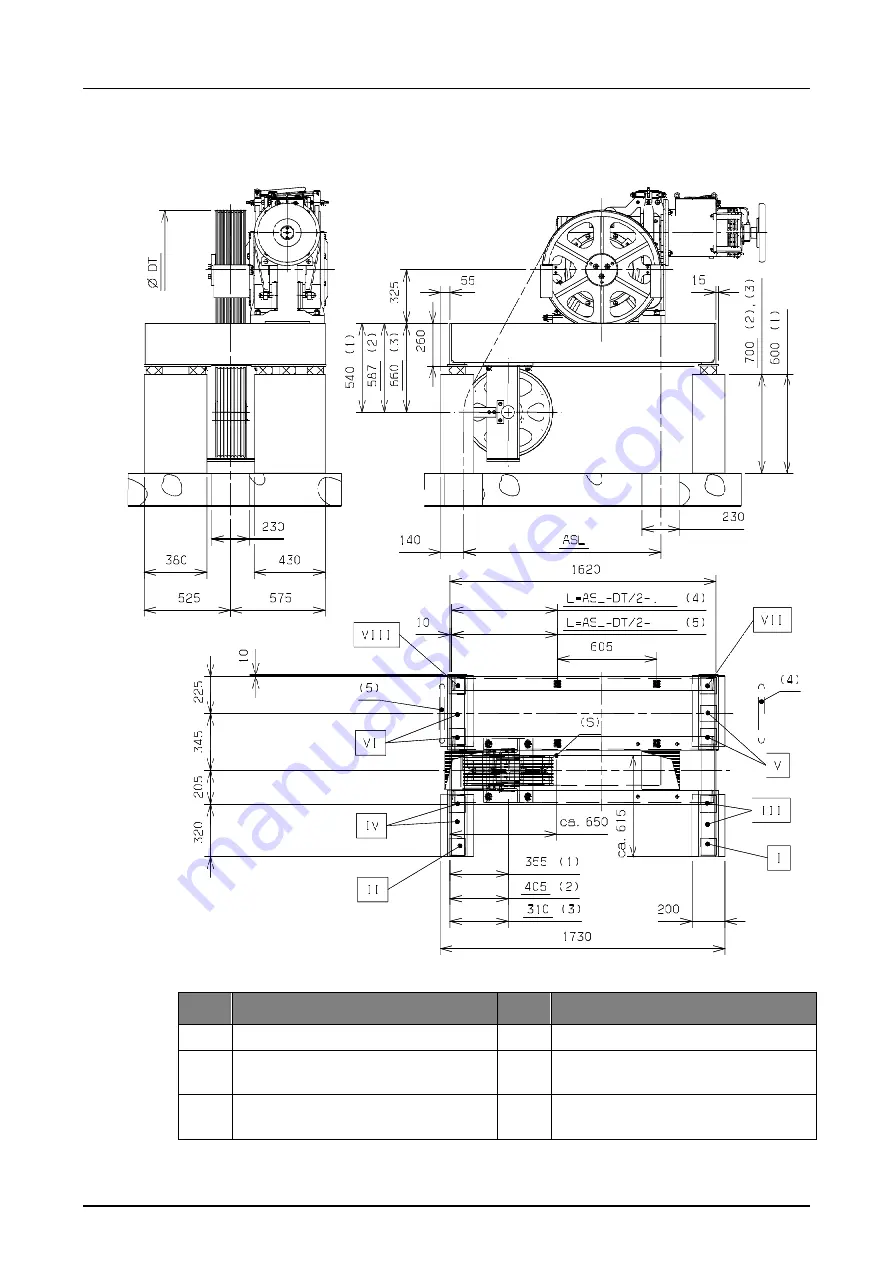
Operating manual
Technology
TW160 drive
TK Aufzugswerke
46
Version 08/2021
4.6.3
Version with rope pulley / machine base frame on concrete foundation
Version with rope pulley position on left
Item Designation
Item Designation
1
With rope pulley D540
2
With rope pulley D640
3
With rope pulley D450
4
Machine with traction sheave
position - left
5
Machine with traction sheave
position - right
S
Centre of gravity, machine base
frame
Fig. 4.6-4
TW160_31104_GER
185
250
Summary of Contents for TW160
Page 1: ...OPERATING MANUAL TW160 Drive 08 2021 6234002860...
Page 6: ......
Page 24: ...Operating manual Technology TW160 drive TK Aufzugswerke 24 Version 08 2021...
Page 101: ......
Page 102: ......
Page 103: ......
Page 104: ...Tachogenerator RE 0444 zu SA 1 Anschlusshinweis...
Page 107: ......
Page 111: ...OPERATING MANUAL EMERGENCY BRAKE SYSTEMS NBS TW45 TW63 TW130 TW160...