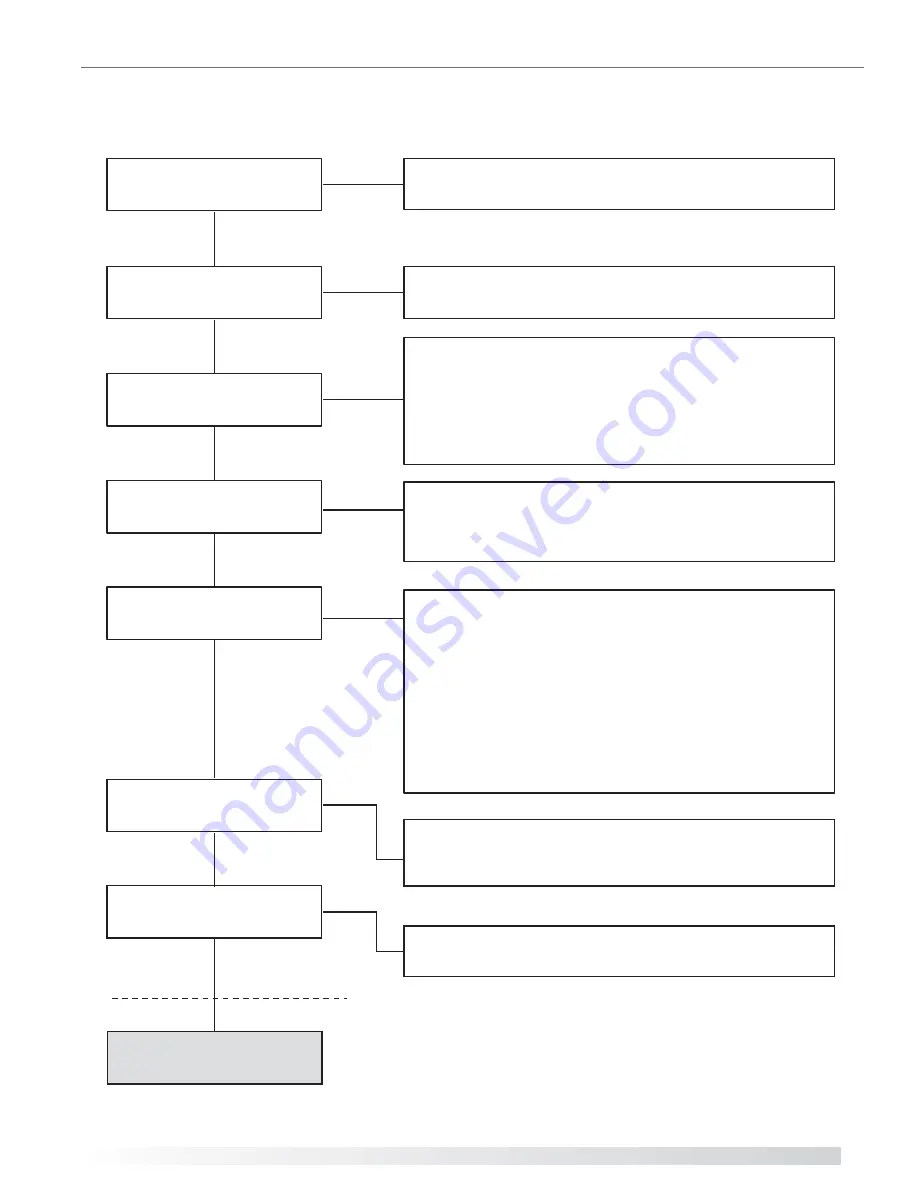
Troubleshooting - 4:1 Modulating Furnace
4:1 Modulating Furnace with Stand-Alone Controller Will Not Light
In all cases, verify correct terminals as shown on the unit-specific wiring diagram.
Line voltage across L1 & L2,
L2 & L3, and L1 & L3 on main
No
disconnect (DS1)?
Main incoming power not connected
Connect proper supply power to unit
Yes
Line voltage across T1 & T2,
T2 & T3, and T1 & T3 on main
No
disconnect (DS1)
Main disconnect (DS1) open or defective
Close, repair, or replace
Yes
24 VAC across R and C?
No
Yes
24 VAC across G and C?
No
Yes
Main transformer (TR1) fault
Reset
or replace main transformer
Phase
Monitor (PM) Contact Open
Correct
incoming phase order
Fuse (FU6) Blown
Test and replace blown fuse(s)
Fan Switch (S2) open or not wired
Close or wire fan switch
(If fan switch is not required, place jumper from R to G)
Supply fan running?
No
Yes
24 VAC across W1 and C?
No
Yes
Freeze protection tripped
Cycle disconnect to reset
Supply fan overload tripped
Push reset button on overload or VFD to reset.
Check motor amp draw and correct as necessary
Damper limit switch (D1L) not closed -
Damper stuck closed or actuator failed
Repair damper interference or replace actuator
Exhaust fan contactor not powered
Close or wire exhaust switch, reset exhaust overload, or replace faulty
exhaust contactor.
Heat Switch (S4) open or not wired
Close or wire heat switch
(If heat switch is not required, place jumper from R to W1)
24 VAC across A2 and A1
No
on the RH relay?
Starter interlock (ST1) not closed
Replace contactor
Unit Main
Furnace Board
Yes
Continues on next page...
Summary of Contents for AR-DE12-05A
Page 75: ...Gas Supply In Typical Split Burner Manifold ...
Page 94: ...NOTE For HMA gas furnace for 311 and 352 chassis see separate IOM Manual ...
Page 96: ...HANDHELD KEYPAD DISPLAY OPTIONAL ...
Page 105: ......
Page 107: ......
Page 108: ......
Page 109: ......
Page 110: ......
Page 111: ......
Page 112: ......
Page 113: ......
Page 114: ......
Page 115: ......
Page 116: ......
Page 117: ......
Page 118: ......
Page 119: ......
Page 120: ......
Page 121: ......
Page 122: ......
Page 123: ......
Page 124: ......
Page 125: ......
Page 126: ......
Page 127: ......
Page 128: ......
Page 129: ......
Page 130: ...Controls Sequence of Operation ...
Page 131: ......
Page 132: ......
Page 133: ......
Page 134: ......
Page 135: ......
Page 136: ......
Page 137: ......
Page 138: ......
Page 139: ......
Page 140: ......
Page 141: ......
Page 142: ......
Page 143: ......
Page 144: ......
Page 145: ......
Page 146: ......
Page 147: ......
Page 148: ......
Page 149: ......
Page 150: ......
Page 151: ......
Page 152: ......
Page 153: ......
Page 154: ......
Page 155: ......
Page 156: ......
Page 157: ......
Page 158: ......
Page 159: ......
Page 160: ......
Page 161: ......
Page 162: ......
Page 163: ......
Page 164: ......
Page 165: ......
Page 166: ......
Page 167: ......
Page 168: ......
Page 169: ......
Page 170: ......
Page 171: ......
Page 172: ......
Page 173: ......
Page 174: ......
Page 175: ......
Page 176: ......