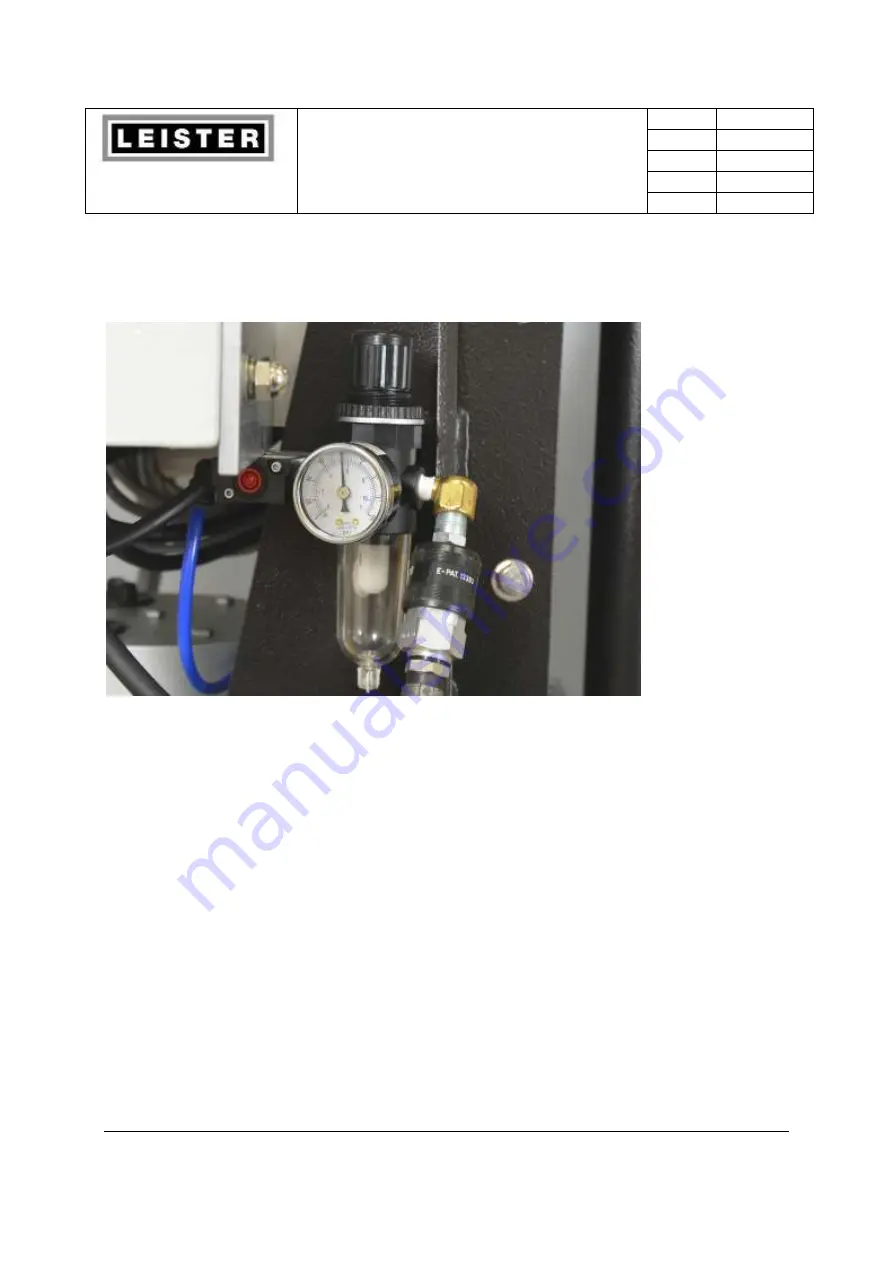
Leister Technologies AG
Operating Manual
Welding Machine SEAMTEK 36
Revision: A
QM
Page
21 / 62
Created
04.04.2014 TEX
Released
Modified
21
4)
Now you are ready to turn on the SEAMTEK 36. See section 5.0 on energizing (turning on)
the SEAMTEK 36 for the first time.
Figure 10 Shop air regulator disconnect plug
4.0 Controls: Switches, Foot Pedals and Touch Screen
This section introduces you to the various switches, foot pedals, touch screen that you use to
control the weld setup and welding process. The following is an overview of these switches,
foot pedals, touch screen and their layout. Many of the functions provided by these controls
are discussed in greater detail in other sections of this manual.
4.1 Description of Control Module Touch Screen &
Switches
This section describes the various controls located at the control module. The control module is
attached to the upper beam where it is directly overhead and in front of the operator. As
discussed in Modular and
Adjustable Features, the control module houses the SEAMTEK 36’s
touch screen operator interface and is where most of the user control features are found. Here
is a picture showing the main control screen.