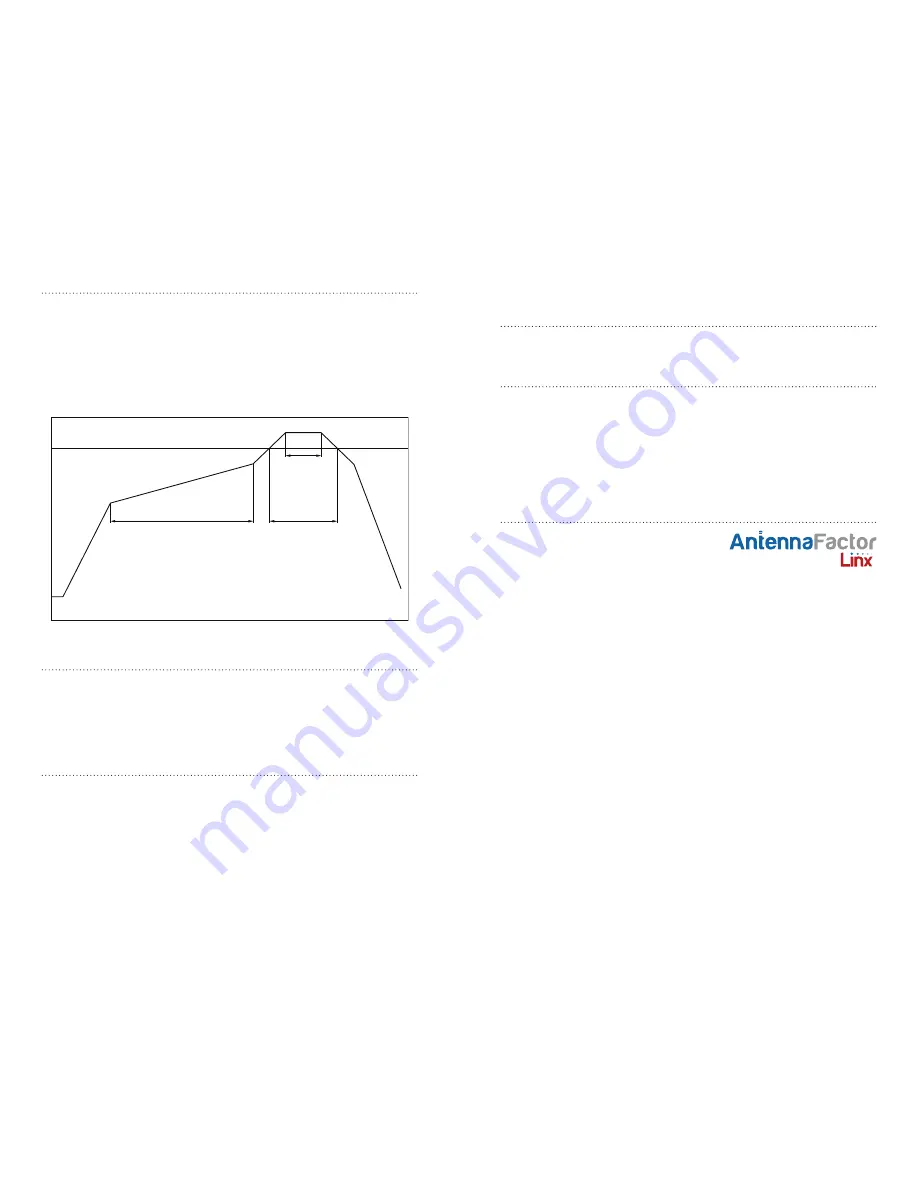
– –
– –
30
31
Resources
Support
For technical support, product documentation, application notes, regulatory
guidelines and software updates, visit www.linxtechnologies.com
RF Design Services
For customers who need help implementing Linx modules, Linx offers
design services including board layout assistance, programming,
certification advice and packaging design. For more complex RF solutions,
Apex Wireless, a division of Linx Technologies, creates optimized designs
with RF components and firmware selected for the customer’s application.
Call +1 800 736 6677 (+1 541 471 6256 if outside the United States) for
more information.
Antenna Factor Antennas
Linx’s Antenna Factor division has the
industry’s broadest selection of antennas
for a wide variety of applications. For
customers with specialized needs, custom
antennas and design services are available
along with simulations of antenna performance to speed development.
Learn more at www.linxtechnologies.com.
by
Reflow Temperature Profile
The single most critical stage in the automated assembly process is the
reflow stage. The reflow profile in Figure 36 should not be exceeded
because excessive temperatures or transport times during reflow will
irreparably damage the modules. Assembly personnel need to pay careful
attention to the oven’s profile to ensure that it meets the requirements
necessary to successfully reflow all components while still remaining
within the limits mandated by the modules. The figure below shows the
recommended reflow oven profile for the modules.
Shock During Reflow Transport
Since some internal module components may reflow along with the
components placed on the board being assembled, it is imperative that
the modules not be subjected to shock or vibration during the time solder
is liquid. Should a shock be applied, some internal components could be
lifted from their pads, causing the module to not function properly.
Washability
The modules are wash-resistant, but are not hermetically sealed. Linx
recommends wash-free manufacturing; however, the modules can be
subjected to a wash cycle provided that a drying time is allowed prior
to applying electrical power to the modules. The drying time should be
sufficient to allow any moisture that may have migrated into the module
to evaporate, thus eliminating the potential for shorting damage during
power-up or testing. If the wash contains contaminants, the performance
may be adversely affected, even after drying.
Preheat:
150 - 200°C
Peak: 240+0/-5°C
25 - 35sec
220°C
2 - 4°C/sec
120 - 150sec
2 - 3°C/sec
60 - 80sec
30°C
Figure 36: Maximum Reflow Temperature Profile