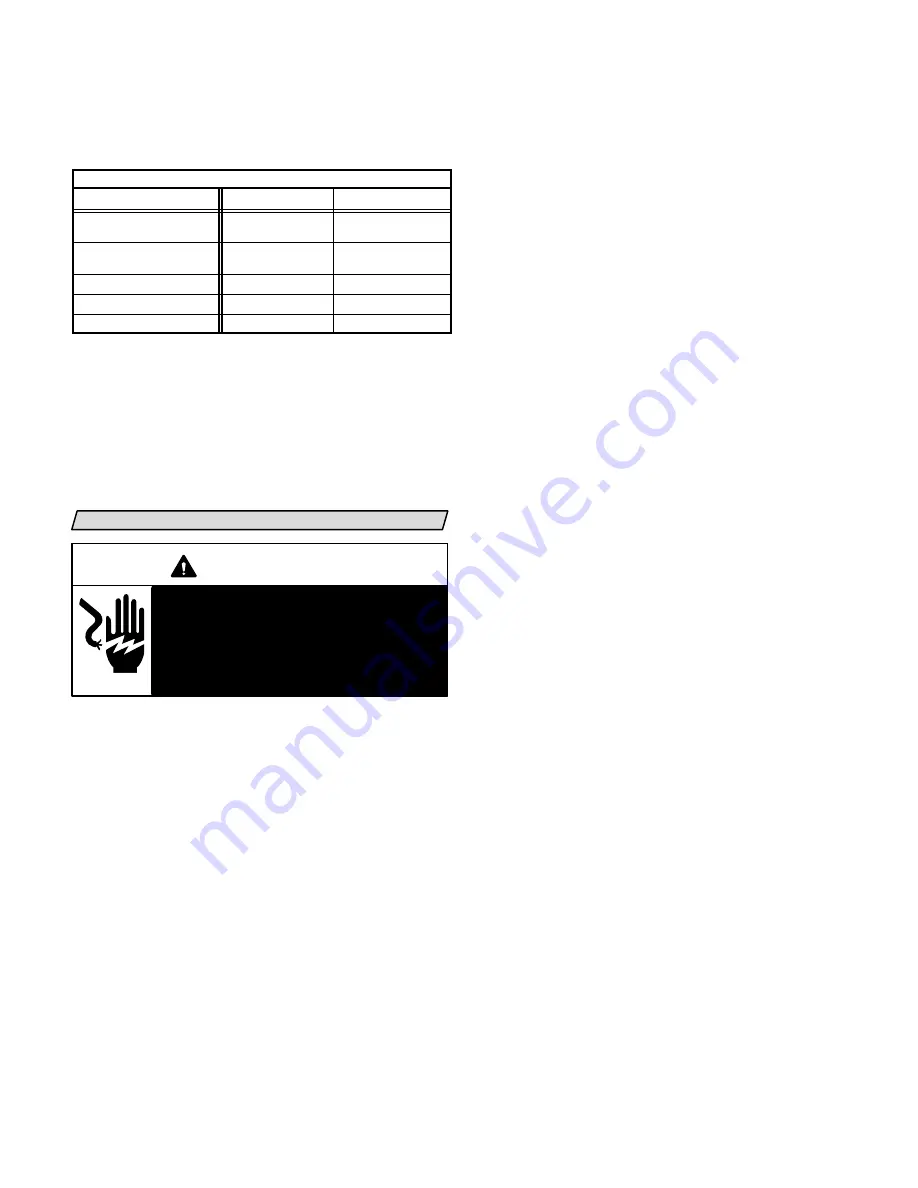
Page 11
Diagnostic LEDs
The defrost board uses two LEDs for diagnostics. The
LEDs flash a specific sequence according to the
condition.
TABLE 7
DEFROST CONTROL BOARD DIAGNOSTIC LED
MODE
LED 1
LED 2
Normal Operation/
Power to board
Flash together
with LED 2
Flash together with
LED 1
Time Delay
To Protect Compressor
Alternating Flashes
with LED 2
Alternating Flashes
with LED 1
Pressure Switch Open
Off
On
Pressure Switch Lockout On
Off
Board Malfunction
On
On
Ambient Thermistor & Service Light Connection
The defrost control board provides terminal connec
tions for the ambient thermistor and service light.
These features provide a service light thermostat
which activates the room thermostat service light dur
ing periods of inefficient operation. The thermistor
compensates for changes in ambient temperature
which might cause thermostat droop.
MAINTENANCE
WARNING
Electric shock hazard. Can cause injury
or death. Before attempting to per
form any service or maintenance, turn
the electrical power to unit OFF at dis
connect switch(es). Unit may have
multiple power supplies.
At the beginning of each heating or cooling season, the
system should be cleaned as follows:
Heat Pump Unit
1- Clean and inspect outdoor coil. (Coil may be
flushed with a water hose.)
2- Outdoor coil fan motor is prelubricated and
sealed. No further lubrication is needed.
3- Visually inspect all connecting lines, joints and
coils for evidence of oil leaks.
4- Check all wiring for loose connections.
5- Check for correct voltage at unit (unit operating).
6- Check amp-draw on heat pump fan motor.
Unit nameplate_______Actual_______.
7- Inspect drain holes in coil compartment base and
clean if necessary.
NOTE-If insufficient heating or cooling occurs, the unit
should be gauged and refrigerant charge checked.
Indoor Coil
1- Clean coil if necessary.
2- Check connecting lines, joints and coil for evi
dence of oil leaks.
3- Check condensate line and clean if necessary.
Indoor Unit
1- Clean or change filters.
2- Adjust blower speed for cooling. The pressure drop
over the coil should be checked to determine the cor
rect blower air volume. Refer to the Lennox Engi
neering Handbook for indoor unit blower perfor
mance tables.
3- Check all wiring for loose connections.
4- Check for correct voltage at unit.
5- Check amp-draw on blower motor.
Motor nameplate_______Actual_______.