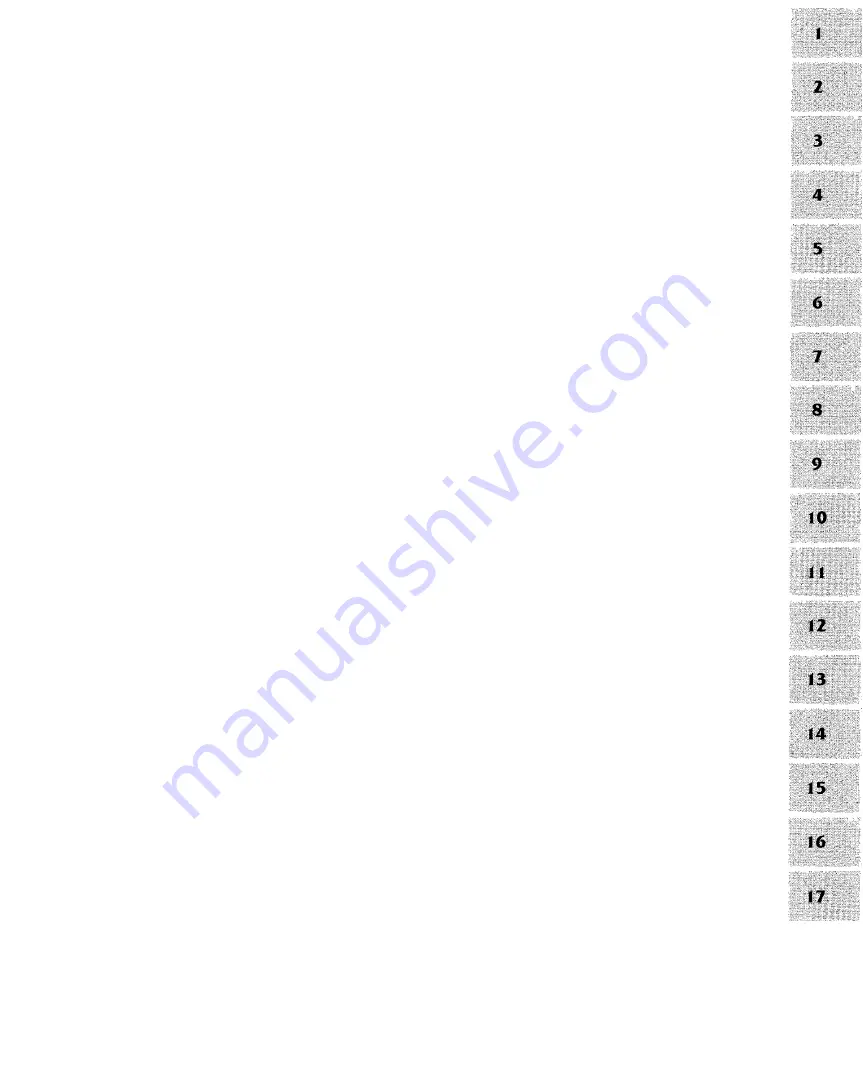
General Information
Troubleshooting
Lubrication, Maintenance and Tune-up
Engine
Fuel and Exhaust Systems
Electrical System
Oil Injection System
Cooling System
Recoil Starter
Drive System
Brakes
Chaincase, Jackshaft and Front Axle
Front Suspension and Steering
Track and Rear Suspension
Off-season Storage
Index
Wiring Diagrams
Summary of Contents for MM600D
Page 5: ......
Page 6: ......
Page 104: ...98 CHAPTER FOUR ENGINE MOUNTS ...
Page 137: ...FUEL AND EXHAUSTSYSTEMS 131 ...
Page 144: ...138 CHAPTER FIVE CARBURETOR HEATER SYSTEM Carburetorheater control valve ...
Page 211: ...BRAKES 205 Wear limit ...
Page 226: ...220 CHAPTER TWELVE ...
Page 228: ...222 CHAPTER TWELVE ...
Page 229: ...CHAINCASE JACKSHAFTAND FRONT AXLE 223 ...
Page 230: ...224 CHAPTER TWELVE ...
Page 254: ...248 CHAPTER THIRTEEN FORWARD Negative Positive O0Camber Angle finder ...
Page 277: ...1 Wiring Diagrams ...
Page 282: ...NOTES ...