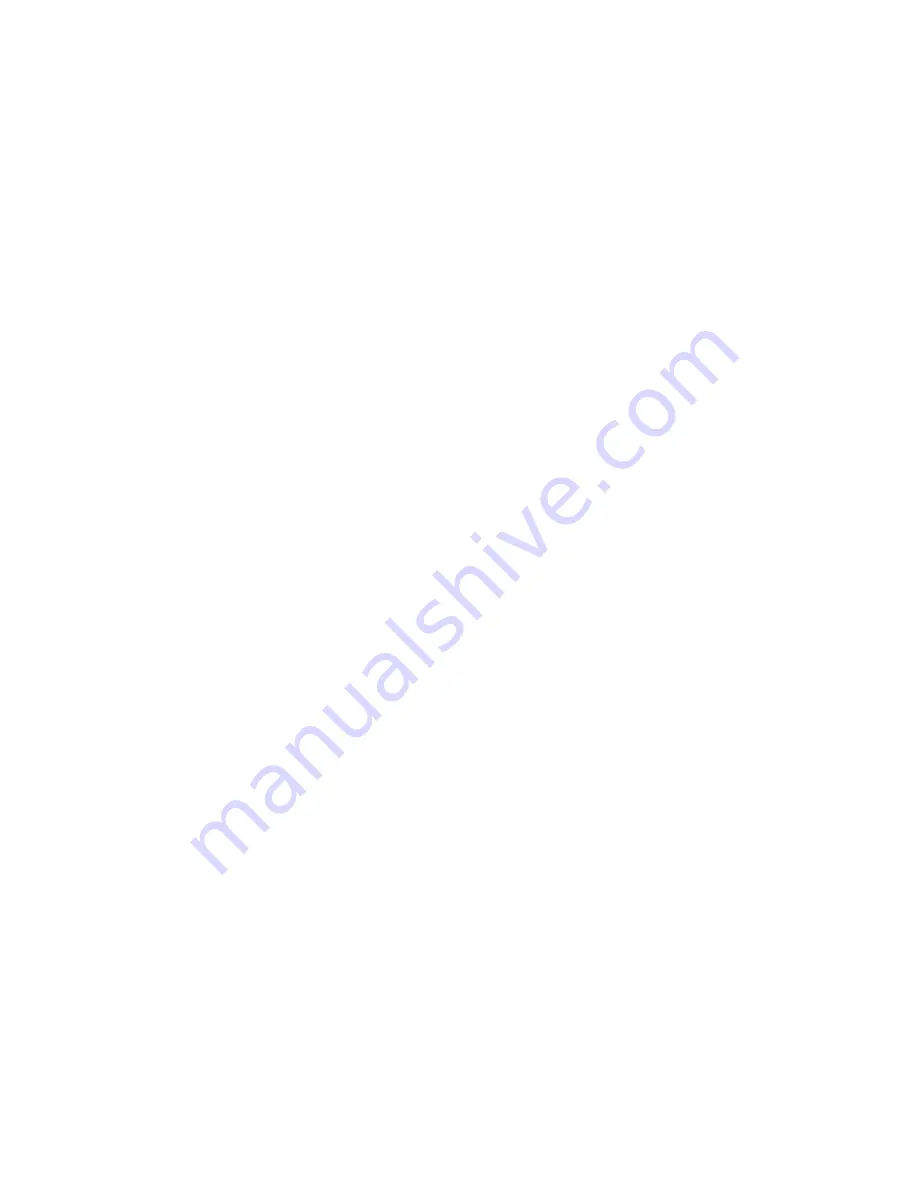
8
2)
Control valve operates in the opposite direction required
to satisfy the system .
a) Check position of direct/reverse switch.
3)
Controller does not operate at all (LCD display off).
a) Check A.C. power connection.
b) Check fuse (F1 in Figure 2).
c) PMC-1 operates but no display, replace LCD display.
4)
Controller does not respond to changes in local set point
adjustment.
a) Check that the set point jumper is in the local
position.
5)
Controller does not respond to changes in the controlled
variable.
a) Check connections and signal from transmitter.
b) Re-check LO-HI calibration and set point.
6)
The displayed process value does not match the actual
when measured against thermometer or pressure gauge.
a) Check display calibration (step 9 of start-up
instructions).
b) Check calibration of transmitter. (See instructions
supplied with transmitter).
c) Remember, the accuracy of the PMC-1 is ±.5% of span
(much better than most gauges or thermometers).
For example, if calibration was from 32-212°F, the
span is 180° so the indicated temperature of the PMC-
1 would be within (.005 x 180) .9°F of actual.
7)
Control valve does not respond to controller output.
a) Check filter/regulator supplying air to controller to
make sure that the output pressure is 5-10 psig higher
than the pressure required to fully stroke the valve.
b) Check actuator operation.
8)
Process never quite makes the set point.
a) Check pneumatic connections for leaks.
For Temperature Control Systems
1)
RTD connection to PMC-1
a) If an RTD is being used, make sure that the wires are
connected according to the diagram in the PMC-1
Installation and Operation Manual. If in doubt,
measure the resistance across the terminals, as shown
in Figure 5.
2)
RTD installation in piping
a) If the process temperature indicated by the PMC-1 (a
function of the RTD signal) lags considerably behind a
thermometer installed in the process line, check to
make sure that the RTD is installed directly into the
flow path of the process fluid. Unless absolutely
necessary, the RTD should not be inside a thermowell.
If the above steps have been taken and the lag is still
too great, thermocouple with transmitter may be
necessary.
3)
RF interference
a) For best protection from radio frequency interference.
make sure that the temperature sensing element is
connected to the PMC-1 using shielded cable that the
shielding is connected to the earth ground.
4)
Insufficient air pressure to PMC-1
a) Make sure that the air pressure supplied to the PMC-1
is sufficient to fully stroke the control valve or to
provide the maximum outlet pressure required from a
regulator.
5)
Leaks in pneumatic lines
a) Small pneumatic line leaks can cause control
instability, particularly when using the PMC-1 with a
regulator. Use a soap solution or “snoop” to locate
possible leaks.
6)
Too much air pressure to PMC-1
a) If too much air pressure is supplied to the PMC-1, it
can overload the actuator or regulator diaphragm
causing overshoot and slow response when venting is
required.
7)
Inaccurate calibration
a) If the process temperature indicated by the PMC-1 is
significantly different from the temperature indicated
by a thermometer, check to make sure that the PMC-
1 is calibrated according to the range of the signal
conditioning card installed (if using an RTD) or the
range of the temperature transmitter (if using a
thermocouple).
8)
Trapping problems
a) A steam trap that is under sized or malfunctioning
can cause the heat exchanger to flood during high
load conditions, giving rise to wide swings in process
temperature. Check for this problem by manually
bypassing the trap under full load conditions, and
observe whether there is an improvement in
temperature control.
9)
Incorrect Installation of Regulator
a) A poorly installed regulator can cause cycling. Make
sure that the regulator is installed in the proper
orientation and that the sensing line is installed to
provide proper condensate drainage, as indicated in
the regulator’s Installation and Operation Manual.
10) Poor performance or malfunction of control valve
a) A malfunctioning control valve component, such as a
leaking or broken actuator stem seal, can cause the
system to work poorly or not at all. Also, if an existing
control valve from another manufacturer has been
used in the system, check for hysteresis, ability to
throttle properly, and sizing (over or under).
10 Most Common Problems
1 ) Leaky air connections - must be tested bubble tight with
soapy water solution.
2)
Incorrect field wiring. Re-check connections in reverse
order of how they were connected.
3)
Loose connections.
4)
Incorrect calibration.
5)
Speed of response and dead band adjustment.
6)
Insufficient air pressure supply.
7)
LCD decimal selector in wrong position.
8)
Oversized or malfunctioning control valve/regulator.
9)
Poor condensate drainage from heat exchangers.
10) Wrong supply voltage.