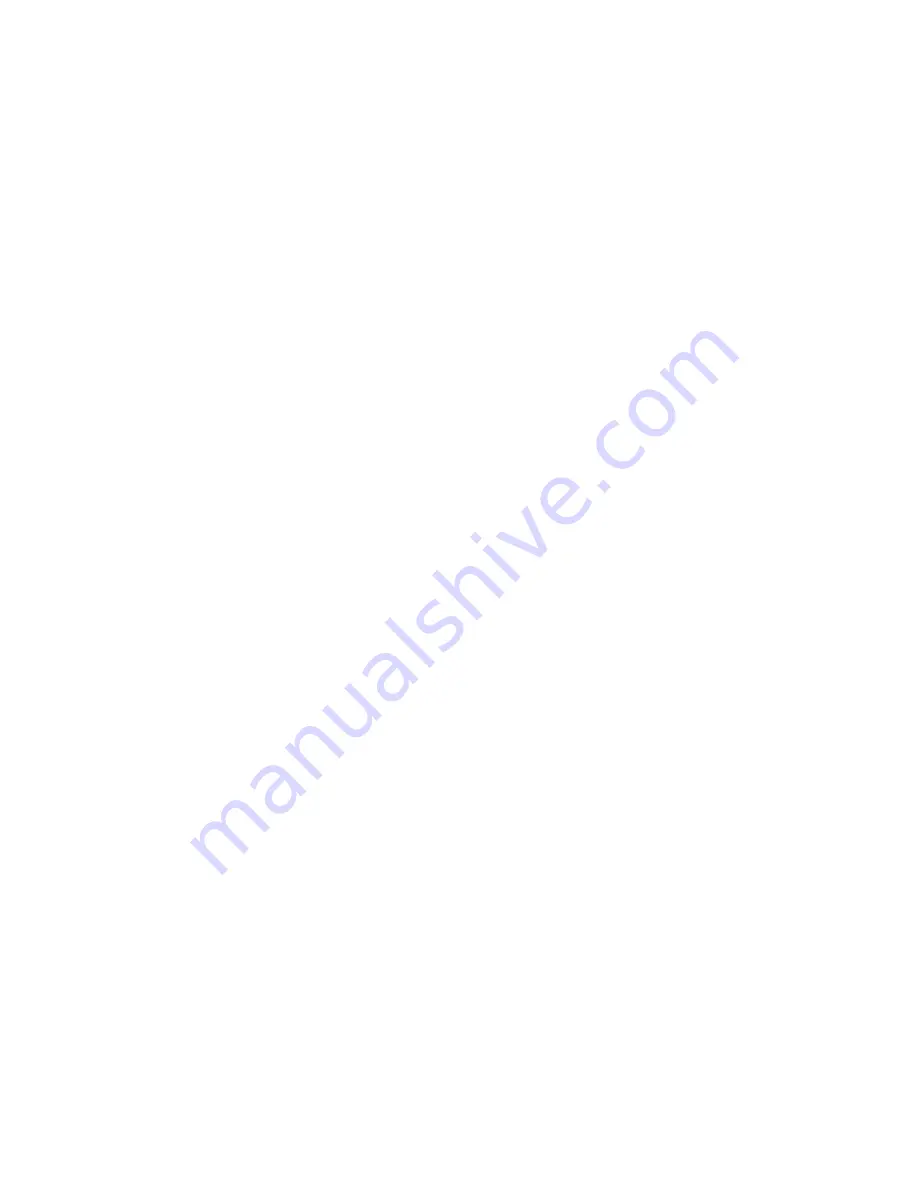
LAWSON ENGINEERS LTD Ref : PJ1682
Issue Date : 06.06.2006
Stage 2.
An axial displacement variable swash plate piston pump
.
It supplies the
coiling gear on the winch, and the various functions on the A-Frame and
Snubber.
Pump Stage 1 has a feedback loop from the Winch Drive and the Winch/A-Frame Stack
to ensure the pump pressure stays at only 20 bar above the required drive pressure, (Load
sensing control).
This is done to reduce heating in the pump when the system is not operating but the pack
is running.
The pump drain line and winch brakes return line are connected direct to the reservoir.
The pump self relieves at 230 bar which prevents the winch circuit from seeing excessive
pressure.
Other power pack equipment includes: -
Seawater oil cooler with external bypass check.
Pressure & return line filters, 10µ abs.
Relief valves for stages 1 & 2.
4 - off lockable suction line isolation valve.
Tank filler point - 1/2" male quick release coupling (mating female half supplied loose
with system)
Tank filler filter 10 µ abs.
Twin 75 kW Star-Delta starter.
Reservoir equipment - Suction strainer 125 µ
Return line diffuser
Level gauge
Reservoir
breather
Heater 2 kW
Oil level/temp switch.
The following is a brief description to the operation of the major valves in the hydraulic
circuit reference drawing SW1673X-0002
Winch Counterbalance valves Item 16.
These valves are fitted to give dynamic
and static control of the load on the winch. The valves also prevent runaway in the event
of a burst hose. They provide pilot pressure to release the brakes but only when sufficient
pressure is available to control the load, in a hoisting or lowering direction.
Brake sequence valves Item 30.
These valves are piloted by the signal
from the Winch Counterbalance valves or motor return line and ensure the brake is not
released prematurely. When
the signal decays they open and divert brake pressure direct
to tank thus giving a fast response to brake operation.
- 4 -