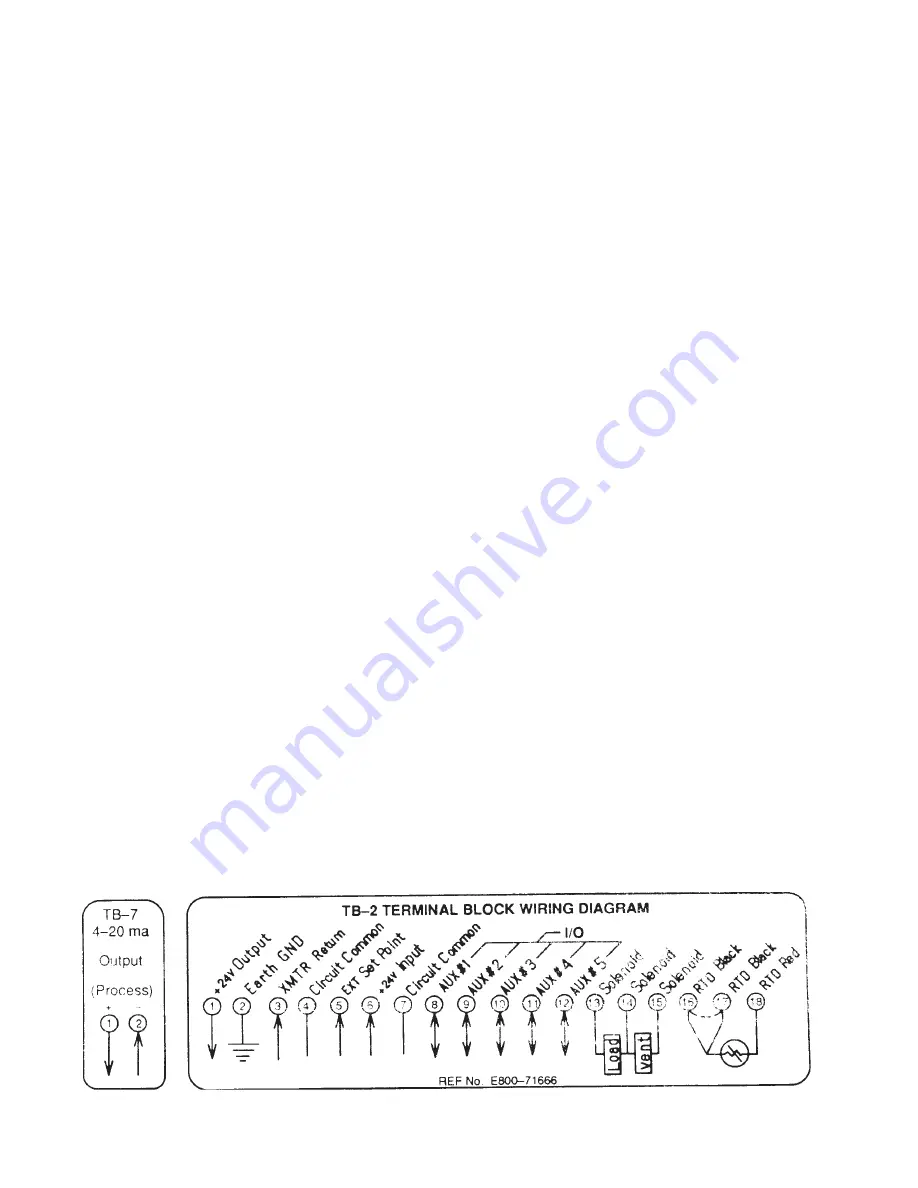
WARNING
- Electrical power must be supplied
through an external circuit breaker or fuse protection.
An external switch must be provided to turn off
power. Always turn off power before removing the
internal field wiring panel.
Pneumatic connections:
Connect air supply and output lines to the 1/8” NPT
connections at the bottom of the controller The center
connection is for air exhaust and is supplied with a porous
metal filter/silencer which should not be removed.
Corrosion resistant 3/8 in. O.D. tubing or 1/4 in. pipe is
recommended for the air lines. Connect air supply to the
right hand connection labeled “Input” and output to left
hand connection labeled “Output” to actuator. See Figure 1.
The supply line should be fitted with a pressure gauge and 50
micron filter/regulator to remove any floating particles. If the
supply air is mixed with traces of oil, a filter capable of
removing oil should be used. (CAUTION: Some lubricating
oils permanently damage solenoid valves.)
W A R N I N G
- Turn off electrical power before
removing the internal field wiring panel
Field Wiring:
1.
After mounting the PMC-1 at the desired location, open
the cover by loosening 5 screws and the thumb screw.
Then remove the field wiring panel by loosening two
captive screws. The terminal block wiring diagram
shown in Figure 2 appears on the back of the panel.
Power and signal lines should be routed through
separate conduits to avoid interference. Transmitter or
RTD signal lines should use shielded cable grounded at
terminal 2 in insure against RF interference.
2.
Connect the transmitter wires as shown in Figure 3 . A
two wire transmitter should be powered with the 24v DC
supply from the PMC-1 by connecting the positive wire
to terminal number 1 and the other transmitter wire to
terminal 3 of TB-2. Twisted pair wires can be used for
connecting the transmitter to the PMC-1. If a shielded
pair of wires is used,connect the shield to terminal 2 of
TB-2. Jumper at J5/J6 must be on J5. For 4-wire
transmitters,see Appendix B.
3.
For external set point connection (4-20mA) connect two
wires to terminals 5 and 4 of TB-2. Terminal 5 is positive
(current flows into terminal 5) and terminal 4 is
negative. (See Figure 4)
A. Introduction
The Leslie PMC-1 electro-pneumatic controller can be used
to control pressure, temperature. liquid level, and other
process variables. It accepts signals from any standard 4-20
mA transmitter and provides a pneumatic output to operate a
diaphragm control valve, etc. It provides the following
features:
1)
The controller supplies 24 volt D C. power for the
transmitter, eliminating the need for a separate D.C.
power supply.
2)
It provides high volume air output at pressures up to 100
psig to directly operate a diaphragm control valve. I/P
transducers and valve positioners are not required or
recommended.
3)
There are no small air orifices to plug or foul (.060” dia.
solenoid ports)
4)
There is no air consumption except when air is being
loaded onto the control valve diaphragm.
B. Operation
The electronic circuit of the controller compares the signal
from the transmitter to the desired set point. If the error is
greater than the dead band, electrical pulses are sent to one
of the two internal air solenoid valves. One valve increases
output air pressure and the other bleeds it. Each time a pulse
is received, the resulting pressure on the diaphragm of the
control valve increases or decreases slightly. If the error is
large, the solenoid valves are held open longer to increase the
speed of output changes. For small errors, the pulse width is
decreased to prevent overshoot. The response speed
adjustment can be used to control how quickly the output
changes for a given error. Adjusting the dead band will allow
the controller to ignore small changes or “noise” in the
system. The overall result is a more accurate and stable
system.
C. Installation
Mount the controller in a location that will allow access to
the internal adjustments. See Figure 1 for mounting
dimensions. It should be mounted in a location where the
temperature will be between -4°F and 140°F. Temperatures
above or below these limits will affect the LCD although the
controller would continue to function. A location within 50
ft. of the control valve is recommended to reduce time lags in
the pneumatic signal. Where the distance to the control valve
is large, an optional external solenoid valve package (PMC-1
local control module model RCS-90) can be used.
FIGURE 2
4