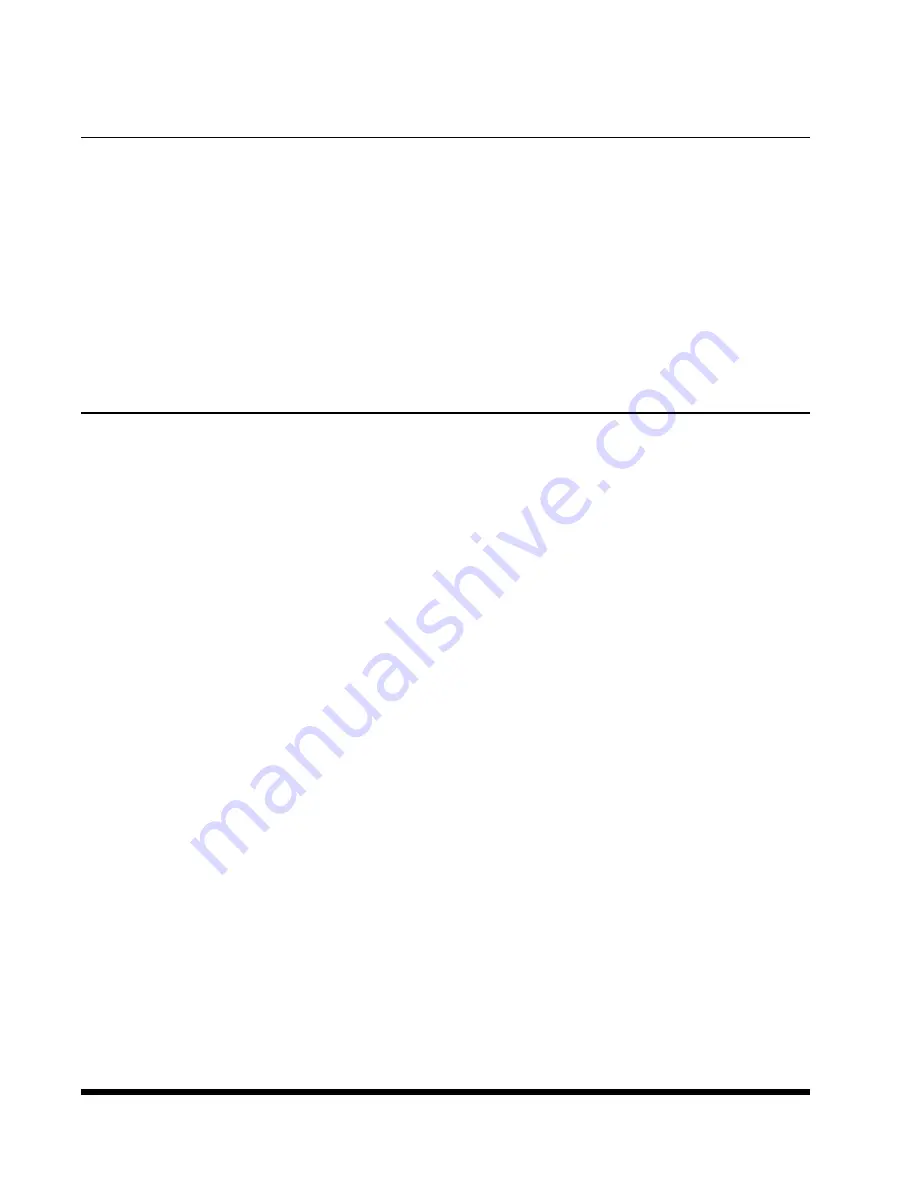
4-5 WHEEL BEARING MAINTENANCE
Wheel bearing maintenance should be per-
formed at the beginning of every season of use.
Check the wheel bearings periodically for exces-
sive end play. If needed, adjust or replace them
using the following procedure:
4-5.1
Place the frame on blocks or stands suffi-
cient to lift the tire clear of the ground.
4-5.2
Remove tire and wheel.
4-5.3
Remove the hub cap, cotter pin, slotted nut
and washer.
4-5.4
Remove the hub. Clean and inspect the
bearings and hub cavity. Replace any worn
or defective parts.
4-5.5
Repack the bearing using a high-quality
wheel bearing grease.
4-5.6
Replace the hub with a new seal and the
inner bearing in place.
4-5.7
Install the outer bearing cone, washer, and
slotted nut.
4-5.8
Tighten the slotted nut while rotating the
hub until there is slight resistance to wheel
rotation. Then, back the slotted nut off one
notch, until the wheel rotates freely without
end play.
4-5.9
Install a new cotter pin and replace the
hub cap.
4-5.10
Reinstall tire and wheel.
4-6 HYDRAULIC MAINTENANCE
4-6.1
Check the tractor hydraulic fluid level per
tractor owners manual and after any leakage.
Check fluid level with the cylinders in the re-
tracted position.
4-6.2
If a cylinder leaks, disassemble the parts
to determine the cause of the leak. Any time
a cylinder is opened up, or whenever any
seal replacement is necessary, it is advisable
to clean all parts and replace all seals Seal
kits are available from your Landoll dealer.
4-6.3
Check all hydraulic hoses weekly, Look for
binding or cracking. Replace all worn or de-
fective parts immediately.
4-4
Summary of Contents for SOIL MASTER II 1200 Series
Page 7: ......
Page 11: ...2 4 Figure 2 1 Rigid 7 9 Shank Spacing...
Page 12: ...2 5 Figure 2 2 Rigid 11 Shank Spacing...
Page 13: ...2 6 Figure 2 3 Rigid 13 Shank Spacing...
Page 14: ...2 7 Figure 2 4 Wing 15 Shank Spacing...
Page 15: ...2 8 Figure 2 5 Wing 17 Shank Spacing...
Page 16: ...2 9 Figure 2 6 Wing 19 Shank Spacing...
Page 17: ...NOTES 2 10...
Page 19: ...3 2 Figure 3 1 Frame Assembly Rigid...
Page 21: ...3 4 Figure 3 2 Frame Assembly Folding...
Page 29: ...3 12 Figure 3 7 Hydraulic Fold Assembly...
Page 31: ...3 14 Figure 3 8 Pull Hitch Installation...
Page 33: ...3 16 Figure 3 9 Coulter Gang Installation...
Page 34: ...3 17 Figure 3 10 Coulter Depth Adjustment...
Page 35: ...3 18 Figure 3 11 Coulter Gang Hydraulic Assembly...
Page 37: ...3 20 Figure 3 12 Clamp Assemblies...
Page 39: ...3 22 Figure 3 13 Electrical Installation...
Page 41: ...3 24 Figure 3 14 1200 Series Decal Placement 1 of 2...
Page 42: ...3 25 Figure 3 15 1200 Series Decal Placement 2 of 2...
Page 51: ......
Page 53: ...NOTES 5 3...
Page 54: ......