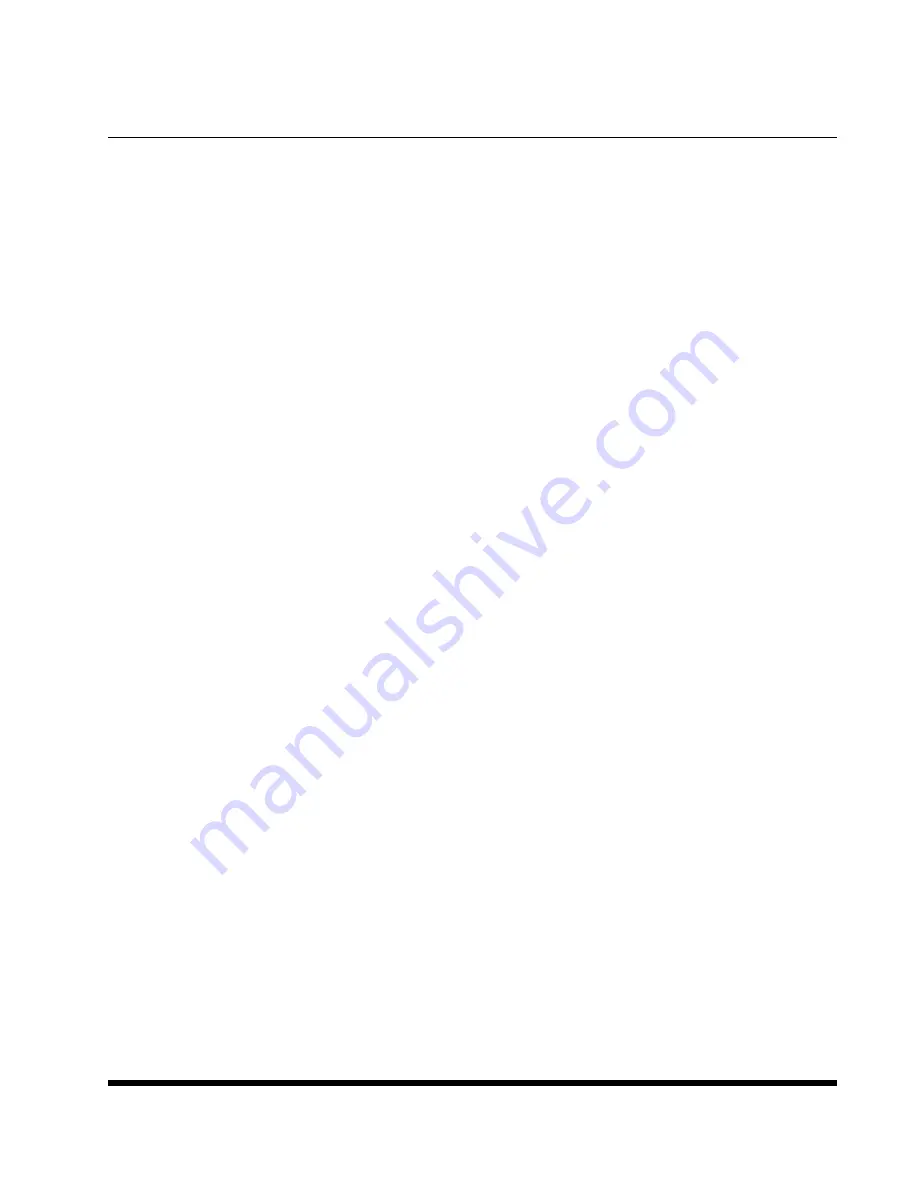
3-6 HYDRAULIC LIFT ASSEMBLY - FOLD MODELS
3-6.1
Unscrew yoke from master cylinder piston
rod. Install stroke control cover and stroke
control on cylinder piston rod. Replace cylin-
der yoke, adjust extended length to 28-1/4"
from hole center to hole center by threading
yoke on piston rod proper distance. Tighten
set screw to lock yoke in place
(See Figure
.
3-6.2
Install main frame lift cylinders (master cyl-
inders with stroke controls are used on the
main frame) ports up, using cylinder pin.
Connect yoke to gauge wheel arm using cyl-
inder lockouts, extended pin and hair pin cot-
ters. Connect anchor end to extended pin
and hair pin cotters
(See Figures 3-3 and
3-6.3
Install wing lift cylinders ports up, using cyl-
inder pins and hair pin cotters.
3-6.4
Screw two adapters and a bushing into
flow divider valve ports (
See Figure 3-6).
3-6.5
Mount flow divider valve on frame with
3/8-16 x 2-1/2" hex head cap screw and split
lock washer. (Note that the bushing is to the
front.)
3-6.6
Mount double pilot check valve on frame,
C
2
port to the front and facing the cylinder,
using 3/8-16 x 1-3/4" hex head cap screws
and split lock washer.
3-6.7
Use hose A to connect from elbow in flow
divider to port V
2
in the double pilot check
valves. (For hose lengths and installation,
see
Table 3-2
and
Figure 3-6)
.
3-6.8
Screw hose B into each end of the swivel
tee and into port V
1
of the double pilot check
valves.
3-6.9
Screw the restrictor into the adapter in port
C
1
of the double pilot check valve.
NOTE: Arrow on restrictor must point toward
cylinder.
3-6.10
Install Hose C between restrictor and base
of master cylinder(s).
3-6.11
Connect Hose D from the master cylinder
rod port to the slave cylinder base port.
3-6.12
Connect Hose E from the C
2
port of the
double pilot check valve to the rod port of
the slave cylinder.
3-6.13
To prevent contamination of hydraulic sys-
tem, plug the open port on the flow divider
and tee.
3-11
Summary of Contents for SOIL MASTER II 1200 Series
Page 7: ......
Page 11: ...2 4 Figure 2 1 Rigid 7 9 Shank Spacing...
Page 12: ...2 5 Figure 2 2 Rigid 11 Shank Spacing...
Page 13: ...2 6 Figure 2 3 Rigid 13 Shank Spacing...
Page 14: ...2 7 Figure 2 4 Wing 15 Shank Spacing...
Page 15: ...2 8 Figure 2 5 Wing 17 Shank Spacing...
Page 16: ...2 9 Figure 2 6 Wing 19 Shank Spacing...
Page 17: ...NOTES 2 10...
Page 19: ...3 2 Figure 3 1 Frame Assembly Rigid...
Page 21: ...3 4 Figure 3 2 Frame Assembly Folding...
Page 29: ...3 12 Figure 3 7 Hydraulic Fold Assembly...
Page 31: ...3 14 Figure 3 8 Pull Hitch Installation...
Page 33: ...3 16 Figure 3 9 Coulter Gang Installation...
Page 34: ...3 17 Figure 3 10 Coulter Depth Adjustment...
Page 35: ...3 18 Figure 3 11 Coulter Gang Hydraulic Assembly...
Page 37: ...3 20 Figure 3 12 Clamp Assemblies...
Page 39: ...3 22 Figure 3 13 Electrical Installation...
Page 41: ...3 24 Figure 3 14 1200 Series Decal Placement 1 of 2...
Page 42: ...3 25 Figure 3 15 1200 Series Decal Placement 2 of 2...
Page 51: ......
Page 53: ...NOTES 5 3...
Page 54: ......