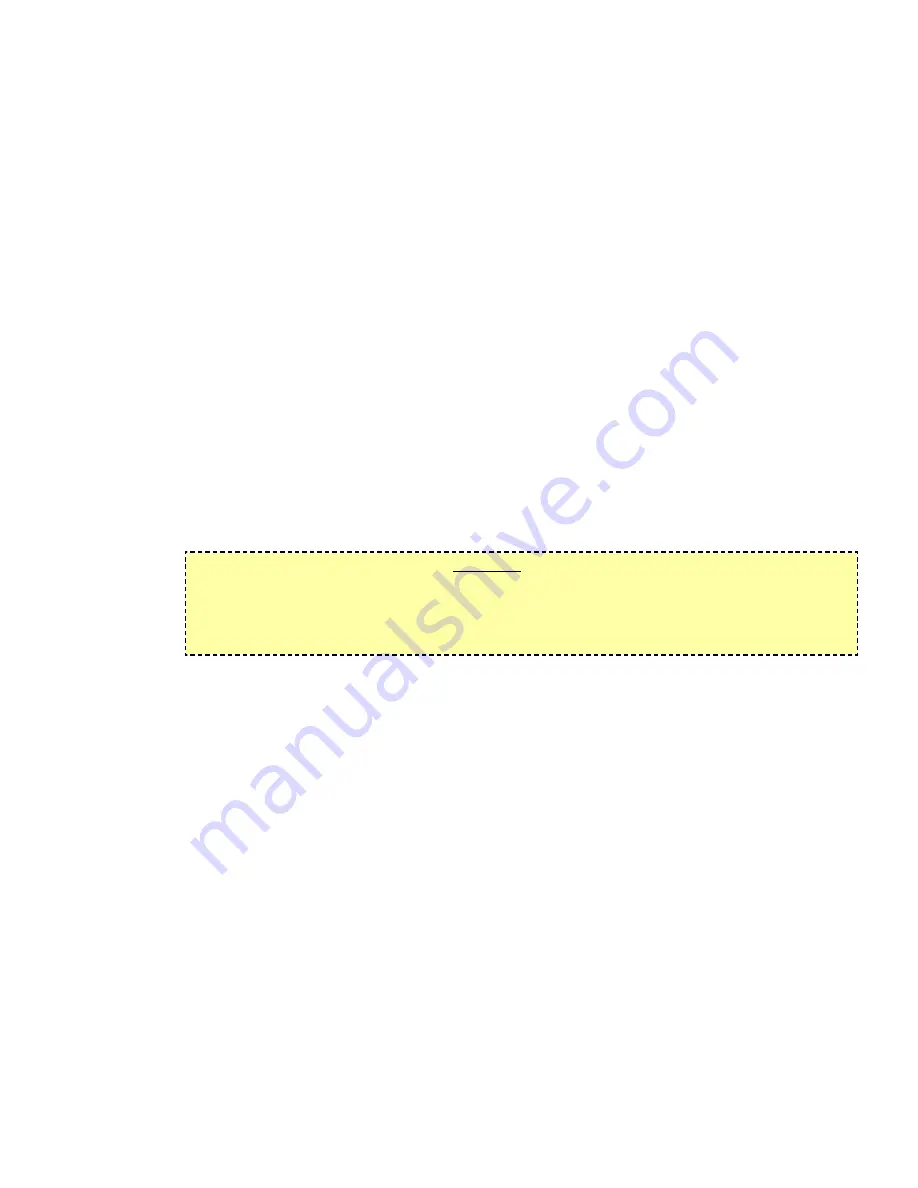
water to flow to the check valve on the concentrate container and simultaneously operates the
concentrate pump. Water flows through the check valve, the concentrate pump, and the spout. The
check valve positioned at the concentrate container prevents flush water from entering the
concentrate container.
3.7
REFRIGERATION SYSTEM
An ice bank is formed and maintained on the copper tube evaporator located in the water bath
compartment of the tank assembly. Water is continually circulated by the agitator motor across the
ice bank and around the copper water coil. Water temperature is maintained at 32°F (0°C).
Because the water compartment and concentrate compartment form an integral aluminum die
casting, the concentrate compartment is maintained at a constant 35°F (0°C) temperature. When a
product is dispensed, water is drawn through the copper water coils and chilled. As the ice bank is
depleted, the ice bank control senses that the ice is melting and causes the compressor and
condenser fan motor to start. When the ice bank is rebuilt, the control shuts off the compressor and
condenser fan motor.
The compressor and condenser fan motor will operate periodically, even though no drinks are being
dispensed, in order to maintain the ice bank. If the unit is unplugged or power is disrupted while
operating, the compressor will not restart for a period of time during which the refrigerant pressures
equalize [approximately five (5) minutes]. This feature protects the compressor from premature
failure.
4.
RELOCATING OR SHIPPING UNIT
4.1
REMOVING AN OPERATING UNIT
A. Perform FLUSH operation on each side of unit until a clean stream of water is being dispensed.
B. Remove Minute Paks
®
.
CAUTION
IF UNIT IS TO BE TRANSPORTED OR STORED WHEN AMBIENT TEMPERATURE IS 32°F (0°C)
OR LOWER, STEPS C AND D MUST BE PERFORMED TO PREVENT THE WATER SYSTEM
FROM FREEZING AND DAMAGING THE UNIT. DO NOT USE CO
2
GAS TO PURGE WATER
FROM UNIT AS IT WILL CAUSE A HEALTH HAZARD.
C. Shut off inlet water supply. Disconnect inlet water tube from bottom of unit. About six (6) ounces
(177.4 ml) of water will drain out of the unit as the vacuum breaker opens, allowing air into
system.
D. Depress each dispensing paddle. This allows additional air into the system and will cause a few
more ounces (ml) of water to drain from unit.
E. Turn key switch OFF.
F.
Unplug unit power cord from electrical outlet.
G. Remove agitator deck (see Section 6.14), and using plastic tubing, siphon water out of ice bath
compartment. It will be necessary to pour about 12 ounces (354.8 ml) of warm water
(do
NOT
use extremely hot water)
into the ice bath compartment to completely melt the ice bank. Drain
the remaining water and replace agitator deck and secure with nuts.
H. Remove drip tray and cup rest. Clean and reinstall. Wipe exterior surfaces of unit with a clean
damp cloth.
4.2
TRANSPORTING UNIT
The best method of handling and transporting a unit is to remove the legs and secure the unit to a
plywood shipping base. If it is to be handled and transported with the legs assembled to the unit,
special care should be taken not to damage unit.
DO NOT LAY UNIT ON SIDE OR BACK.
4.3
SHIPPING UNIT
If a unit is to be shipped by a common carrier, it must be secured to the plywood shipping base and
repacked in the original carton with the inner packaging material.
For this reason, it is wise to retain
the original packing material.
8
dinecompany.com