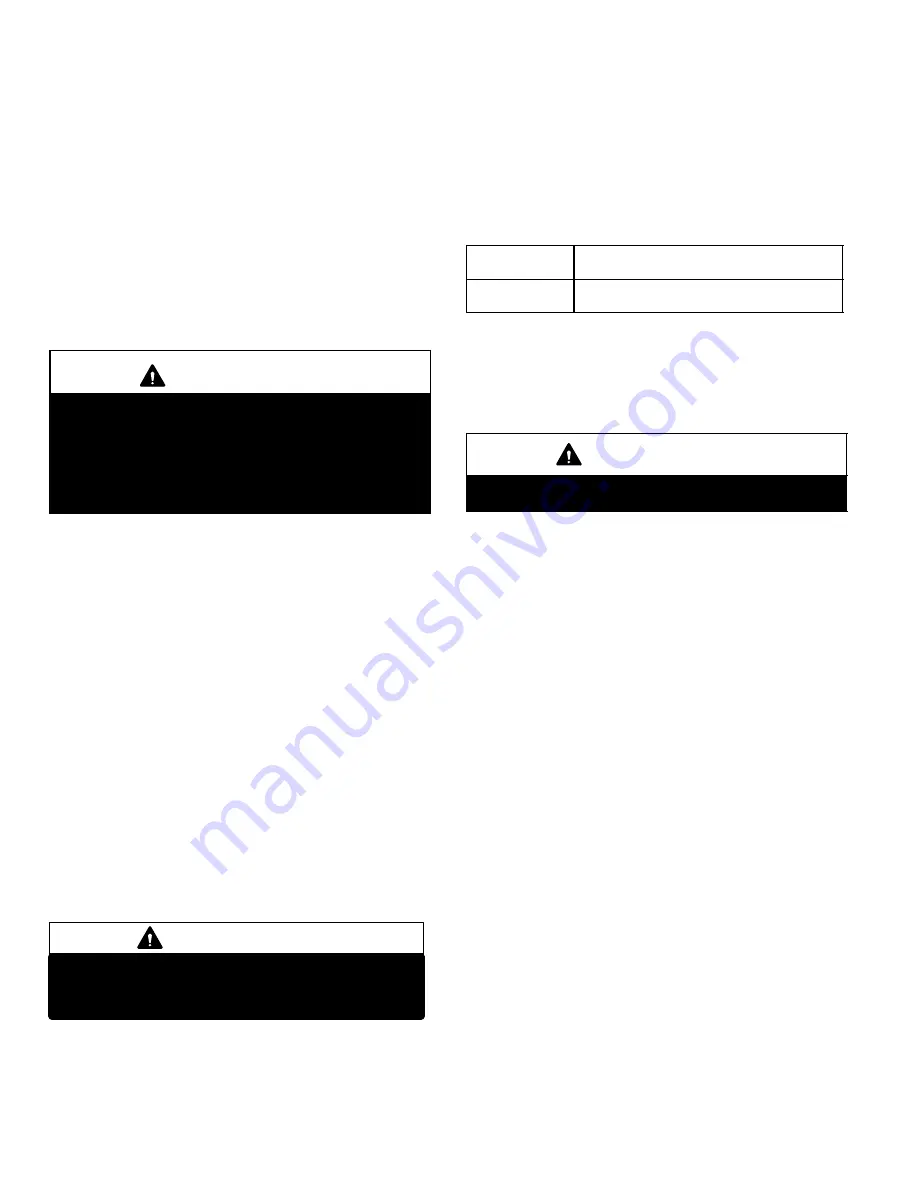
Page 16
NOTE − The term
absolute pressure
means the total
actual pressure within a given volume or system,
above the absolute zero of pressure. Absolute pres-
sure in a vacuum is equal to atmospheric pressure mi-
nus vacuum pressure.
6 − When the absolute pressure reaches 23,000 microns
(29.01 inches of mercury), close the manifold gauge
valves, turn off the vacuum pump and disconnect the
manifold gauge center port hose from vacuum pump.
Attach the manifold center port hose to a nitrogen cylin-
der with pressure regulator set to 150 psig (1034 kPa)
and purge the hose. Open the manifold gauge valves to
break the vacuum in the line set and indoor unit. Close
the manifold gauge valves.
CAUTION
Danger of Equipment Damage.
Avoid deep vacuum operation. Do not use compres-
sors to evacuate a system.
Extremely low vacuums can cause internal arcing
and compressor failure.
Damage caused by deep vacuum operation will void
warranty.
7 − Shut off the nitrogen cylinder and remove the manifold
gauge hose from the cylinder. Open the manifold
gauge valves to release the nitrogen from the line set
and indoor unit.
8 − Reconnect the manifold gauge to the vacuum pump,
turn the pump on, and continue to evacuate the line set
and indoor unit until the absolute pressure does not rise
above 500 microns (29.9 inches of mercury) within a
20−minute period after shutting off the vacuum pump
and closing the manifold gauge valves.
9 − When the absolute pressure requirement above has
been met, disconnect the manifold hose from the vacu-
um pump and connect it to an upright cylinder of R410A
refrigerant. Open the manifold gauge valves to break
the vacuum from 1 to 2 psig positive pressure in the line
set and indoor unit. Close manifold gauge valves and
shut off the R410A cylinder and remove the manifold
gauge set.
C − Charging
WARNING
Refrigerant can be harmful if inhaled. Refrigerant
must be used and recovered responsibly. Failure
to follow this warning can lead to injury or death.
Units are factory charged with the amount of R410A refrig-
erant indicated on the unit rating plate. This charge is based
on a matching indoor coil and outdoor coil with 15 ft. (4.5m)
line set. See table 4 for varying lengths of line set and
charge adjustment. The check/expansion valve provided
with the unit is approved for use with R410A. Do not replace
it with a valve designed for use with R22. This unit is NOT
approved for use with coils which include metering orifices
or capillary tubes.
TABLE 4
Liquid Line Set
Diameter
Oz. per 5 ft. (grams per 1.5 m) adjust
from 15 ft. (4.5 m) line set*
3/8 in.
(10 mm)
3 ounces per 5 feet
(85g per 1.5 m)
*If line length is greater than 15 ft. (4.5 m), add this amount.
If line length is less than 15 ft. (4.5 m), subtract this amount.
Units are designed for line sets up to 50 feet (15.2 m). Con-
sult Lennox Refrigeration Piping Manual for line sets over
50 feet (15.2 m).
IMPORTANT
Mineral oils are not compatible with R410A. If oil
must be added, it must be a polyol ester oil.
The outdoor unit should be charged during warm weather.
However, applications arise in which charging must occur
in the colder months.
The method of charging is determined
by the unit’s
refrigerant metering device
and the
outdoor
ambient temperature
.
Measure the liquid line temperature and the outdoor ambi-
ent temperature as outlined below:
1 − Connect the manifold gauge set to the service valves:
low pressure gauge to
vapor
valve service port
high pressure gauge to
liquid
valve service port
Connect the center manifold hose to an upright cylinder
of R410A. Close manifold gauge set valves.
2 − Set the room thermostat to call for heat. This will create
the necessary load for properly charging the system in
the cooling cycle.
3 − Use a digital thermometer to record the outdoor ambi-
ent temperature.
4 − When the heating demand has been satisfied, switch
the thermostat to cooling mode with a set point of 68
F
(20
C). When pressures have stabilized, use a digital
thermometer to record the liquid line temperature.
5 − The outdoor temperature will determine which charg-
ing method to use. Proceed with the appropriate charg-
ing procedure.