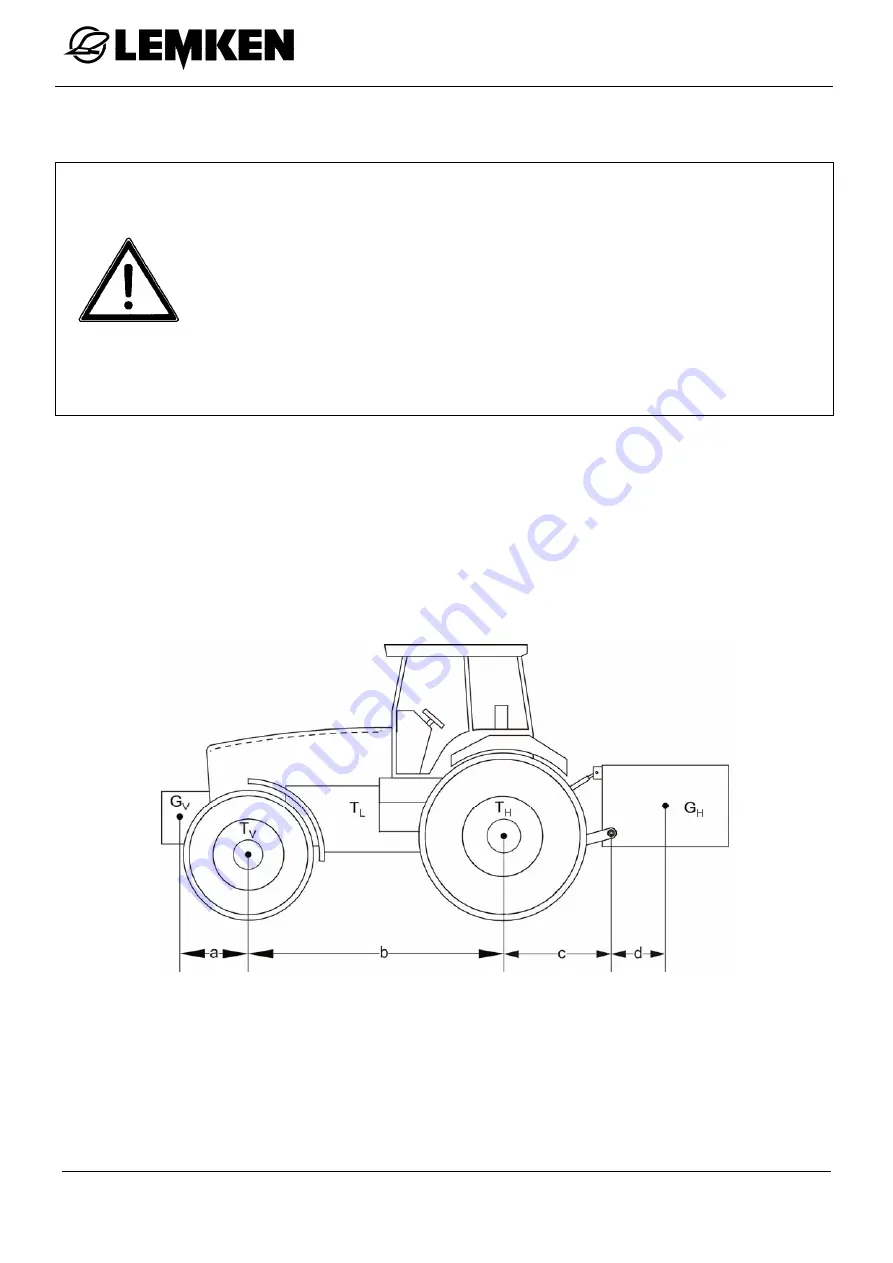
Safety measures and precautions
26
3.9.3 Axle
loads
Implements mounted to the front and rear three-point linkage must
not result in the following being exceeded:
permissible gross weight of tractor,
permissible axle loads of tractor,
the tractor's tyre load-carrying capacities.
The tractor's front axle must always be loaded with at least 20 %
of the tractor's curb weight.
The following data are required for the calculation:
from the tractor operating instructions,
from the implement operating instructions,
which are to be documented through remeasuring.