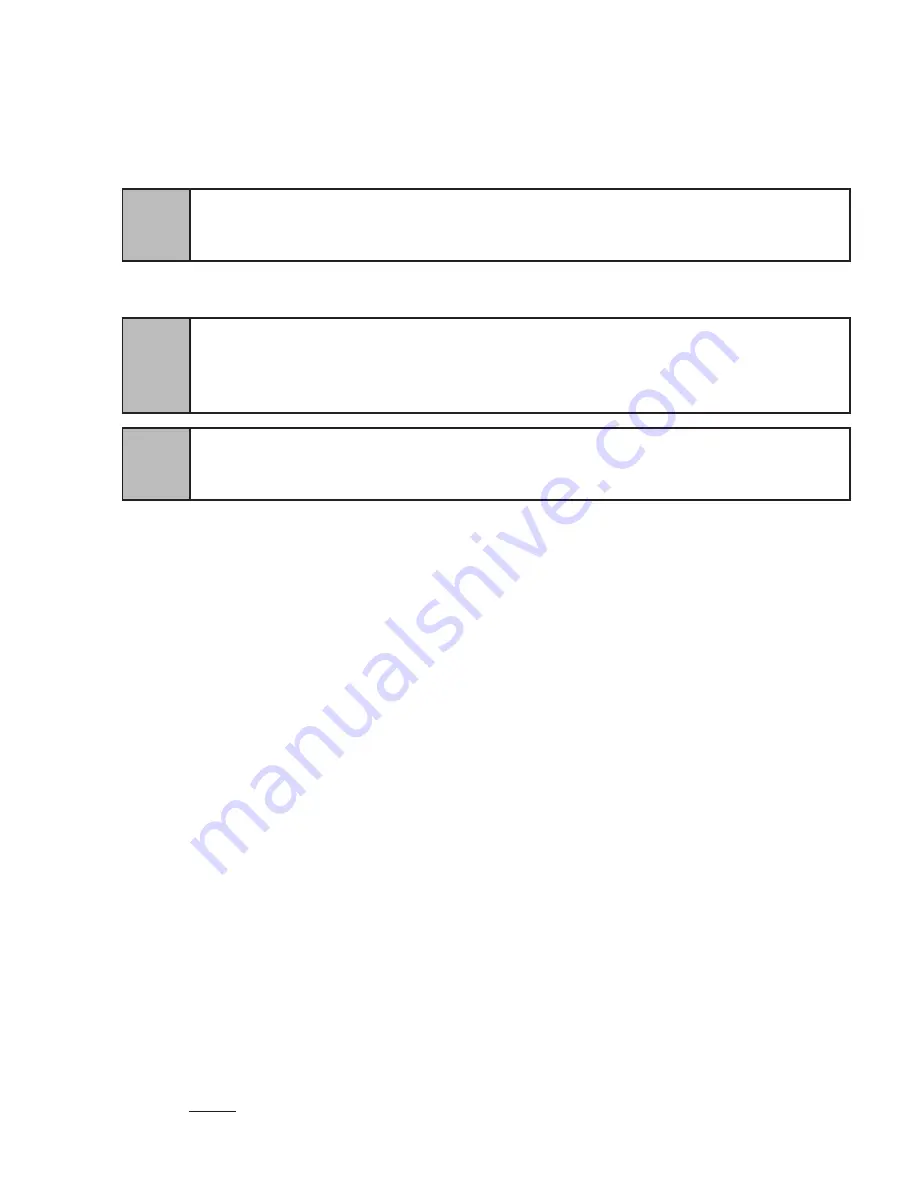
1.6 FILLING UNIT WITH WATER
A. Remove the bonnet from the unit.
B. Remove the yellow plastic plug (located on the front of the unit’s carbonator deck) from the unit’s
fill hole.
C. Using a funnel or tube, fill the water bath compartment with water until it flows out of the
overflow tube into the drip tray.
D. Replace the yellow plug.
1.7 CONNECTING TO ELECTRICAL POWER
A. If the unit is equipped with a built-in carbonator, disconnect the power supply to the carbonator
motor by disconnecting the four pin connector, located near the top of the electrical control box
on the refrigeration deck.
B. Check the dispenser serial number plate for unit’s correct electrical requirements. Do not plug
into wall electrical outlet unless serial number plate current shown agrees with local current
available.
C. Route the power supply cord to a grounded electrical outlet of the proper voltage and amperage
rating, and plug in the unit. This will turn on the refrigeration system and allow it to start cooling,
while completing the rest of the installation. The agitator motor will start immediately, but the
compressor and fan motor will not start until the five (5) minute delay has elapsed.
1.8 CONNECTING PYTHON TO REMOTE RECIRCULATING UNIT (SEE FIGURE 1)
A. All remote units have the plain water feature, factory installed. If plain water is not wanted,
remove the barbed fitting and short extension fitting, and cap end of plain water line with cap
from accessory kit.
B. Determine length of python required, allowing additional length as required for servicing. The
length of the python must not exceed 25 feet (8 meters) if built-in syrup pumps are being used.
C. Position one end of python near remote unit. Slit the python insulation back 18 inches (45 cm)
from end and roll insulation back to expose individual tubes. Take care not to cut into tubing
bundle.
D. Slide the tube insulation from the accessory kit over one of the 3/8 inch ID plastic soda lines.
Connect this line to the 3/8 inch barbed 90° elbow located on the inlet to the recirculating pump.
Secure with an Oetiker clamp from the kit.
E. Connect the other 3/8 inch ID plastic soda line to the 3/8 inch barbed fitting on the stainless steel
soda recirculating Pump. Secure with Oetiker clamp from kit.
F. Connect each of the 1/4 inch ID plastic lines from the python to the barbed fittings on each of
the stainless steel lines (and plain water line, if used). Secure with Oetiker clamps. The
individual barbed fittings for the lines can be removed for insertion into the python tubing by
removing the “U” shaped retainer pin and pulling the fitting off of syrup line.
NOTE:
Do not insulate connections at this time. Leave all connects exposed for inspection for
leaks. Refer to Section 1.17 to complete insulation.
2
!
CAUTION
THE WATER BATH COMPARTMENT MUST BE FILLED WITH WATER BEFORE
PLUGGING IN THE UNIT. OTHERWISE, THE COMPRESSOR DECK AND CONDENSER FAN
MAY NOT OPERATE PROPERLY.
!
WARNING
THIS UNIT MUST BE PROPERLY ELECTRICALLY GROUNDED TO AVOID
POSSIBLE FATAL ELECTRICAL SHOCK OR SERIOUS INJURY TO THE OPERATOR. THE
POWER CORD IS PROVIDED WITH A THREE PRONG GROUNDED PLUG. IF A THREE-HOLE
GROUNDED ELECTRICAL OUTLET IS NOT AVAILABLE, USE AN APPROVED METHOD TO
GROUND THE UNIT.
!
WARNING
FAILURE TO DISCONNECT THE MOTOR POWER SUPPLY WILL DAMAGE THE
CARBONATOR MOTOR AND PUMP AND VOID THE WARRANTY.
Summary of Contents for DELTA III 9100 Series
Page 31: ...26 NOTES...