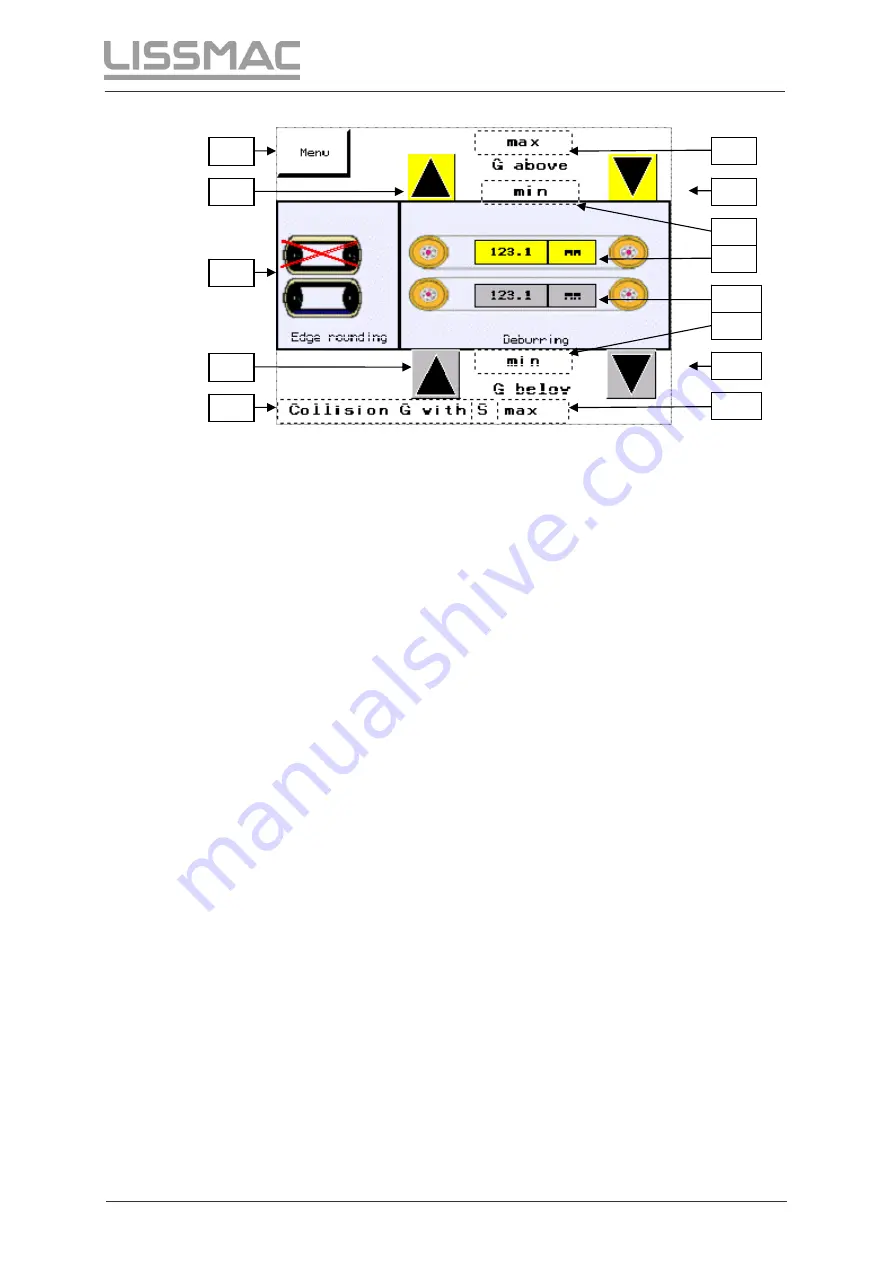
Operation
Grinding Machine SBM-L 1000+1500 G1S2 ALU MIX
41
Abb. 30:
Display – lower G-unit
1
Menu (see 5.3.2)
2
Button for moving the upper G unit upwards.
3
Button for changing to lower S unit.
4
Button for moving the lower G unit upwards.
5
Display only appears if the lower G axle and lower S axle have
collided.
6
Display appears if the maximum position of the upper G unit has
been reached.
7
Button for moving the upper G unit downwards.
8
Display appears if the minimum position of the upper G unit has
been reached.
9
Current position of the upper G axle.
10 Current position of the lower G axle.
11 Display appears if the minimum end position of the lower G unit
has been reached.
12 Button for moving the lower G unit downwards.
13 Display appears if the maximum end position of the lower G unit
has been reached.
1
3
4
5
2
7
6
8
9
13
12
11
10
Summary of Contents for SBM-L 1000 G1S2 ALU MIX
Page 2: ......
Page 15: ...Safety Grinding Machine SBM L 1000 1500 G1S2 ALU MIX 15 Notes...
Page 82: ......