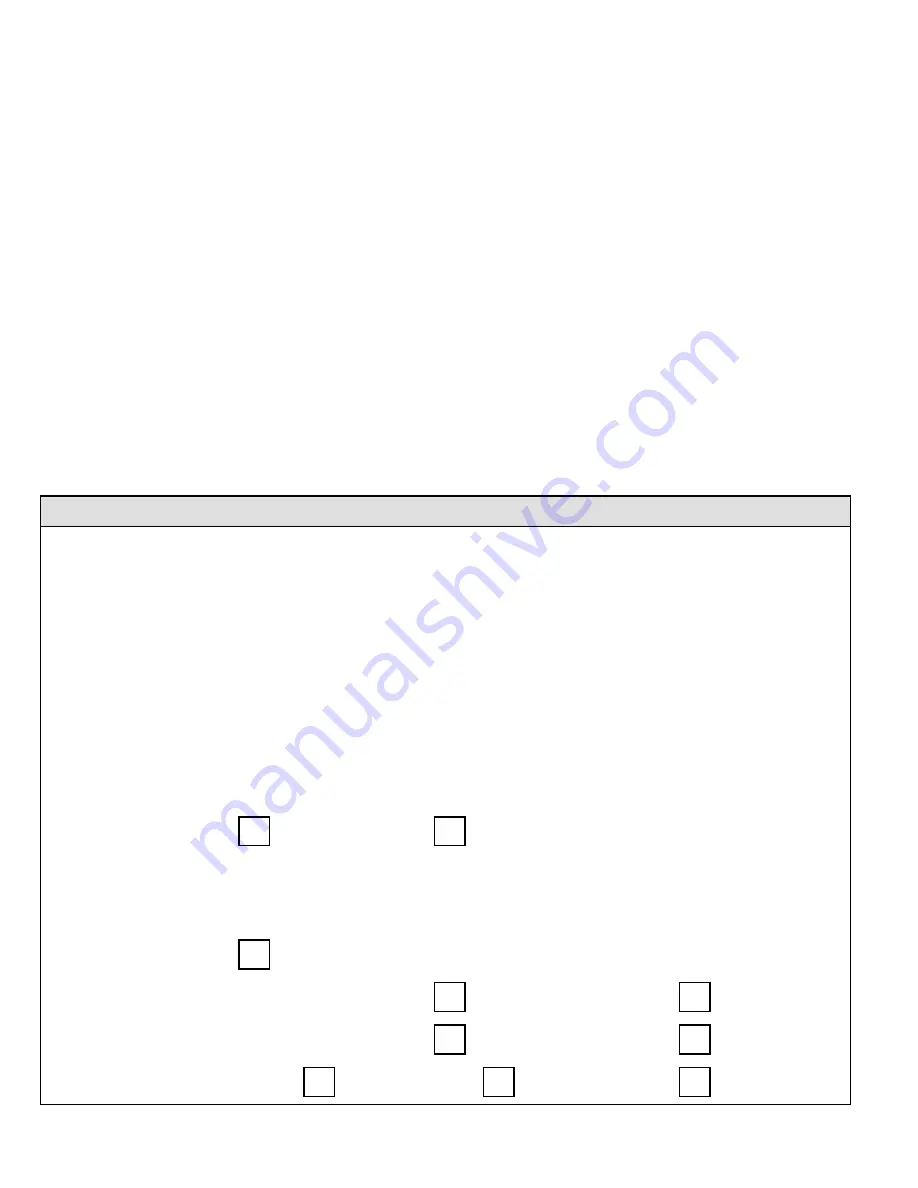
506694-01
Issue 1720
Page 16 of 16
6. Inspect drain holes in coil compartment base and
clean if necessary.
NOTE:
If insufficient cooling occurs, the unit should be
gauged and refrigerant charge should be checked.
Outdoor Coil
Clean and inspect outdoor coil (may be flushed with a
water hose). Ensure power is off before cleaning.
NOTE:
It may be necessary to flush the outdoor coil
more frequently if it is exposed to substances which are
corrosive or which block airflow across the coil (e.g., pet
urine, cottonwood seeds, fertilizers, fluids that may contain
high levels of corrosive chemicals such as salts)
Sea Coast
— Moist air in ocean locations can carry salt,
which is corrosive to most metal. Units that are located near
the ocean require frequent inspections and maintenance.
These inspections will determine the necessary need
to wash the unit including the outdoor coil. Consult your
installing contractor for proper intervals/procedures for
your geographic area or service contract.
Indoor Unit
1.
Clean or change filters.
2. Some blower motors are pre-lubricated and
permanently sealed. No more lubrication is needed.
3. Adjust blower speed for cooling. Measure the pressure
drop over the coil to determine the correct blower
CFM. Refer to the unit information service manual for
pressure drop tables and procedure.
4. Belt Drive Blowers - Check belt for wear and proper
tension.
5. Check all wiring for loose connections.
6. Check for correct voltage at unit. (blower operating)
7. Check amp draw on blower motor.
Motor Nameplate:_________ Actual:__________.
Indoor Coil
1. Clean coil if necessary.
2. Check connecting lines, joints and coil for evidence of
oil leaks.
3. Check condensate line and clean if necessary.
Start-Up and Performance Checklist
Job Name: ______________________________________________
Job No. _________________ Date: ________________
Job Location: ____________________________________________
City: ____________________ State: ________________
Installer: ________________________________________________
City: ____________________ State: ________________
Unit Model No. ___________________________________________
Serial No. _______________________________________
Service Technician: _______________________________________
Nameplate Voltage: _______________________________
Rated Load Ampacity: _______________
Compressor Amperage: _________________ Outdoor Fan: _____________________
Maximum Fuse or Circuit Breaker: ____________________________
Electrical Connections Tight?
Indoor Filter Clean?
Supply Voltage (Unit Off): __________________________
Indoor Blower RPM: ______________________________________
S.P. Drop Over Indoor (Dry): ________________________
Outdoor Coil Entering Air Temperature: _______________________
Voltage with Compressor Operating:
___________________
Outdoor Fan Checked?
Refrigerant Lines:
Leak Checked?
Properly Insulated?
Service Valves:
Fully Opened?
Caps Tight?
Thermostat
Calibrated?
Properly Set?
Level?