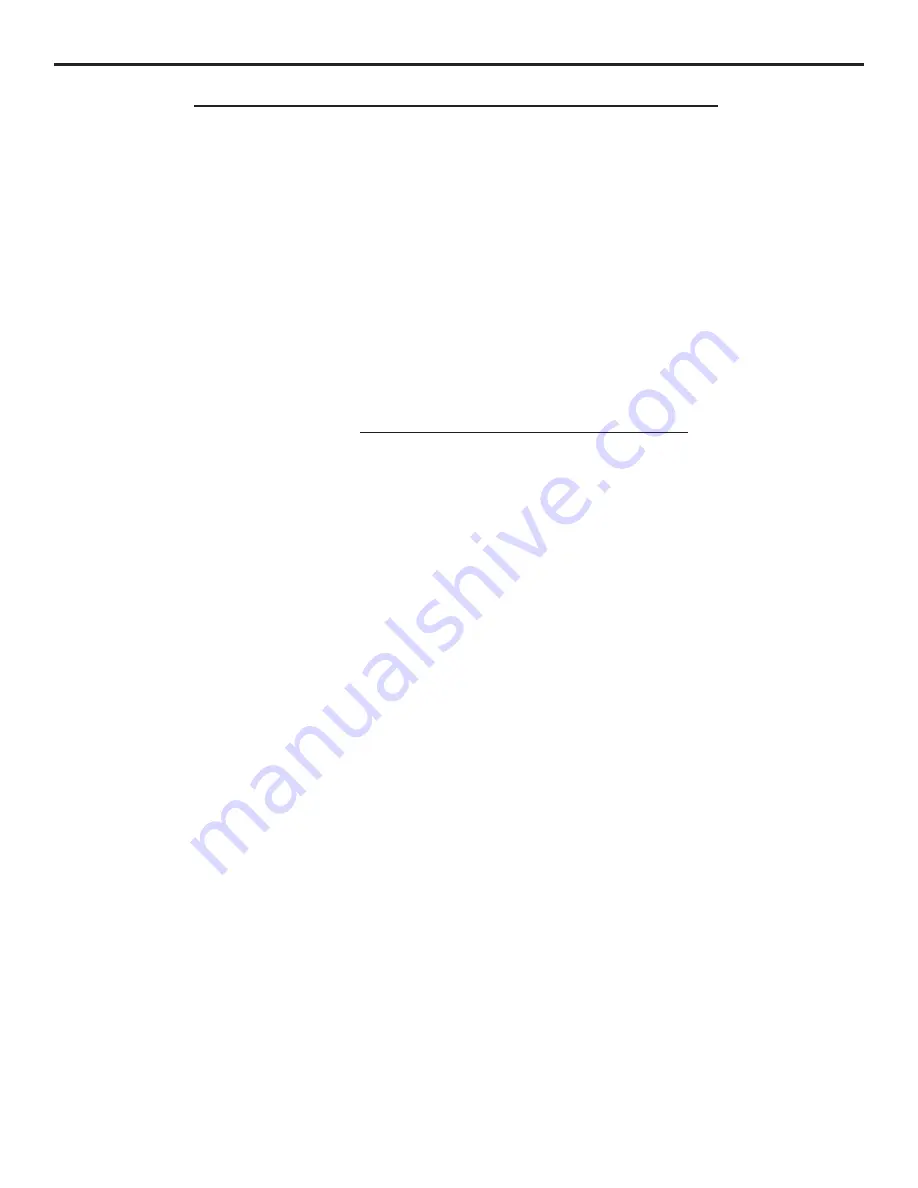
GSLG-A OPERATOR INSTALLATION GUIDE
- 32 -
By signing this installation checklist, I/we hereby certify that each item listed and checked above has been covered by the
installer and is clearly understood by the customer.
______________________________________________ _____________________________
Customer
Signature
Date
______________________________________________ _____________________________
Installer
Signature
Date
GATE OPERATOR INSTALLATION CHECKLIST
1. The gate has been checked to make sure it is level and moves freely in both directions.
2. Potential pinch areas have been guarded so as to be inaccessible
OR
have contact and/or
non-contact obstruction sensing devices installed.
3. The installer has installed one or more contact or non-contact obstruction sensing devices,
in compliance with UL325 requirements for this installation.
4. The slide gate has been screened or secured from the bottom of the gate to a minimum of
48 inches above ground to prevent a 2 1/4-inch sphere from passing through the openings
anywhere in the gate and in that portion of the adjacent fence that the gate covers when
the gate is in the open and closed positions. Picket gates which have spacings less than 2
1/4 inches apart to the minimum height requirement are also acceptable.
5. Roller covers have been installed on cantilever gates.
6. Pedestrians have been supplied with a separate access opening. The customer has been
informed that all
pedestrian traffi c must use the pedestrian gate.
7. Two (2) warning signs have been installed, one on each side of the gate in easily visible
locations. The customer has been informed that these signs must remain at all times.
8. Controls intended for user activation are located at least six feet (6’) away from any mov-
ing part of the gate and where the user is prevented from reaching over, under, around
or through the gate to operate the controls. Outdoor or easily accessible controls have a
security feature to prevent unauthorized use.
9. The installer has properly adjusted the obstruction sensing feature and has tested the gate
to make sure that the gate stops and reverses a short distance with minimal resistance
applied (40 lbs. on a swing gate at the end of the gate, 75 lbs. on a slide gate)
10. The installer has instructed the customer in the proper use of the gate operator and reviewed
all of the operational functions, obstruction sensing devices, warning beeper and reset,
etc.
11. The installer has instructed the customer in the proper use of the operator’s manual discon-
nect feature. The manual disconnect must never be used while the gate is in motion. The
power switch must be turned off before using the manual disconnect and disengaging the
operator.
12. The installer has reviewed all safety instructions with the customer, and has left the safety
instructions and owner’s information sheets for their reference.
13. The installer has answered any questions the customer has regarding the operation of the
gate operator and gate operator safety precautions.
14. The installer has explained to the customer that a regular maintenance schedule for both
the gate and the gate operator is recommended.
________ ________
________ ________
________ ________
________ ________
________ ________
________ ________
________ ________
________ ________
________ ________
________ ________
________ ________
INSTALLER
CUSTOMER
________ ________
________ ________
________ ________
P560 SEPT. 08
Summary of Contents for GSLG-A
Page 14: ...GSLG A OPERATOR INSTALLATION GUIDE 14 CONTROL and ACCESSORY CONNECTION ILLUSTRATIONS...
Page 15: ...GSLG A OPERATOR INSTALLATION GUIDE 15 CONTROL and ACCESSORY CONNECTION ILLUSTRATIONS...
Page 16: ...GSLG A OPERATOR INSTALLATION GUIDE 16 CONTROL and ACCESSORY CONNECTION ILLUSTRATIONS...
Page 17: ...GSLG A OPERATOR INSTALLATION GUIDE 17 CONTROL and ACCESSORY CONNECTION ILLUSTRATIONS...
Page 23: ...GSLG A OPERATOR INSTALLATION GUIDE 23 TRACK GATE ILLUSTRATION...
Page 25: ...GSLG A OPERATOR INSTALLATION GUIDE 25 MODEL GSLG A MECHANICAL PARTS EXPLODED VIEW...
Page 31: ...GSLG A OPERATOR INSTALLATION GUIDE 31 This page intentionally left blank...