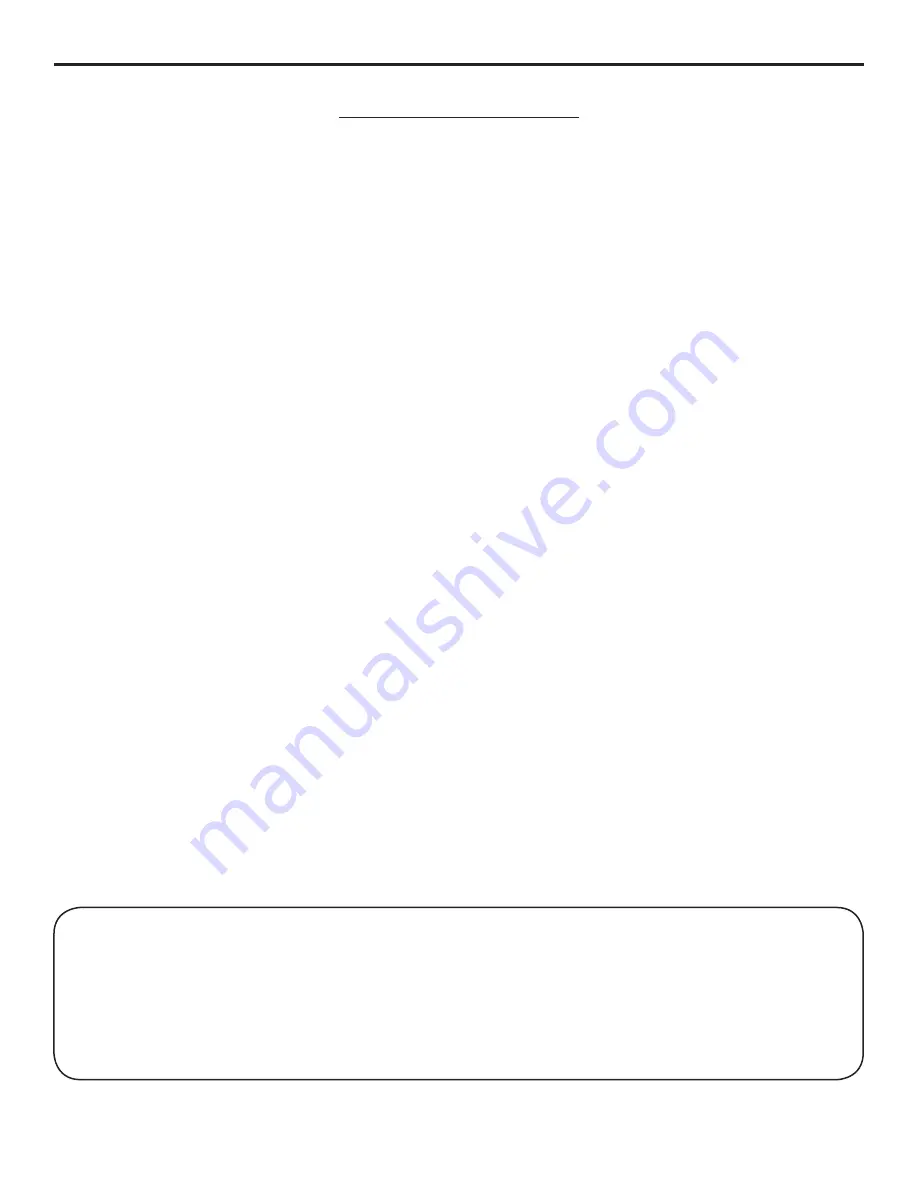
GSLG-A OPERATOR INSTALLATION GUIDE
- 24 -
TROUBLESHOOTING
Operator fails to start:
A. If the operator has been running a large number of cycles,
the motor may have gotten hot and tripped the overload.
Allow the motor to cool down and the overload will reset
automatically.
B. Make sure you have power at the master distribution panel
and that the power has not been turned off.
C. The secondary fuse on the control board may have blown.
Replace the fuse (refer to control box parts list on page
26
for part number information).
Motor operates, but gate does not move:
A. In operators with torque limiters and friction pad clutches,
check for signs of slipping. You can mark the sprocket and
clutch with a yellow or white grease pen and watch for the
lines to move apart if slipping is taking place. Adjust the
torque limiter tighter if this is the problem.
B. Check for broken chain or worn belts.
C. Check all setscrews on pulleys and sprockets and tight-
en them if necessary, and check for keys which may
have fallen loose from keyways.
Motor sounds like it is working harder than normal:
A. Make sure the gate is moving freely and without binding
throughout its entire travel.
B. Check the drive chain for obstructions (if the operator has
one).
C. If the operator has an internal brake mechanism, make
sure it is releasing.
Limit switch getting out of time:
A. Check for proper tension on all limit chains to be sure
there is no jumping taking place. Mark one tooth and its
corresponding link and run the gate. If the marks have
moved, the chain is skipping.
B. Check the setscrews in limit cams and limit sprockets for
tightness. In rotary limit boxes, check the rotary limit nut
for sloppiness or stripped threads. Replace if necessary.
C. Check the chain tension along the output sprocket and
idlers. Mark the chain and one tooth of the sprocket as
described above and run the gate. Check for jumping.
Gate stopping part way open or closed
(but no visible obstruction):
A. The control board may have received a false obstruction
input triggered by current sensing set too low. Make sure
the gate moves freely through its entire travel before ad-
justing the current sensing.
B. The maximum run timer may have counted down and
expired. This can be caused by having the timer set too
low, if a chain or belt is broken, or if a sprocket or pulley
is slipping. When the timer expires, the gate stops and an
alarm will sound.
C. An obstruction signal from an accessory wired to the
obstruction input may have triggered falsely. Check the
control board for lit L.E.D. indicators for any of the following
inputs: safety, shadow, open obstruction, close obstruc-
tion, stop, etc. If any are lit when the operator should be
running, remove all devices hooked to that function and
hook them up one at a time and try to run the operator
until the problem device is found. Refer to page
12
for
details on the control board indicators.
Gate staying open with automatic system:
A. If there are vehicle detectors in your machine which are
set up for reverse, one of your loops or loop detectors may
be sending a false signal. Disconnect the wire harness
and try running the operator.
B. An opening or reversing device may be stuck or malfunc-
tioning. Try disconnecting these devices and hook them
back up one at a time and try running the operator until
the malfunctioning device is found.
C. Make sure the close limit switch isn’t activated. If it is, the
operator will think the gate is already closed.
D. Make sure operator is on full open limit switch, unless
close from any position is enabled. See wiring diagram.
E. If the stop or reset button is pressed, the timer is disabled
until another run command is received.
HOW TO ORDER REPLACEMENT PARTS
Use the part numbers listed on the following pages. Contact your
local LINEAR dealer
or
distributor
to order parts.
1. Supply the model number and serial number of your operator.
2. Specify the quantity of pieces needed and order by part number and name of part.
3. State whether to ship by freight, truck, parcel post, UPS or air express.
4. State whether transportation charges are to be prepaid or collect.
5. Specify name and address of person or company to whom parts are to be shipped.
6. Specify name and address of person or company to whom invoice is to be sent.
Summary of Contents for GSLG-A
Page 14: ...GSLG A OPERATOR INSTALLATION GUIDE 14 CONTROL and ACCESSORY CONNECTION ILLUSTRATIONS...
Page 15: ...GSLG A OPERATOR INSTALLATION GUIDE 15 CONTROL and ACCESSORY CONNECTION ILLUSTRATIONS...
Page 16: ...GSLG A OPERATOR INSTALLATION GUIDE 16 CONTROL and ACCESSORY CONNECTION ILLUSTRATIONS...
Page 17: ...GSLG A OPERATOR INSTALLATION GUIDE 17 CONTROL and ACCESSORY CONNECTION ILLUSTRATIONS...
Page 23: ...GSLG A OPERATOR INSTALLATION GUIDE 23 TRACK GATE ILLUSTRATION...
Page 25: ...GSLG A OPERATOR INSTALLATION GUIDE 25 MODEL GSLG A MECHANICAL PARTS EXPLODED VIEW...
Page 31: ...GSLG A OPERATOR INSTALLATION GUIDE 31 This page intentionally left blank...