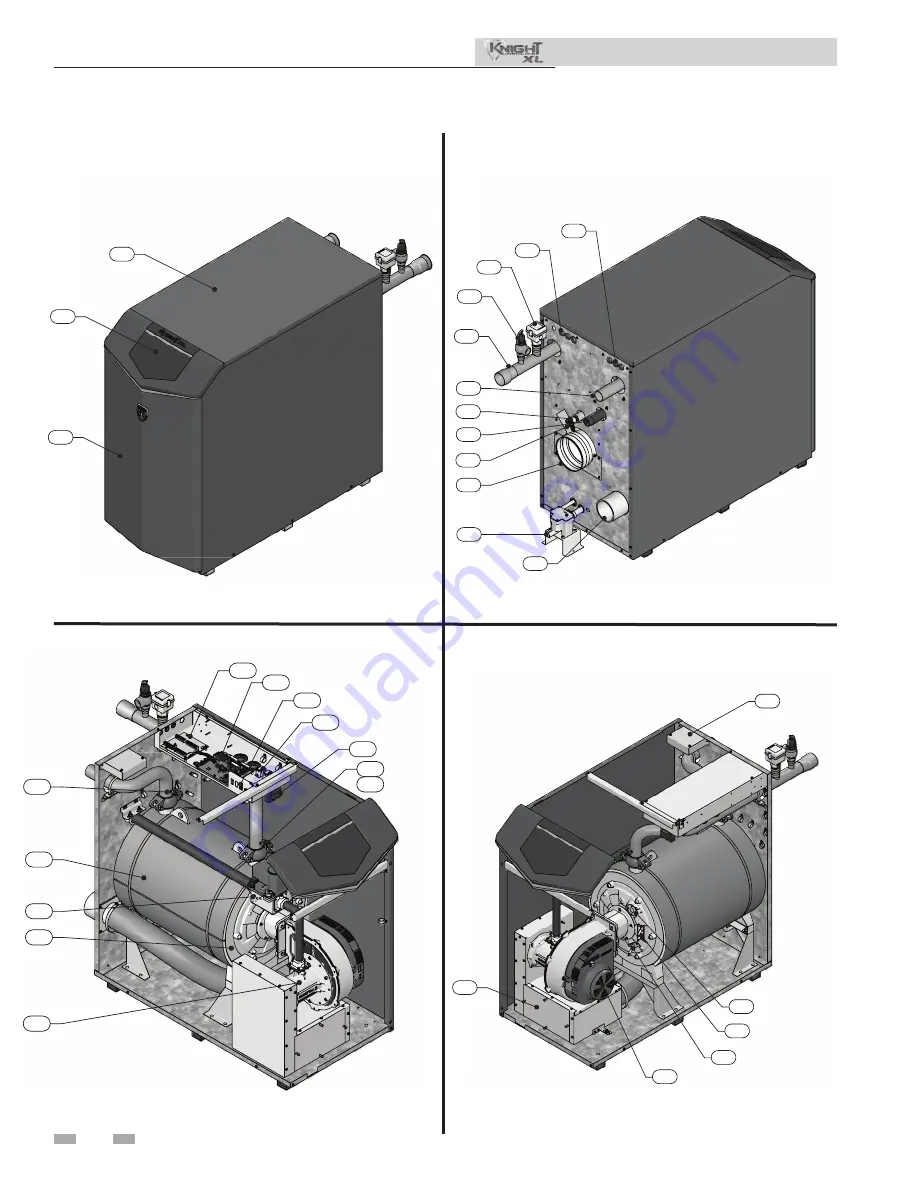
6
The Knight XL - How it works...
DIR #2000582923 00
DIR #2000582923 00
DIR #2000582923
00
29
10
23
Front View - Model 1000
DIR #2000582932 00
1
2
4
5
20
33
30
34
7
8
35
16
Rear View - Model 1000
Left Side (inside unit) - Model 1000
Left Side (inside unit) - Model 1000
Model 650 - 1000
DIR #2000582924 00
21
26
13
14
15
11
22
19
28
6
17
37
DIR #2000582937 00
31
18
24
27
3
25
Installation & Operation Manual