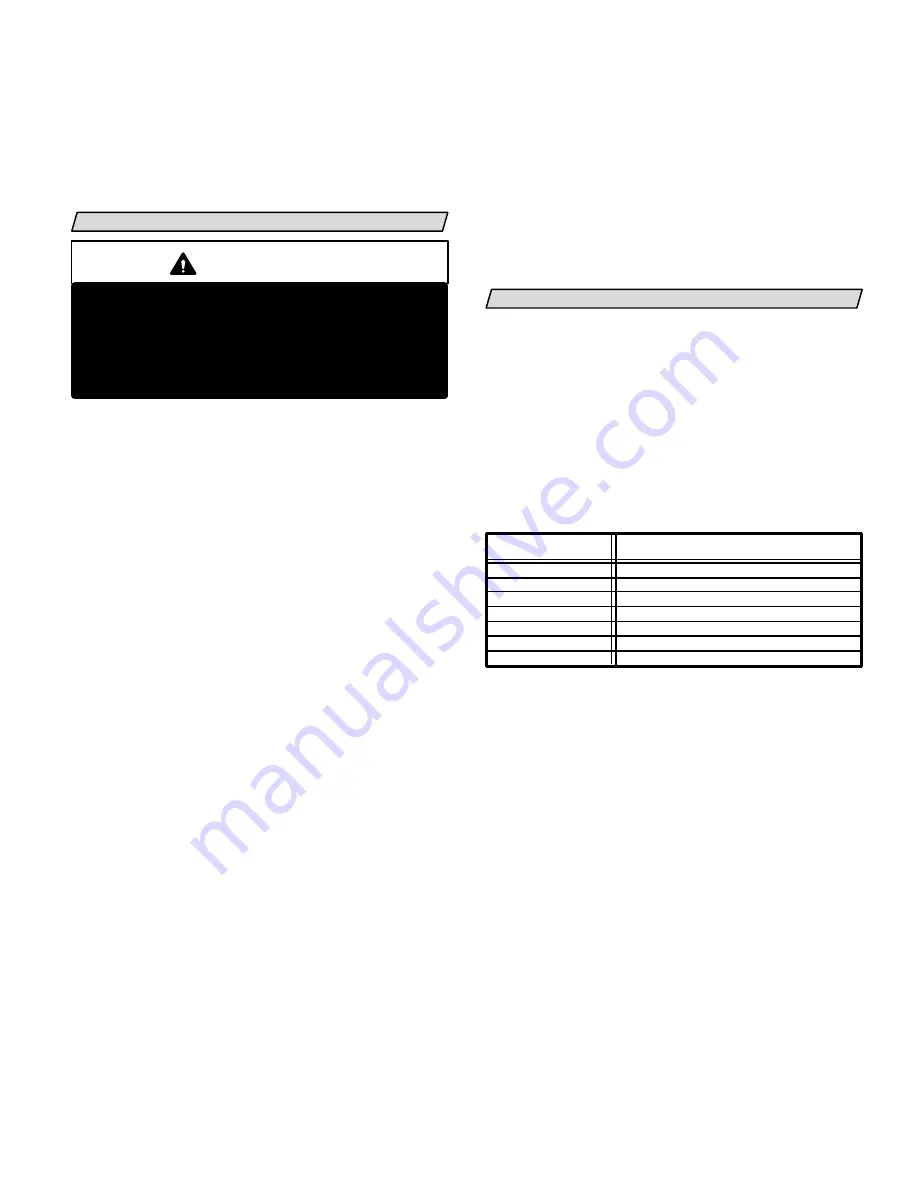
Page 7
3.57kg) 9-
When the absolute pressure require
ment above has been met, disconnect the manifold
hose from the vacuum pump and connect it to an
upright bottle of R22 refrigerant. Open the manifold
gauge valves to break the vacuum in the line set and
indoor unit. Close manifold gauge valves and shut
off R22 bottle and remove manifold gauge set.
START-UP
IMPORTANT
HP25-413/463-1Y three-phase units only-Crank
case heater must be energized 24 hours before at
tempting to start compressor. Compressor dam
age may occur from slugging. To prevent com
pressor operation, set thermostat demand so
there is no demand. Apply power to unit.
Cooling Start-up
1- Rotate fan to check for frozen bearings or binding.
2- Inspect all factory and field-installed wiring for
loose connections.
3- Open liquid line and vapor line service valves to re
lease refrigerant charge (contained in heat pump
unit) into the system.
4- Replace stem caps and secure finger tight plus an
additional 1/6th turn.
5- Check voltage supply at the disconnect switch.
The voltage must be within the range listed on the
unit nameplate. If not, do not start the equipment
until the power company has been consulted and
the voltage condition corrected.
6- Set the thermostat for a cooling demand, turn on
power to the indoor blower coil and close heat
pump unit disconnect switch to start the unit.
7- Recheck unit voltage with unit running. Power
must be within range shown on unit nameplate.
Check amperage draw of unit. Refer to unit name
plate for correct running amps.
Three-Phase Compressor Rotation
Three-phase scroll compressors must be phased se
quentially to ensure correct compressor rotation and
operation. At compressor start-up, a rise in discharge
and drop in suction pressures indicate proper com
pressor phasing and operation. If discharge and suc
tions pressures do not perform normally, follow the
steps below to correctly phase in the unit.
1- Disconnect power to the unit.
2- Reverse any two field power leads to the unit.
3- Reapply power to the unit.
Discharge and suction pressures should operate at
their normal start-up ranges.
NOTE-Compressor noise level will be significantly
higher when phasing is incorrect and the unit will not
provide cooling when compressor is operating back
wards. Continued backward operation will cause the
compressor to cycle on internal protector.
CHARGING
It is desirable to charge the system in the cooling cycle
if weather conditions permit. However, if the unit must
be charged in the heating season, one of the following
procedures must be followed to ensure proper system
charge.
If the system is completely void of refrigerant, the rec
ommended and most accurate method of charging is
to weigh the refrigerant into the unit according to the
total amount shown on the unit nameplate and in table
3. Refer to the Lennox Unit Information Service manual
for proper procedure.
TABLE 3
Model
Refrigerant Charge R-22
HP25-211
HP25-311
HP25-410
HP25-460
7 lbs. 10 oz. (3.46 kg)
10 lbs. 4 oz. (4.65 kg)
11 lbs.4 oz. (5.10 kg)
12 lbs. 8 oz. (5.67 kg)
HP25-261
8 lbs. 14 oz. (4.03 kg)
HP25-510
18 lbs. 8 oz. (8.39 kg)
HP25-650
23 lbs. 14 oz. (10.83 kg)
If weighing facilities are not available or if unit is just
low on charge, use the following procedure:
1- Connect gauge manifold as shown in figure 7.
Connect an upright R-22 (HCFC-22) drum to center
port of gauge manifold.
2- Record outdoor ambient temperature.
3- Set room thermostat to 74
F (23
C) in Emergen
cy Heat" or Heat" position and allow unit to run
until heating demand is satisfied. This will create
the necessary load for proper charging of system
in cooling cycle. Change thermostat setting to
68
F (20
C) in Cool" position. Allow unit to run
until system pressures stabilize.
4- Check to make sure that thermometer well is filled
with mineral oil before checking liquid line tem
perature.