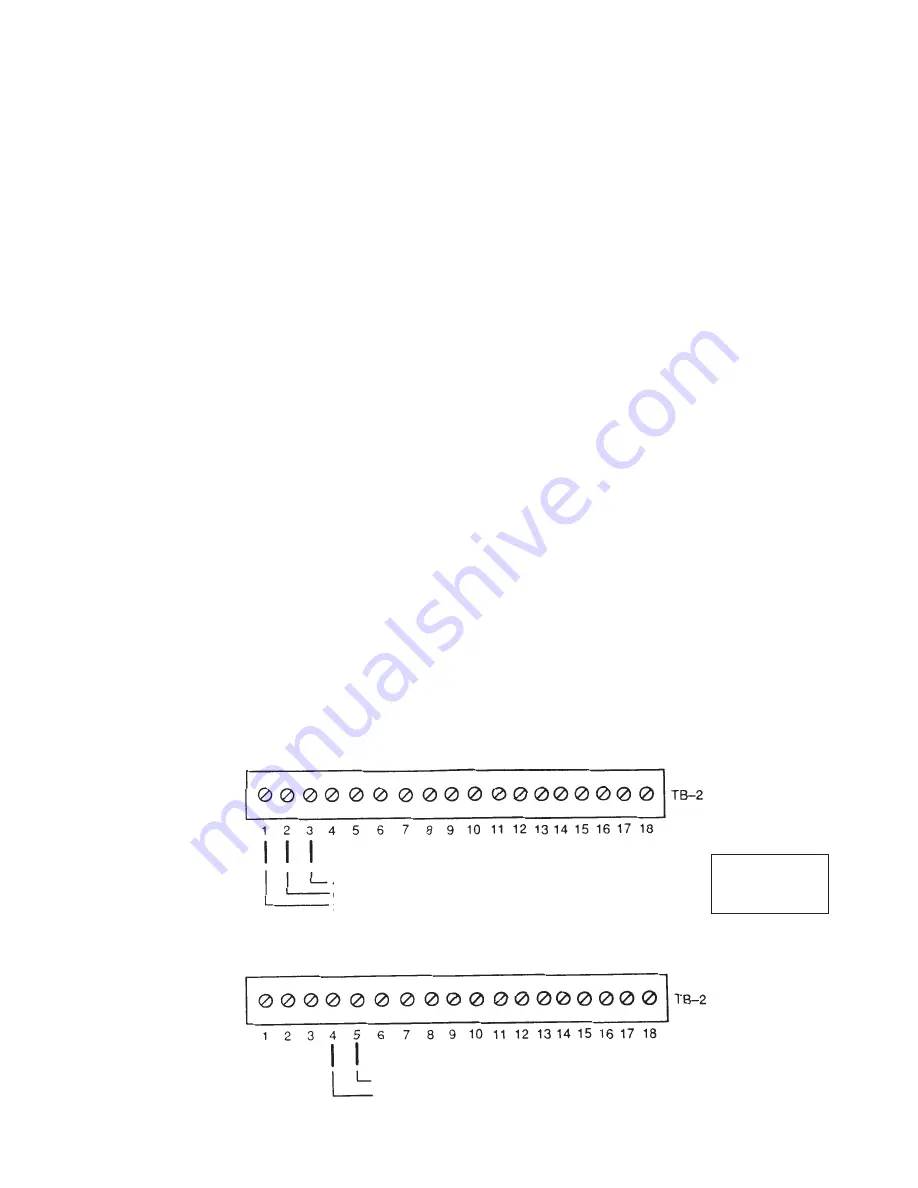
CAUTION
- All the pneumatic connections must be
tight enough to be leak proof for proper operation. Air
connections MUST be checked with a soapy water
solution and bubble tight.
W A R N I N G
- Keep stop valves closed until all
adjustments and checks in steps 2 -10 are completed.
W A R N I N G
- Turn off electrical power before
removing the internal field wiring panel.
2)
Take off field wiring panel by loosening screws.
3)
Set the direct/reverse switch (SW3) to the proper
position. (See Figure 7). When set on direct, the air
output will increase when the signal from the
transmitter increases and vice versa.
For example, if the system is being used to control
pressure downstream of a normally closed control valve,
reverse action would be required (increasing system
pressure will increase the signal from the transmitter
and this must produce a decrease of output signal air
pressure to close the control valve).
4)
Install the set point selector jumper J16-J21. This
jumper allows the PMC-1 to operate in one of two
different set point modes, local or remote.
LOC
Local set point
REM/LOC
REM/LPOS
REM/VENT
REM/LOAD
}
REM/ZERO
Installing jumper in ‘LOC” (local) position allows set
point adjustments using the up or down push buttons
located on the front panel, only when the “SP” LED is lit.
By inserting the jumper in any of the remaining five
positions, the controller accepts a (4-20mA) external set
Remote set point
with selection of
defaults.
4.
Terminals 8 through 12 have been reserved for adding
future options to the controller.
5.
Terminals 13, 14, 15 are used to connect the optional
local control module model RCS-90. This module can be
used if the PMC-1 is mounted at a remote location from a
control valve.
6.
When the PMC-1 is being used as a temperature
controller with an RTD, an optional signal conditioning
card, calibrated for a temperature range suitable for the
process, must be installed in TB 5. Jumper at J5/J6 must
be on J6. (See figure 7) For a 3 wire RTD, connect the
two RTD wires that are internally connected together
(zero resistance between them) to terminals 16 and 17
and the remaining connection to terminal 18 of TB-2.
(See Figure 5). For a 2 wire RTD, jump terminals 16 and
17. (See Figure 6). See Appendix C for guidelines on
practical distance limitations.
7.
Power and signal lines should be routed through separate
conduits to avoid interference. Set the 115/230 voltage
switch (SW1) to match the supply voltage.
DO NOT TURN
ON A.C. POWER YET
. With AC power circuit breaker
OFF, connect power leads (unpowered) to TB-1 (Figure 7).
Connect the black wire (HI) to terminal 1, the white wire
(LO) to terminal 2 and the green or green/yellow earth
ground wire to terminal 3 of TB-1. If the PMC-1 is power-
ed by 24v DC, connect the positive connection to terminal
6 and the negative connection to terminal 7 of TB-2, and
DO NOT connect any wires to TB-1. (See Figure 8).
8.
For 4-20mA output, connect recorder, alarms or other
auxiliary device to TB-7 noting the polarity. NOTE: The
4-20mA output will be within ±0.5% (of span) of the
value indicated on the PMC-1. Re-calibrate the remote
device to agree with the PMC-1, do not re-calibrate the
PMC-1.
D. Start-Up
1)
Close stop valves upstream and downstream of the
diaphragm control valve.
WIRING DIAGRAMS FOR TYPICAL INSTALLATIONS
Wiring Connections for 4—20 mA Transmitter (e.g. pressure or level)
4—20 mA transmitter return
Ground
24 VDC power output to transmitter
Wiring Connections for External Set Point
4—20 mA input
4—20 mA return
FIGURE 3
FIGURE 4
5
NOTE:
Jumper J5/J6
must be on J5