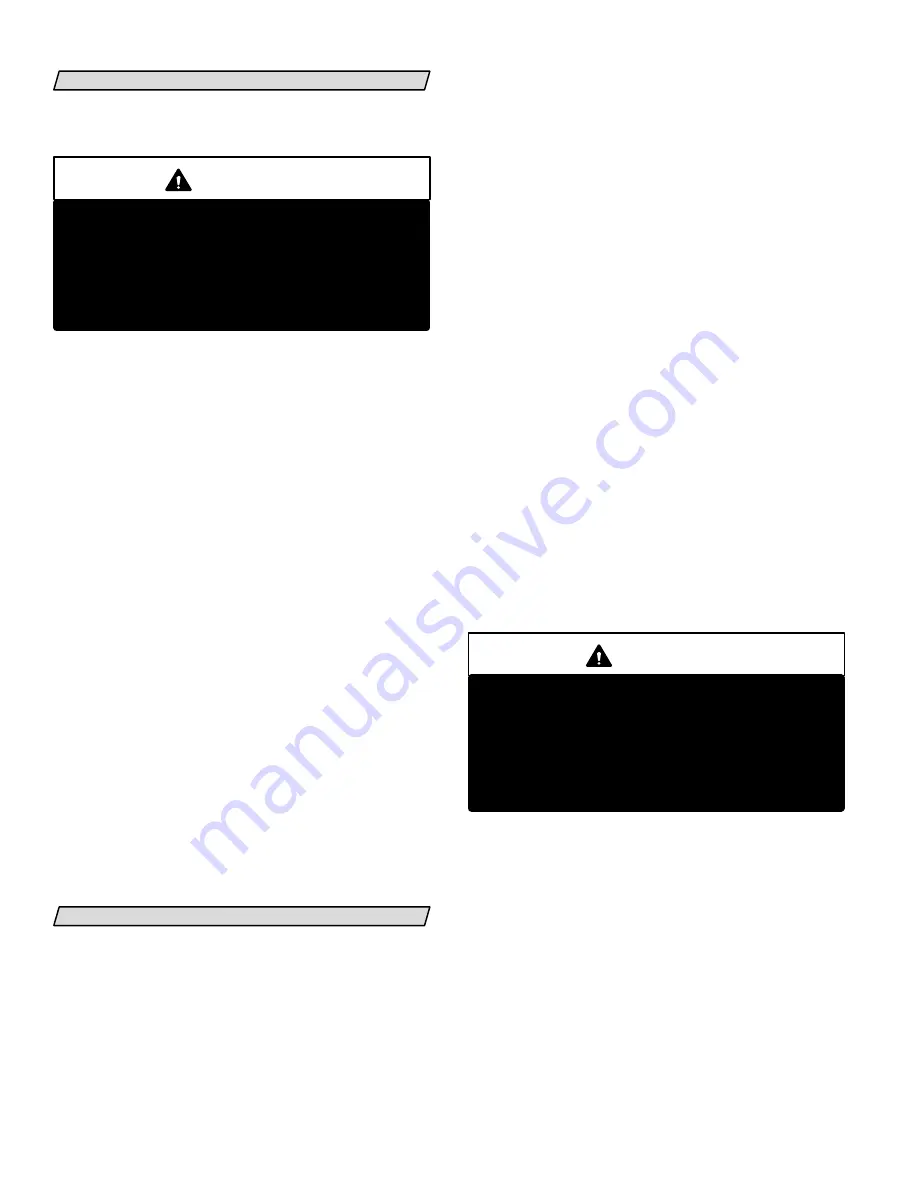
Page 6
LEAK TESTING
After the line set has been connected to the indoor and
outdoor units, the line set connections and indoor unit
must be checked for leaks.
WARNING
Never use oxygen to pressurize refrigeration or air
conditioning system. Oxygen will explode on con
tact with oil and could cause personal injury. When
using high pressure gas such as nitrogen or CO
2
for
this purpose, be sure to use a regulator that can
control the pressure down to 1 or 2 psig (6.9 to 13.8
kPa).
Using an Electronic Leak Detector or Halide
1- Connect a cylinder of nitrogen with a pressure reg
ulating valve to the center port of the manifold
gauge set.
2- Connect the high pressure hose of the manifold
gauge set to the service port of the vapor valve.
(Normally, the high pressure hose is connected to
the liquid line port, however, connecting it to the
vapor port better protects the manifold gauge set
from high pressure damage.)
3- With both manifold valves closed, open the valve
on the R22 bottle (vapor only).
4- Open the high pressure side of the manifold to al
low R22 into the line set and indoor unit. Weigh in a
trace amount of R22.
[A trace amount is a maxi
mum of 2 ounces (57g) refrigerant or 3 pounds (31
kPa) pressure].
Close the valve on the R22 bottle
and the valve on the high pressure side of the man
ifold gauge set. Disconnect R22 bottle.
5- Adjust nitrogen pressure to 150 psig (1034 kPa). Open
the valve on the high side of the manifold gauge set
which will pressurize line set and indoor unit.
6- After a short period of time, open a refrigerant port
to make sure the refrigerant added is adequate to
be detected. (Amounts of refrigerant will vary with
line lengths.) Check all joints for leaks. Purge nitro
gen and R22 mixture. Correct any leaks and re
check.
EVACUATING
Evacuating the system of non-condensables is critical
for proper operation of the unit. Non-condensables are
defined as any gas that will not condense under temper
atures and pressures present during operation of an air
conditioning system. Non-condensables and water va
por combine with refrigerant to produce substances
that corrode copper piping and compressor parts.
1- Connect manifold gauge set to the service valve ports
as follows: low pressure gauge to vapor line service
valve; high pressure gauge to liquid line service valve.
2- Connect the vacuum pump (with vacuum gauge)
to the center port of the manifold gauge set.
3- Open both manifold valves and start vacuum
pump.
4- Evacuate the line set and indoor unit to an
absolute
pressure
of 23mm of mercury or approximately 1
inch of mercury. During the early stages of evacua
tion, it is desirable to close the manifold gauge
valve at least once to determine if there is a rapid
rise in
absolute pressure
. A rapid rise in pressure
indicates a relatively large leak. If this occurs, the
leak testing procedure must be repeated.
NOTE - The term
absolute pressure
means the to
tal actual pressure within a given volume or sys
tem, above the absolute zero of pressure. Absolute
pressure in a vacuum is equal to atmospheric pres
sure minus vacuum pressure.
5- When the absolute pressure reaches 23mm of mer
cury, close the manifold gauge valves, turn off the
vacuum pump and disconnect the manifold gauge
center port hose from vacuum pump. Attach the
manifold center port hose to a nitrogen cylinder
with pressure regulator set to 150 psig (1034 kPa)
and purge the hose. Open the manifold gauge
valves to break the vacuum in the line set and in
door unit. Close the manifold gauge valves.
CAUTION
Danger of Equipment Damage.
Avoid deep vacuum operation. Do not use com
pressors to evacuate a system.
Extremely low vacuums can cause internal arcing
and compressor failure.
Damage caused by deep vacuum operation will
void warranty.
6- Shut off the nitrogen cylinder and remove the man
ifold gauge hose from the cylinder. Open the man
ifold gauge valves to release the nitrogen from the
line set and indoor unit.
7- Reconnect the manifold gauge to the vacuum
pump, turn the pump on and continue to evacuate
the line set and indoor unit until the absolute pres
sure does not rise above .5mm of mercury within a
20 minute period after shutting off the vacuum
pump and closing the manifold gauge valves.
8- Depending on the equipment used to determine
the vacuum level, absolute pressure of .5mm of
mercury is equal to 500 microns.