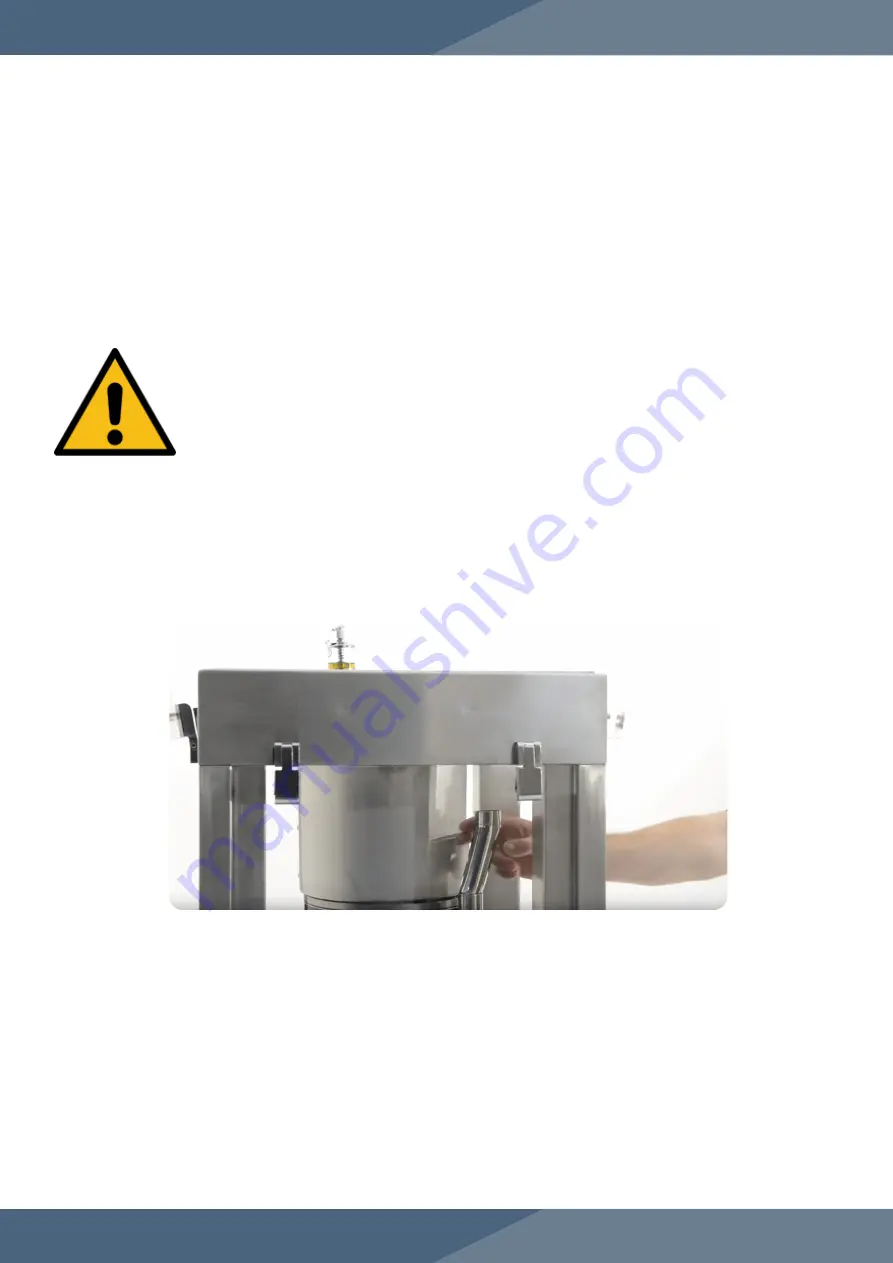
46
Take-Off Blade and Force Feeder Scraper
The Take-Off Blade and Force Feeder Scraper are attached to the Force Feeder. They help keep
the powder flowing into the Dies' bores and aid in tablet ejection.
Tools and Materials Needed
• Crosshead screwdriver
• Wrench set
• New Take-Off Blade and Scraper part
• Disposable latex/rubber gloves (for food grade products and to protect hands from grease)
• Hairnet and/or beard net (food grade products only)
• Sterile shoe covers (food grade products only)
WARNING:
To prevent any potential personal injury, ALWAYS unplug the RTP
10i® from the electrical outlet when replacing parts.
Instructions
Note: Wear latex/rubber gloves (and appropriate food grade attire if applicable) during this process.
Remove the Take-Off Blade and Force Feeder Scraper
1. Raise each of the Perspex Casing's doors and lock them into an upward position.
2. Unscrew the Hopper to Force Feeder Connecting Pipe's bolt by hand and remove the
Hopper.
3. Remove the Hopper to Force Feeder Connecting Pipe.