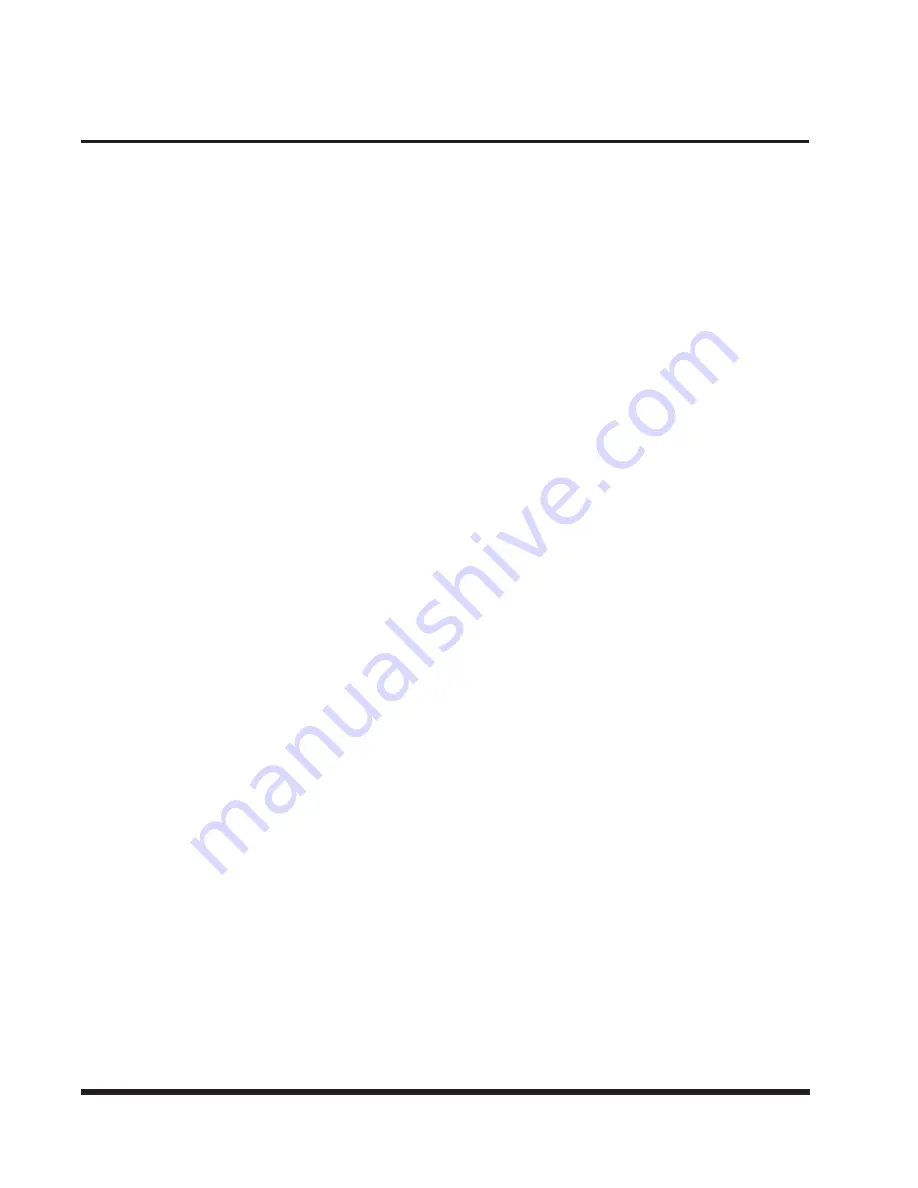
ii
REPORTING SAFETY DEFECTS
If you believe that your vehicle has a defect which could cause a crash or could
cause injury or death, you should immediately inform the National Highway Traffic
Safety Administration (NHTSA) in addition to notifying Landoll Manufacturing.
If NHTSA receives similar complaints, it may open an investigation, and if it
finds that a safety defect exists in a group of vehicles, it may order a recall and
remedy campaign.
However, NHTSA cannot become involved in individual prob-
lems between you, your dealer, or Landoll Manufacturing.
To contact NHTSA, you may either call the Auto Safety Hotline toll-free at 1-800-
424-9393 (or 366-0123 in Washington, D.C. area) or write to: NHTSA, U.S. Depart-
ment of Transportation, Washington, D.C. 20590. You can also obtain other infor-
mation about motor vehicle safety from the Hotline.
In the event of a defect or problem with your LANDOLL equipment, please notify
LANDOLL CORPORATION:
LANDOLL CORPORATION
SALES AND SERVICE
1900 NORTH STREET
MARYSVILLE, KANSAS 66508
OR PHONE:
1-800-HAULOLL
(1-800-428-5655)
FAX NO.: (785)562-3240
FOR REPLACEMENT PARTS:
(785)562-4650
1-800-423-4320
FAX NO.: (785) 562-4654
Summary of Contents for 900B Series
Page 8: ......
Page 12: ......
Page 52: ...4 12 Figure 4 5 Wired Remote Control Diagrams...
Page 53: ...4 13 Figure 4 6 Tandem Triple Axle Air Ride Suspension Figure 4 7 Air Ride Height Adjustment...
Page 56: ...4 16 Figure 4 9 Checking Axle Alignment Figure 4 10 Examples of Camber...
Page 61: ...4 21 Figure 4 13 Axle and Brake Assembly...
Page 71: ...4 31 Figure 4 21 Crank Landing Gear Assembly...
Page 81: ...5 9 NOTES...
Page 82: ......