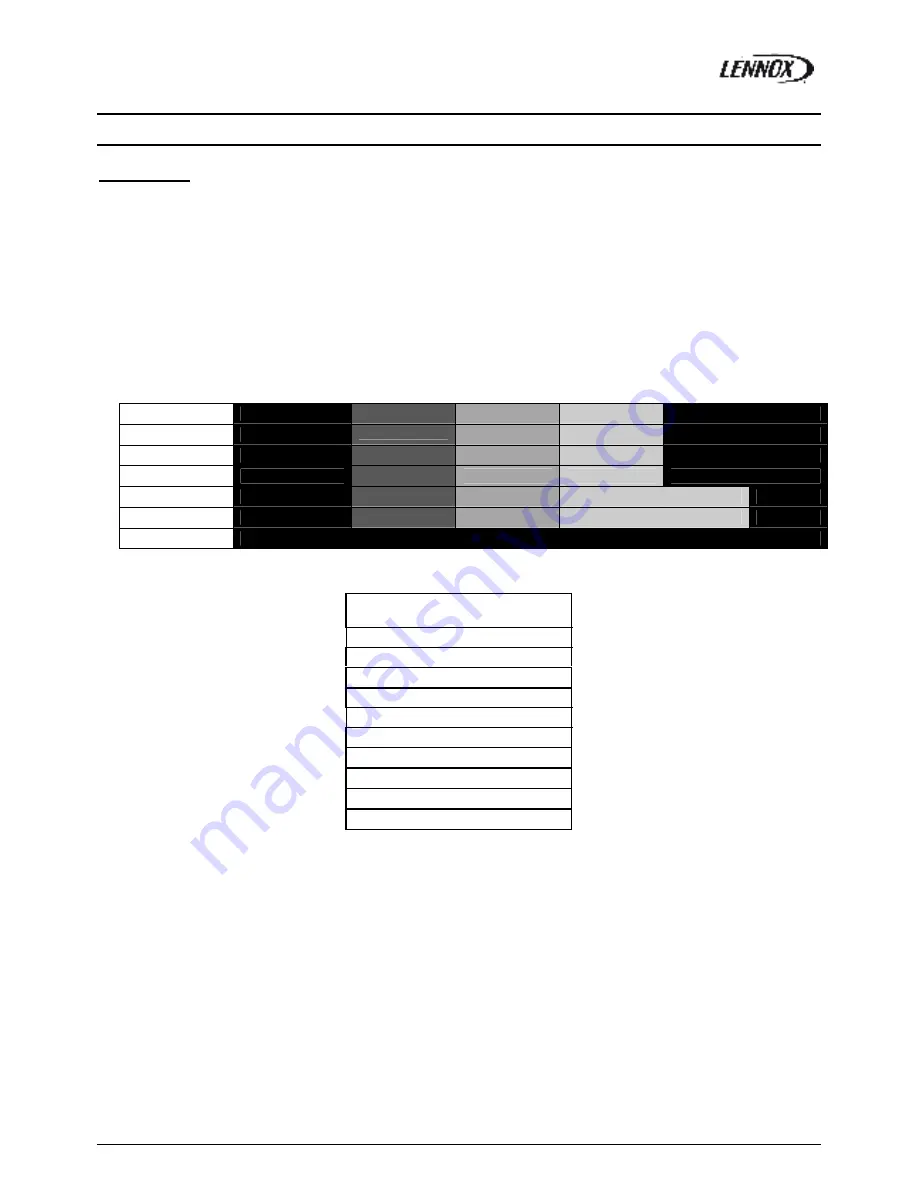
CLIMATIC 50 – ROOFTOP – VERSION 23
BALTIC R410A-IOM-0708-E
Page 100
SCHEDULING
–
CLOCK SETTING
Scheduling
Function
Controlling operation of the unit according to the time and day
Description
CLIMATICTM 50 can handle 4 time zones over the 7 days of the week:
Zone unoccupied
(Night)
Zone A
(Day A)
Zone B
(Day B)
Zone C
(Day C)
Each set point integrates the hour and minute’s adjustment, thus a value of 8.3 equal 8.30 a.m.
8h00
12h00
13h50
20h30
22h00
Monday
Unoccupied
Z :A
Z :B
Z :C
Unoccupied
Tuesday
Wednesday
Thursday
Friday
Saturday
Sunday
For each time zone, the set following set points following can be modified:
LIST SET POINT BY ZONE
Ambient temperature
Set point average
Set point dynamic
Minimum fresh air (%)
Programming
Beginning of zone; each day
Start Uno
Start z.A
Start z.B
Start z.C
Note
: “Monday” is considered as the first day of the week for programming the CLIMATIC™50.
Factory settings:
“Day A” activated from Monday to Saturday 6h
22h
Night mode (unoccupied) for the remaining of time, Sunday included
Summary of Contents for BAC020SNM
Page 11: ...COMMISSIONING REPORT BALTIC R410A IOM 0708 E Page 10 ...
Page 66: ...VENTILATION AIRFLOW BALANCING BALTIC R410A IOM 0708 E Page 65 ROOF TOP AT15 11S ...
Page 67: ...VENTILATION AIRFLOW BALANCING BALTIC R410A IOM 0708 E Page 66 ROOF TOP AT15 15S ...
Page 69: ...VENTILATION AIRFLOW BALANCING BALTIC R410A IOM 0708 E Page 68 AT10 10S EXHAUST ROOF CURB ...
Page 70: ...VENTILATION AIRFLOW BALANCING BALTIC R410A IOM 0708 E Page 69 EXHAUST ROOF CURB AT10 8G2L ...
Page 71: ...VENTILATION AIRFLOW BALANCING BALTIC R410A IOM 0708 E Page 70 EXHAUST ROOF CURB AT10 10G2L ...
Page 126: ...CERTIFICATES BALTIC R410A IOM 0708 E Page 125 ...
Page 127: ...CERTIFICATES BALTIC R410A IOM 0708 E Page 126 ...
Page 128: ...CERTIFICATES BALTIC R410A IOM 0708 E Page 127 ...
Page 129: ...CERTIFICATES BALTIC R410A IOM 0708 E Page 128 ...
Page 130: ...CERTIFICATES G4 FILTERS BALTIC R410A IOM 0708 E Page 129 ...
Page 131: ...CERTIFICATES F7 FILTERS BALTIC R410A IOM 0708 E Page 130 ...
Page 132: ...CERTIFICATES CLIMAVER 202 BALTIC R410A IOM 0708 E Page 131 ...
Page 133: ...CERTIFICATES CLIMAVER 274 BALTIC R410A IOM 0708 E Page 132 ...
Page 134: ...CERTIFICATES BALTIC R410A IOM 0708 E Page 133 ...
Page 135: ...CERTIFICATES BALTIC R410A IOM 0708 E Page 134 ...
Page 136: ...CERTIFICATES BALTIC R410A IOM 0708 E Page 135 ...