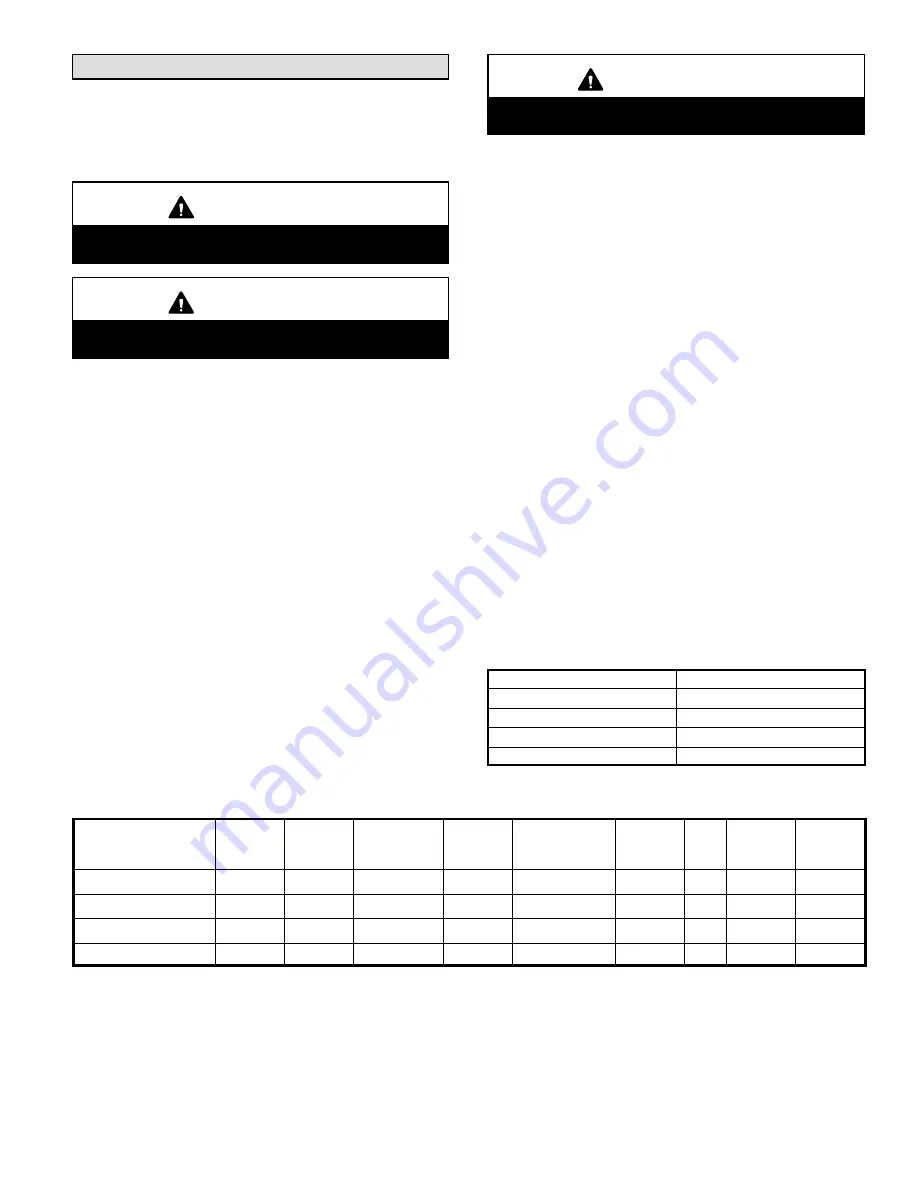
Page 15
Unit Start-Up & Adjustments
Before starting unit, make sure the oil tank is adequately
filled with clean No. 1 or No. 2 furnace oil.
NOTE - Water, rust or other contaminants in oil supply sys
tem will cause malfunction and failure of the internal parts
of the fuel pump.
CAUTION
Never burn garbage or paper in the heating system.
Never leave papers near or around the unit.
CAUTION
Blower access door must be in place before start-
up.
Burner Start-Up
1 - Set thermostat for heating demand and turn on elec
trical supply to unit.
2 - Open all shut-off valves in the oil supply line to the
burner.
3 - While the ignition is on, press and release the reset
button on the burner control (hold 1/2 second or less).
4 - Bleed the pump until all froth and bubbles are purged.
The bleed port is located on the bottom of the fuel
pump. To bleed, attach a clear plastic hose over the
vent plug. Loosen the plug and catch the oil in an
empty container. Tighten the plug when all the air has
been purged.
NOTE - A two-line fuel system will normally bleed itself
by forcing air back to the tank through the return line.
This type of bleeding procedure is not necessary.
5 - If burner fails to start within the set time, the burner
control will lock out operation. Press the reset button
to reset the control as in step 3. See figure 2 for burner
parts arrangement.
CAUTION
Do not push the reset button on the primary control
more than one time.
6 - If 2 pipe system fails to prime after pressing the reset
button one time, use the manual bleed port to prime
the pump.
Fuel Pump Pressure Adjustment
Measure fuel pump pressure with unit off. Attach pressure
gauge to pump outlet. Turn unit on and check pressure and
compare to table 9. Adjust if necessary.
Temperature Rise Adjustment
To measure temperature rise, place plenum thermome
ters in warm air and return air plenums. Locate thermome
ter in warm air plenum where thermometer will not “see”
the heat exchanger to prevent it from picking up radiant
heat. Set thermostat to its highest setting to start unit. After
plenum thermometers have reached their highest and
steadiest readings, subtract the readings. The difference
in temperatures in the supply and return air plenums
should approximate the temperatures listed in table 8 and
on the appliance rating plate.
If the temperature rise is not within the range listed, check
the following items:
D
Make sure that properly sized nozzle has been
used (table 9).
D
Make sure that fuel pump pressure is correct.
D
If furnace is in cutback mode, check for:
Dirty filters,
Dirty indoor coil,
Restricted ducts, closed registers, etc.
Table 8
Temperature Rise
Unit
Temperature Rise °F
ELO183DH101
65 - 75
ELO183DH114
70 - 80
ELO183DH135
65 - 75
ELO183DH150
70 - 80
Table 9
Burner Specifications
Unit
Burner
Number
Beckett
Spec. No.
Beckett
Air Tube Part
No.
Input
Rating
BTU/HR
Nozzle Size,
Spray, Angle, &
Pattern
Pump
Pressure
Head
Insertion
Length
Static
Plate
Diameter
ELO183DH101/114
100591-05
ARM2008
AF46XNHS
105,000
0.65gph X 80° B
140
F3
5
2.75
ELO183DH101/114
100591-05
ARM2008
AF46XNHS
120,000
*0.75gph X 80° B
140
F3
5
2.75
ELO183DH135/150
100591-06
ARM2009
AF46WPHS
140,000
0.85gph X 80° B
140
F4
5
3.38
ELO183DH135/150
100591-06
ARM2009
AF46WPHS
150,000
*1.00gph X 80° B
140
F4
5
3.38
*Nozzle must be field-installed for conversion to higher heating input.
NOTE - All nozzles are Delavan brand