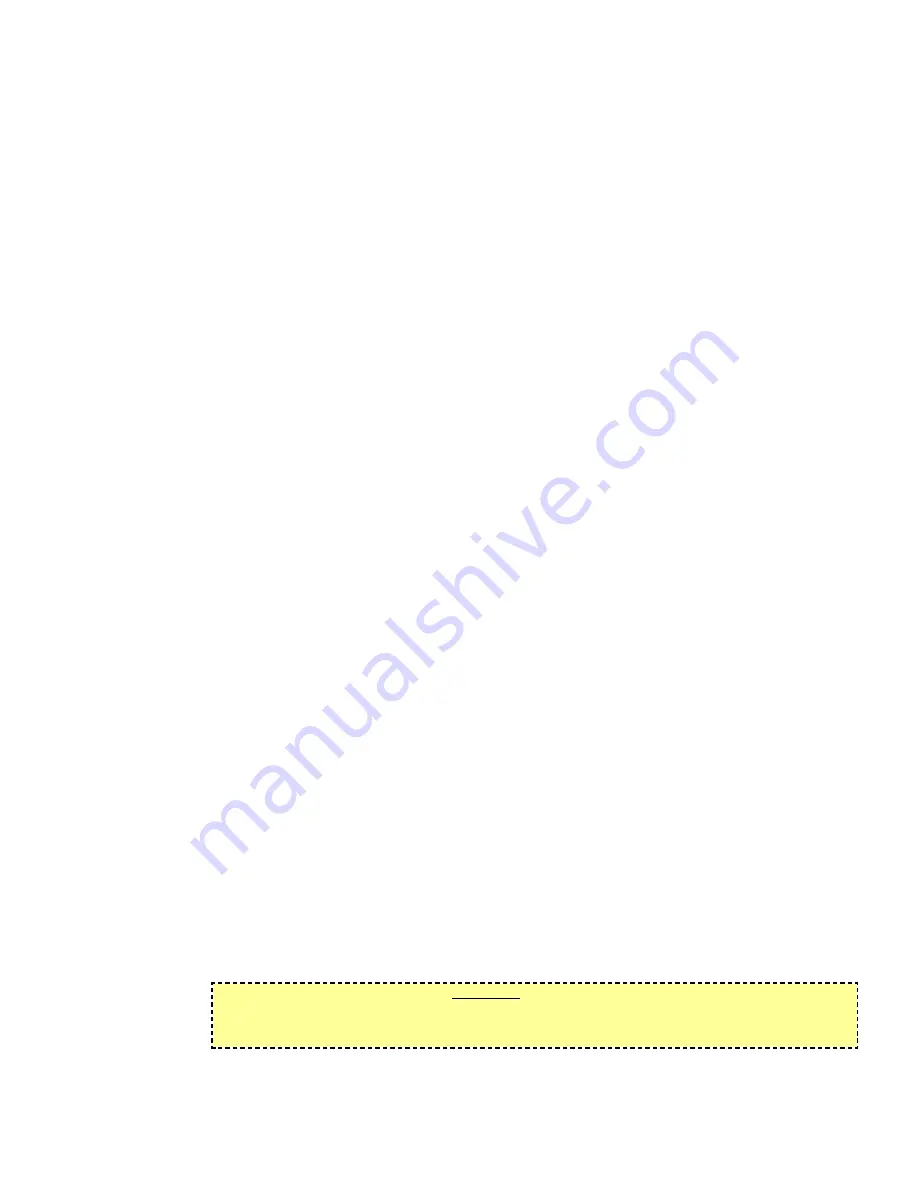
(7.4 ml/sec) to .40 oz/sec (11.8 ml/sec) to obtain a finished drink flow rate from 1.45 oz/sec
(41 ml/sec) to 2.40 oz/sec (71 ml/sec).
Adjusting the flow control
clockwise will increase
the flow,
while turning it
counter-clockwise will decrease
the flow.
The water flow control modules are gray
in color and are plumbed to the center fitting on the nozzle. The syrup flow control modules are
black and are plumbed to the three outer fittings on the nozzle. The unit should have been running
for at least one hour before attempting to set ratio. The drink temperature should be no higher than
40° F (4.4° C) when the ratio is set.
6.2
ADJUSTING WATER FLOW
A. Remove screws under Valve Shroud and open the Valve Shroud to expose the valve modules.
B. Disconnect the syrup modules from the PCB to disable syrup flow.
C. Hold a Lancer brix cup under the nozzle and dispense water into the cup for four seconds.
Divide number of ounces (ml) of water in cup by four to determine water flow rate per second.
D. To obtain desired flow, use a screwdriver to adjust the water flow control. Recheck as
necessary.
E. Repeat process for other nozzle and water flow controls.
6.3
ADJUSTING SYRUP FLOW
A. Reconnect syrup modules to PCB.
B. Remove nozzle by twisting counter-clockwise and pulling down.
C. Install the Model 600 syrup separator (54-0282) by engaging tangs on nozzle body and turning
clockwise. Lubrication of the separator seal is recommended (use 111 lubricant or another FDA
approved lubricant). Activate valves momentarily to fill the separator tube.
D. Hold the brix cup under the separator and dispense syrup and water into the cup.
E. Use a screwdriver to obtain the proper brix by adjusting the syrup flow control. Recheck as
necessary.
F. Repeat process for other syrup modules plumbed to the nozzle.
G. Remove separator, replace nozzle, and repeat for other nozzle.
H. After all modules are brixed, close Valve Shroud and replace screws.
6.4
CLEANING AND SANITIZING PROCEDURES
A.
VALVE AND SYSTEM SANITIZING
1. The complete valve and dispenser system must be sanitized during initial installation.
Follow the manufacturer’s instructions when scheduling and conducting dispenser
sanitizing. The valve may remain on the dispenser during the sanitizing process.
2. To purge syrup, shut off water at backblock and hold keypad switch down for five (5)
seconds. Syrup will purge for as long as the keypad switch is held down.
6.5
DAILY NOZZLE/DIFFUSER CLEANING (SEE FIGURE 3)
A. The Multiflavor Nozzles (MFN) supplied on your Lancer 600 dispenser require low
maintenance. They are “mix in air” nozzles which means that the syrup/soda water interaction
begins after each of the two fluids leave the confines of the nozzle. Therefore, bacterial growth
should not occur within the syrup portion of the nozzle.
The Lancer MFN is a “wipe clean”
design.
B. Use the following procedure to clean the nozzle assembly each day:
1. Remove nozzle housing by twisting it counter-clockwise and pulling it down.
2. Wash the nozzle with warm water.
3. Wet a clean cloth in warm, soapy water.
4. While the nozzle housing is removed, wipe down the perimeter and end of the nozzle body.
5. Rinse nozzle body with clean warm water and towel dry.
CAUTION
USE CARE TO INSURE O-RING IS NOT TORN OR OTHERWISE DAMAGED. IF DAMAGED,
REPLACE O-RING.
6. Make certain the nozzle o-ring is in place around the nozzle mounting area on the valve. If
necessary, slide a new nozzle o-ring (PN 02-0228) onto the nozzle mounting area.
7. If needed, apply 111 lubricant (or another FDA approved lubricant) to the o-ring on the
8