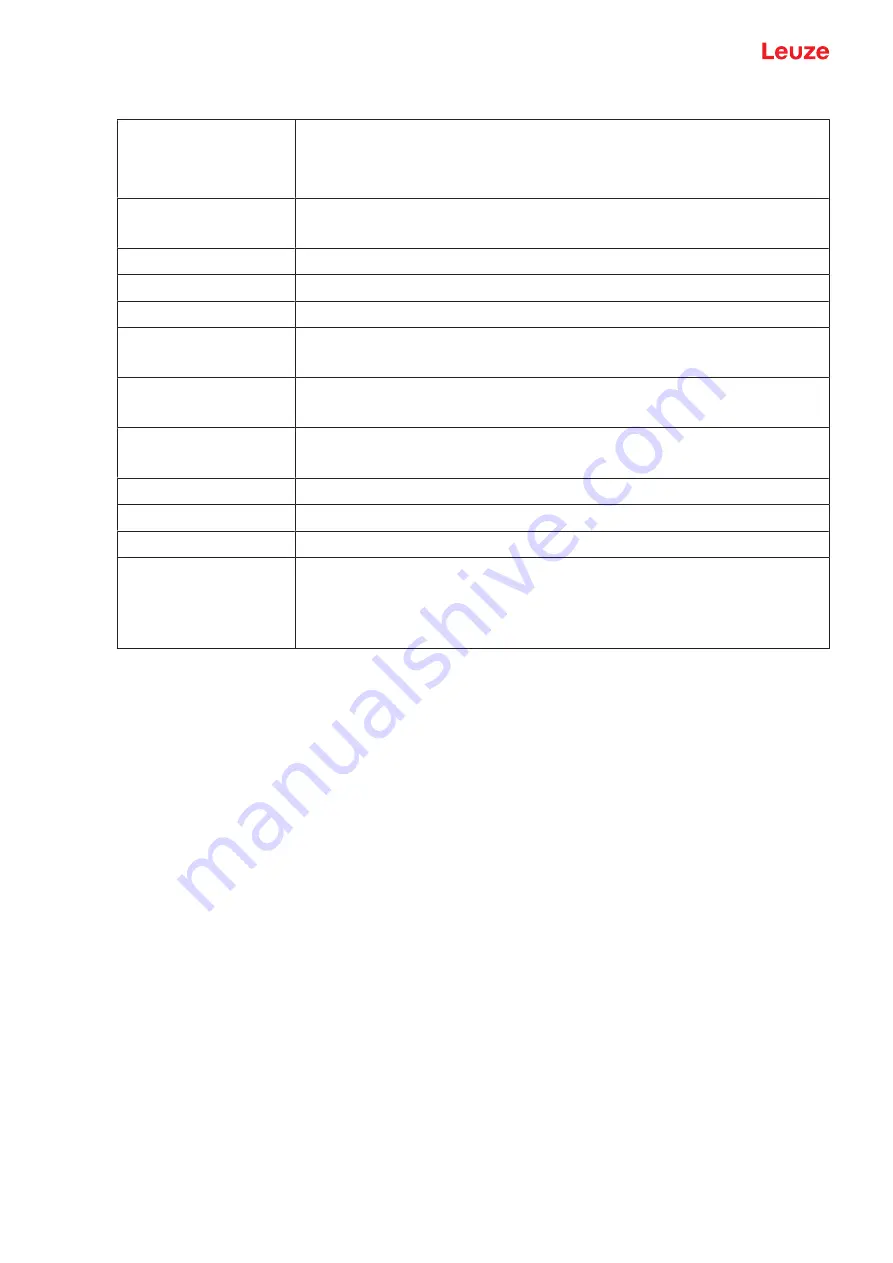
About this document
Leuze electronic GmbH + Co. KG
ELC 100
6
Tab. 1.3:
Terms and abbreviations
Response time
The response time of the protective device is the maximum time between the
occurrence of the event that results in activation of the safety sensor and the
provision of the switching signal at the interface of the protective device (e.g.,
OFF state of the OSSD pair).
AOPD
Active Optoelectronic Protective Device
(
A
ctive
O
ptoelectronic
P
rotective
D
evice)
ESPE
E
lectro-
s
ensitive
p
rotective
e
quipment
ELC
Brief description of the safety sensor, consisting of transmitter and receiver
LED
LED, display element in transmitter and receiver
MTTF
d
Mean time to dangerous failure
(
M
ean
T
ime
T
o dangerous
F
ailure)
OSSD
Safety-related switching output
(
O
utput
S
ignal
S
witching
D
evice)
PFH
d
Probability of a dangerous failure per hour
(
P
robability of dangerous
F
ailure per
H
our)
PL
P
erformance
L
evel
Safety sensor
System consisting of transmitter and receiver
SIL
S
afety
I
ntegrity
L
evel
State
ON: device intact, OSSD switched on
OFF: device intact, OSSD switched off
Locking: device, connection or control / operation faulty, OSSD switched off
(lock-out)
1.2
Checklists
The checklists (see chapter 8 "Testing") serve as a reference for the machine manufacturer or supplier.
They replace neither testing of the complete machine or system prior to initial commissioning nor their peri-
odic testing by a qualified person (Necessary competencies). The checklists contain minimum testing re-
quirements. Depending on the application, other tests may be necessary.