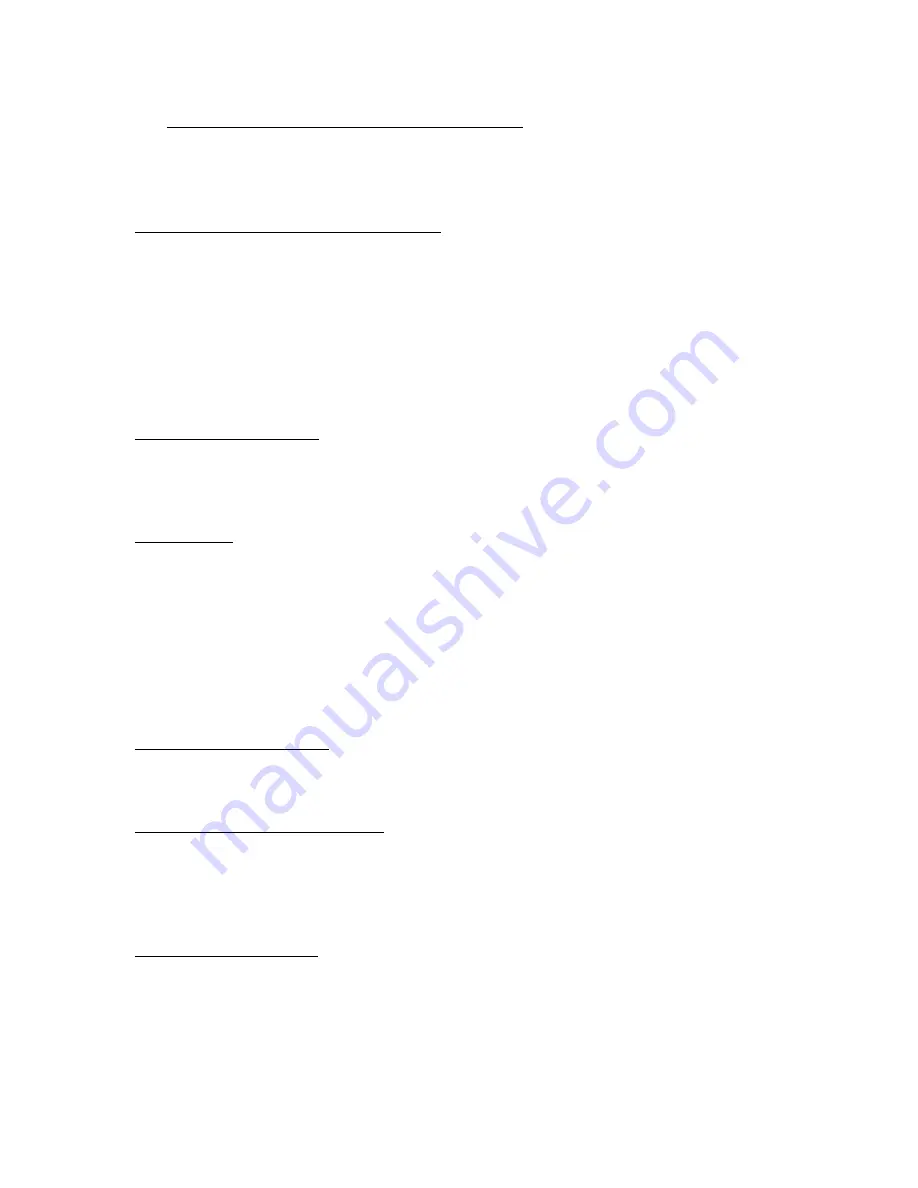
LAWSON ENGINEERS LTD Ref : PJ1682
Issue Date : 06.06.2006
9 SUBSYSTEM DISASSEMBLY / ASSEMBLY
9.1 WINCH DISASSEMBLY PROCEDURE.
WINCH DISASSEMBLY PROCEDURE.
See drawing SW1618A-0001 & SW1542A-0002.
In general the system is designed to be as simple as possible to assemble as well as to
operate and maintain. Assembly / disassembly procedures require no specialised
instructions and are well within the capabilities of a properly trained fitter.
The following points are however included for assistance where it was considered
necessary.
Removal of Bump Frame
1.
Ensure the coiler hydraulic hoses are removed from the support bracket attached
to the bump frame.
Coiling Gear
The coiler has two mounting positions to allow for mounting the winch either on or
behind the skid.
Ensure all hydraulic hoses to motor and electrical cable are disconnected and their ends
plugged.
The coiler drive shaft runs in taper roller bearings. When replacing ensure the securing
locknuts are only tensioned enough to remove any slack between the bearings. Over
tightening the taper roller bearings will result in premature failure.
Removal of Winch Motors
1.
Ensure all hydraulic hoses to motors are disconnected and their ends plugged.
Removal of Winch Drive Gearbox
1.
The pinion is forged onto the output shaft of the gearbox. The whole
assembly comes out of the winch frame in one piece; it is not necessary or possible to
remove the pinion first.
Removal of Winch Drum
1.
Remove coiler and bump frame
2.
Remove the slipring bearing bracket. It is not necessary to support the drum to do
this; the main drive ring bearing can support the drum unaided.
3.
Remove ring gear cover plate.
- 52 -