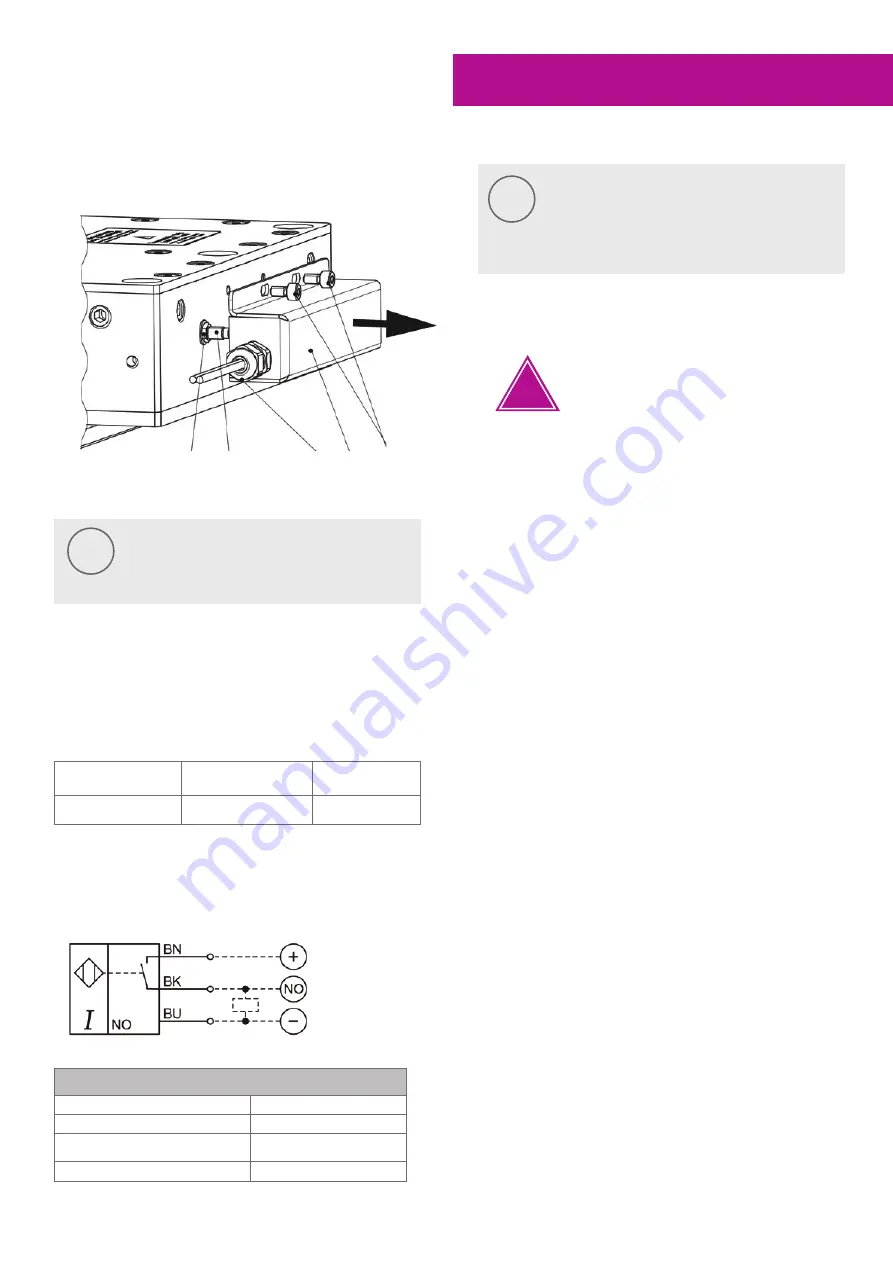
21
9 Switch condition monitoring
www.leantechnik.com
9 Switch condition monitoring
Figure 6
A proximity switch (2) emits a signal for each
brake condition change.
SHB 2 is equipped with 2 proximity switches (2).
Plausibility check
A signal evaluation of both conditions must be
carried out by the customer.
Wiring diagram:
Replacing the proximity switch
Prerequisite
•
Brake is depressurised (closed) on the profile rail.
Disassembly
1. Unscrew the cable gland (3)
2. Unscrew the cylinder screws (5)
3. Remove the cover plate (4)
4. Unscrew the hexagon nut (1), unscrew the proximity
switch (2) and remove.
Installation and adjustment
Initial situation: Proximity switch is not connected
1
2
3
4
5
i
i
!
Note!
Proximity switches are not considered to be
fail-safe, and appropriate access for replace-
ment or adjustment must be possible.
WARNING Load crash possible
Gravity-loaded axles must be fixed in place
before work commences and therefore se-
cured against falling.
Note!
Switching condition monitoring is
set and installed at the factory.
Technical data
PNP/closer
Rated operating voltage
U
e
=24 VDC
Operating voltage
U
e
=10...30 VDC
Cable length
5000mm
Brake open
Pressure on
Signal OFF
Brake closed
Pressure switched off Signal ON
Activity
Result
1. Check whether the brake is depressurised
2. Screw the proximity switch in carefully until
it stops
2.1 Unscrew the proximity switch 1 revolution
(360°)
3. Lock the proximity switch (2) with
a hexagon nut (1)
(Tightening torque: 2 Nm
4. Connect the proximity switch
(see wiring diagram)
"ON" signal
5. Set operating pressure
"OFF" signal
6. Carry out a functional check
6.1 Switch off pressure
"ON" signal
6.2 Switch on pressure
"OFF" signal
7. Pull the cable through the cable gland
(3
8. Screw on the cover plate (4)
9. Tighten the cable gland (3)