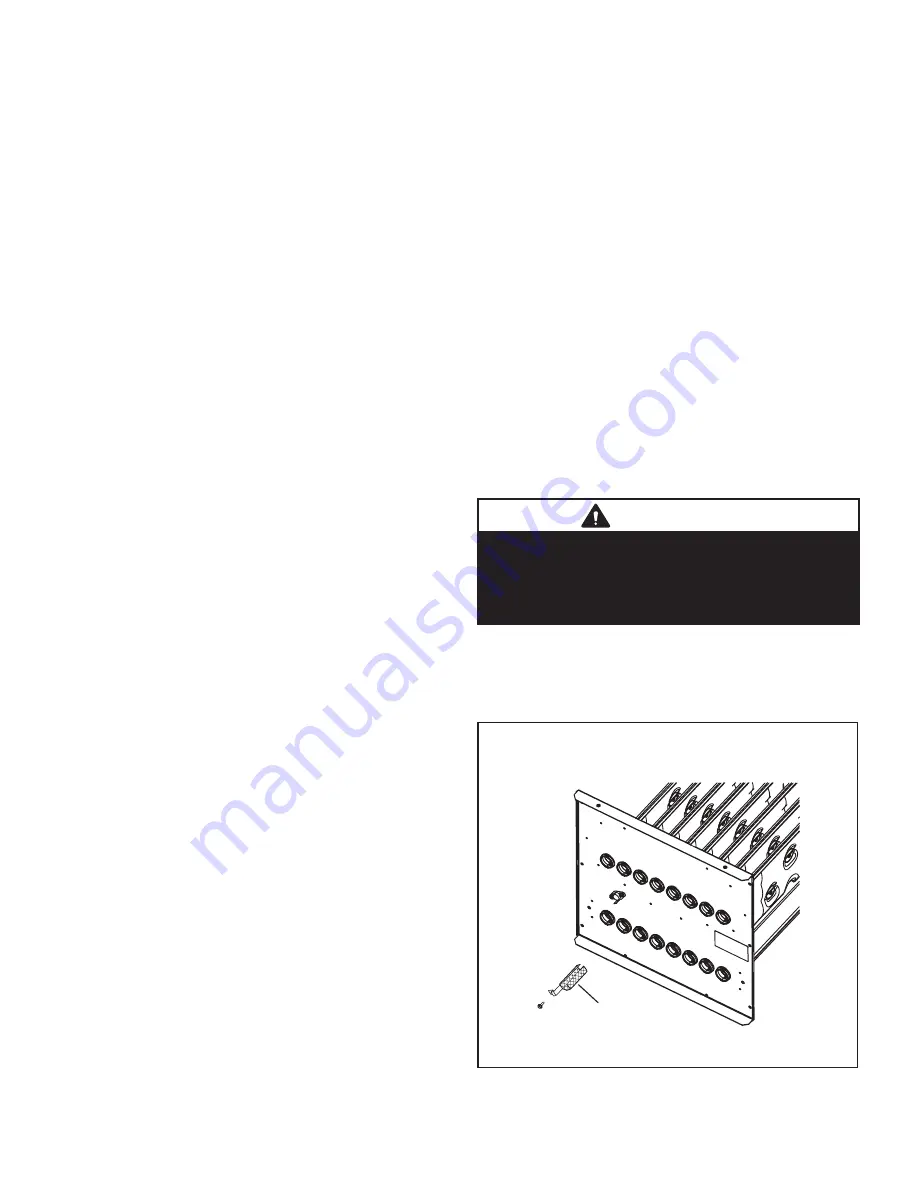
Page 53
2 - Verify that system total static pressure and airflow set
-
tings are within specific operating parameters.
3 - Clock gas meter to ensure that the unit is operating
at the specified firing rate. Check the supply pressure
and the manifold pressure. On two-stage gas furnaces
check the manifold pressure on high fire and low fire. If
manifold pressure adjustment is necessary, consult the
Service Literature for unit specific information on ad
-
justing gas pressure. Not all gas valves are adjustable.
Verify correct temperature rise.
A-Heat Exchanger and Burners
Cleaning the Heat Exchanger and Burners
NOTE -
Use papers or protective covering in front of the
furnace during cleaning.
1 - Turn off both electrical and gas power supplies to fur
-
nace.
2 - Remove flue pipe and top cap (some applications top
cap can remain) from the unit.
3 - Label the wires from gas valve, rollout switches, prima
-
ry limit switch and make-up box then disconnect them.
4 - Remove the screws that secure the combustion air in
-
ducer/ pressure switch assembly to the collector box.
Carefully remove the combustion air inducer to avoid
damaging blower gasket. If gasket is damaged, it must
be replaced to prevent leakage.
5 - Remove the collector box located behind the combus
-
tion air inducer. Be careful with the collector box gas
-
ket. If the gasket is damaged, it must be replaced to
prevent leakage.
6 - Disconnect gas supply piping. Remove the screw se
-
curing the burner box cover and remove cover. Re
-
move the four screws securing the burner manifold
assembly to the vestibule panel and remove the as
-
sembly from the unit.
7 - Remove screws securing burner box and remove burn
-
er box.
8 -
NOX units only -
Remove screw securing NOX insert.
Remove NOX insert. See FIGURE 24.
9 - Remove screws from both sides, top and bottom of
vestibule panel.
10- Remove heat exchanger. It may be necessary to
spread cabinet side to allow more room. If so, remove
five screws from the left side or right side of cabinet.
11- Back wash using steam. Begin from the burner open
-
ing on each clam. Steam must not exceed 275°F.
12- To clean burners, run a vacuum cleaner with a soft
brush attachment over the face of burners. Visually in
-
spect inside the burners and crossovers for any block
-
age caused by foreign matter. Remove any blockage.
FIGURE 25 shows burner detail.
13- To clean the combustion air inducer visually inspect
and using a wire brush clean where necessary. Use
compressed air to clean off debris and any rust.
14- Reinstall heat exchanger in vestibule. (Replace the
five screws in the cabinet from step 10 if removed).
15- NOX units only - replace NOX inserts.
16- Reinstall collector box and combustion air assembly.
Reinstall all screws to the collector box and combus
-
tion air inducer. Failure to replace all screws may
cause leaks. Inspect gaskets for any damage and re
-
place if necessary.
17- Reinstall burner box, manifold assembly and burner
box cover.
18- Reconnect all wires.
19- Reconnect top cap and vent pipe to combustion air
inducer outlet.
20- Reconnect gas supply piping.
21- Turn on power and gas supply to unit.
22- Set thermostat and check for proper operation.
23- Check all piping connections, factory and field, for gas
leaks. Use a leak detecting solution or other preferred
means.
CAUTION
Some soaps used for leak detection are corrosive
to certain metals. Carefully rinse piping thoroughly
after leak test has been completed. Do not use
matches, candles, flame or other sources of ignition
to check for gas leaks.
24- If a leak is detected, shut gas and electricity off and
repair leak.
25- Repeat steps 24 and 26 until no leaks are detected.
26- Replace access panel.
NOx INSERTS
NOx Insert
FIGURE 24