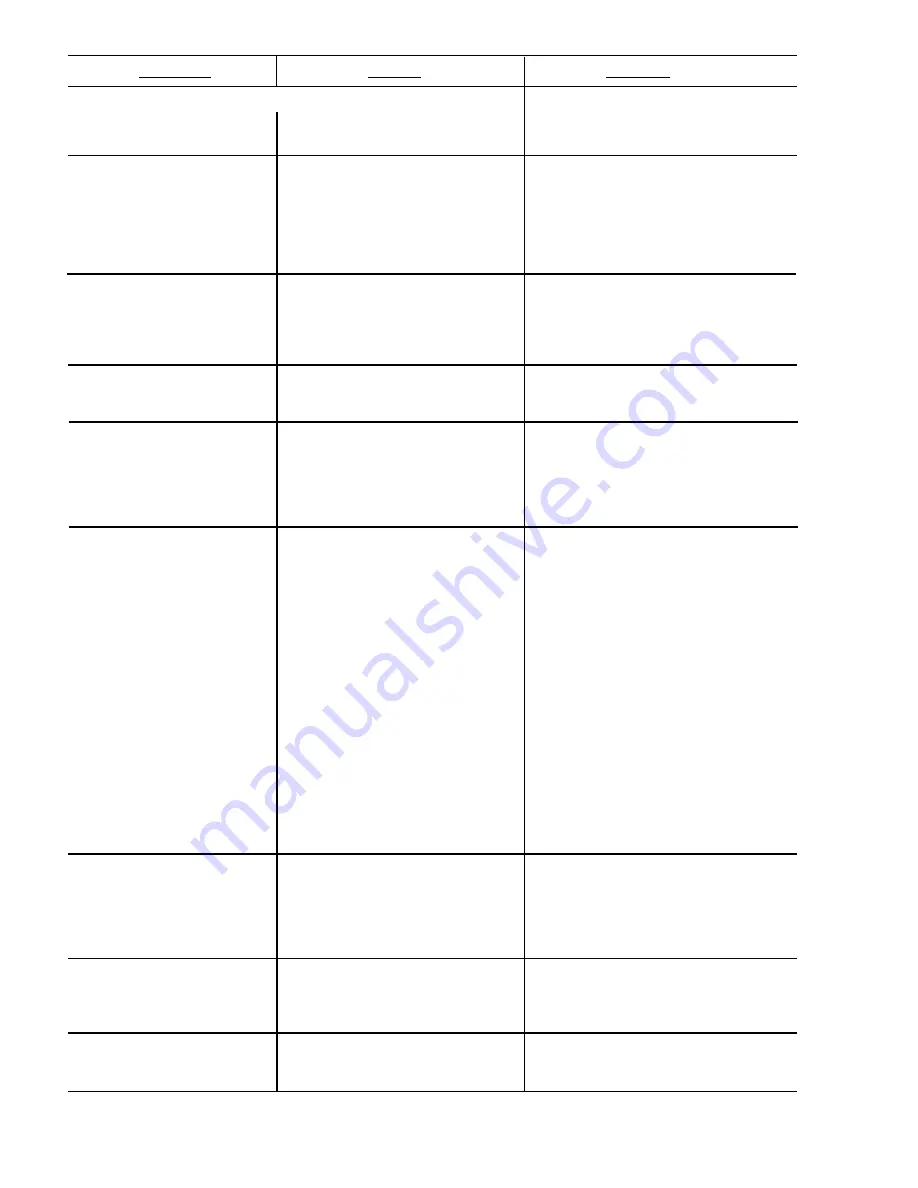
Section 8.17 continued from previous page.
F. Refrigerant leak.
F. Repair and recharge.
G. Compressor malfunctioning.
G. Replace compressor.
8.18
Compressor runs
A. Low water level in water
A. Add water to water bath until water
normally, but water
bath.
runs out of overflow into drip tray.
line is frozen.
B. Syrup in water bath.
B. Drain water from water bath and
refill with clean water.
C. Water cage is out of position.
C. Reposition water cage.
D. Low refrigerant charge/slow
D. Find and repair leak. Recharge
refrigerant leak
system.
8.19
Compressor cycles
A. PCB malfunctioning
A. Replace PCB assembly.
on and off frequently
B. Defective probe.
B. Replace probe.
during the initial
C. Air flow blocked.
C. Check to ensure proper air
pulldown and/or
clearance is provided (see
normal operations.
Section 1.4).
8.20
Plain water flow is
A. Insufficient incoming supply
A. Verify incoming supply water
insufficient.
water and/or pressure.
pressure is a minimum of zero (0)
PSI flowing.
8.21
Suspect faulty PCB.
A. PCB not receiving proper
A. Check power from transformer on
input voltage.
pins 4 and 5 of J10.
B. Green light not flashing (off
B. Replace PCB.
or continuously on).
C. Yellow lights off and green light C. Check fuses F1 and F2, and also
is on when key switch is on.
connection at J10.
8.22
Circuit breaker tripping.
A. Pump is shorted.
A. Disconnect pump and restore
power. If breaker does trip, then
pump is OK. If breaker does not
trip, replace pump.
B. Refrigeration relay is bad.
B. Detect short by disconnecting J10
connector (24VAC input) from
PCB. Restore power. If breaker
doesn’t trip, then replace
refrigeration relay. If breaker does
trip, then refrigeration relay is OK.
Reconnect J10 connector.
C. Secondary wire harness is
C. Detect short by disconnecting both
bad.
secondary transformer fastons and
restore power. If it does not trip,
locate short in secondary harness
between transformer and PCB.
D. Transformer failure.
D. Detect short by disconnecting both
primary transformer fastons and
restore power. If breaker doesn’t
trip, replace transformer.
8.23
BIB pump does not
A. Out of CO
2
, CO
2
not turned
A. Replace CO
2
supply, turn on CO
2
operate when
on, or low CO
2
pressure.
supply, or adjust CO
2
pressure to
dispensing valve is
70-80 PSI.
opened.
B. Out of syrup.
B. Replace syrup supply.
C. BIB connector not tight.
C. Fasten connector tightly.
D. Kinks in syrup or gas lines.
D. Straighten or replace lines.
8.24
BIB pump operates but
A. Leak in syrup inlet or outlet
A. Replace line.
no flow.
line.
B. Defective BIB pump check
B. Replace BIB pump.
valve.
8.25
BIB pump continues to
A. Leak in suction line.
A. Replace line.
operate when bag is
B. Leaking o-ring on pump inlet
B. Replace o-ring.
empty.
fitting.
15
TROUBLE
CAUSE
REMEDY