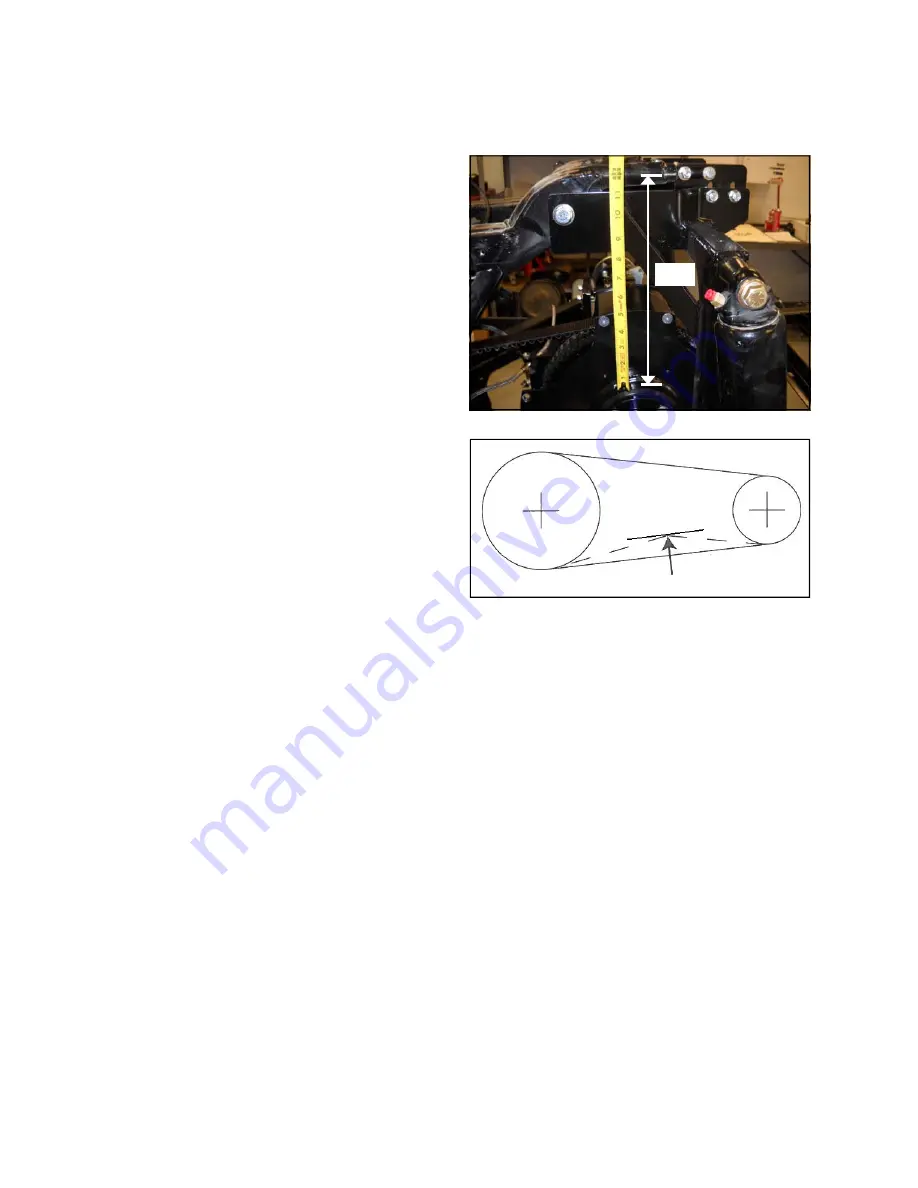
1997-2001 FLH Renegade– Rev. 3
Belt Tensioning and Tracking
1. Center differential to motorcycle frame–
this is
critical for proper belt tensioning
. Make sure
distance is within 1/16” from side to side.
2.
See Fig. 1
. Level swingarm to motorcycle frame.
This will help achieve proper ride height. With
standard shocks
, measure 12” from inner boss
against center section to center of upper motor-
cycle frame.
3.
See Fig. 2
. Using adjusters, push differential
assembly back until belt has about 3/8” slack
with
10 lbs
. pressure at midpoint of bottom run.
Measure between adapter plates and pinch
blocks to ensure that distances are equal.
4. Rotate pulleys forward for at least 3 revolutions
of rear pulley by pulling backwards on bottom
run of belt. Pull belt straight back to get an accu-
rate reading. Check that belt is running about
0.030”
from flange on rear pulley. Tap differen-
tial left or right to achieve this reading. Belt may
ride next to flange as long as it’s not trying to
climb.
5. Tighten socket head screws (8) that hold adapter
plates to swingarm and torque to
35 ft. lbs
.
6. Once tracking is obtained, re-check belt tension. Raise and lower differential assembly slowly with a
jack while checking belt tension. When tightest position is located, apply 10 lbs. force at midpoint of
lower strand of belt.
Correct deflection is 5/16” - 3/8”.
7. Increase or reduce belt deflection by turning adjuster screw on each side in or out an equal number
of turns.
8. Look along top of belt to check belt alignment on front pulley. There should be about 0.030” clear-
ance between pulley flange and belt. If adjustment is required, loosen cap screws that hold adapter
plate to swingarm and tap differential housing with rubber mallet in desired direction. Check rear
alignment and belt tension again if adjustment is required.
Note: If necessary, apply chalk to edge of belt to aid in getting proper clearance between belt and
pulley flanges. If visible clearance cannot be obtained, be sure belt is not climbing up the side of
pulleys or squeaking as belt is rotated.
9. After all adjustments are made, tighten adjuster lock nuts and tighten pinch block bolts. Tighten
pinch blocks in a crosswise pattern. Go over both sides at least 2 times to seat blocks over pins.
Torque bolts to
25 ft. lbs.
16
Fig. 1
12”
Drive belt deflection
Fig. 2