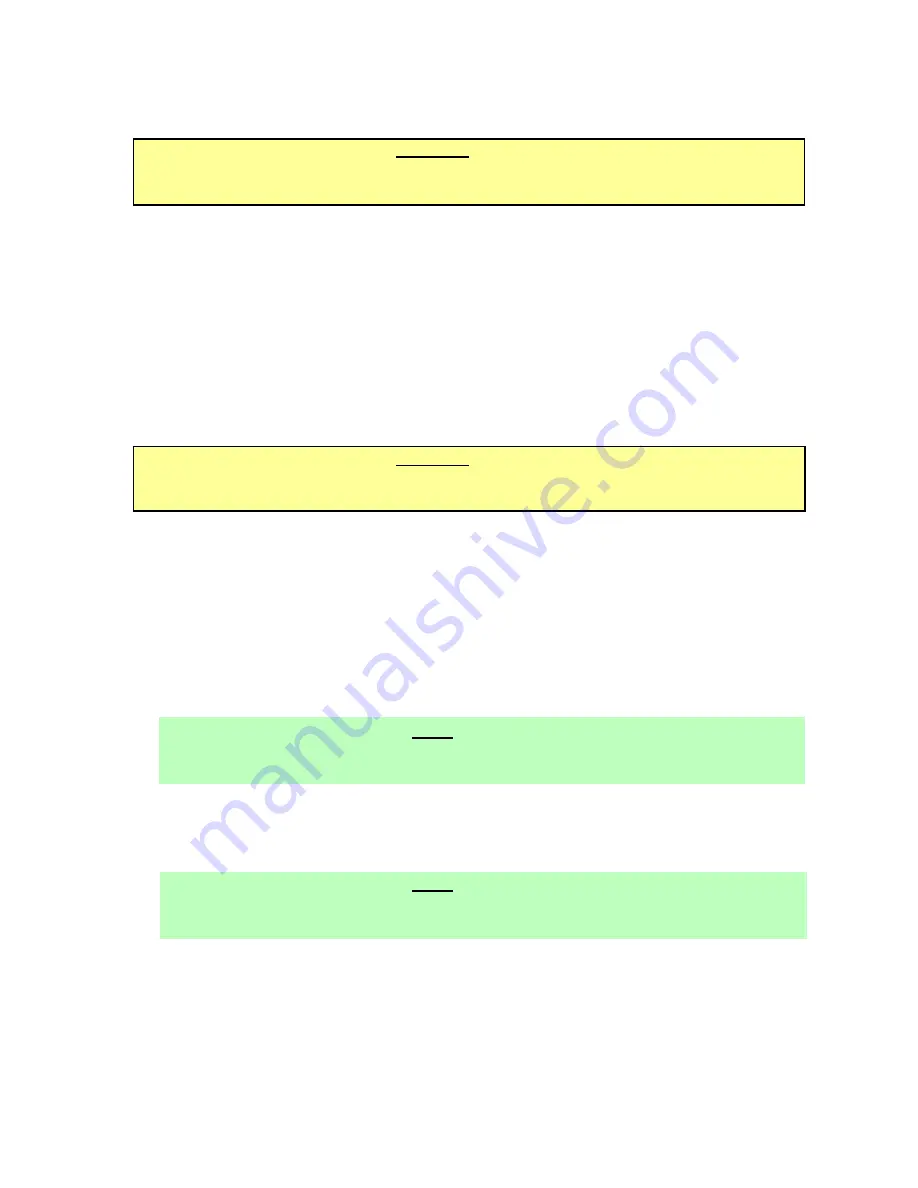
7
water. Connect CO
2
supply hose to tank and pressurize.
C. Activate valve until water is dispensed. Flush and rinse line and fittings for a minimum of
60 seconds to remove all traces of residual product.
WARNING
TO AVOID POSSIBLE PERSONAL INJURY OR PROPERTY DAMAGE, DO NOT ATTEMPT TO
REMOVE SYRUP TANK COVER UNTIL CO
2
PRESSURE HAS BEEN RELEASED FROM TANK.
D. Disconnect CO
2
supply hose from the water filled syrup tank.
E. Following the instructions as described in Section 2.2 above, mix appropriate amount of
cleaning solution. Fill a tank with this solution. Connect hose half of syrup line to the tank.
Connect CO
2
supply hose to tank and pressurize.
F.
Activate valve and draw cleaning solution through lines for a minimum of 60 seconds. This will
ensure line is flushed and filled with cleaning solution. Allow line to stand for at least
30 minutes.
G. Disconnect CO
2
supply hose from the tank.
H. Connect hose half of syrup line to a tank filled with clean, potable, water at a temperature of
90° to 110°F. Connect CO
2
supply hose to tank and pressurize.
I.
Activate valve to flush and rinse line and fittings for a minimum of 60 seconds to remove all
traces of cleaning solution. Continue rinsing until testing with phenolpthalein shows that the
rinse water is free of residual detergent.
WARNING
TO AVOID POSSIBLE PERSONAL INJURY OR PROPERTY DAMAGE, DO NOT ATTEMPT TO
REMOVE SYRUP TANK COVER UNTIL CO
2
PRESSURE HAS BEEN RELEASED FROM TANK.
J.
Disconnect CO
2
supply hose from the tank.
K. Following the instructions as described in 2.2 above, mix appropriate amount of sanitizing
solution. Fill a tank with this solution. Connect hose half of syrup line to the tank. Connect
CO
2
supply hose to tank and pressurize.
L.
Activate valve and draw sanitizing solution through line for a minimum of 60 seconds. This
will ensure line is flushed and filled with sanitizing solution. Allow line to stand for at least
30 minutes.
M. Disconnect CO
2
supply hose from the tank.
N. Reconnect syrup lines to syrup containers (for example, quick disconnects, figal containers,
etc.) and ready unit for operation.
O. Draw drinks to refill lines and flush the sanitizing solution from the dispenser.
NOTE
Please note that a fresh water rinse cannot follow sanitization of equipment.
Purge only with
the end use product until there is no after taste in the product.
This is an NSF requirement.
P.
Test dispenser in normal manner for proper operation. Taste dispensed product to ensure there
is no off-taste. If off-taste is found, additional flushing of syrup system may be required.
Q. Repeat cleaning, rinsing, and sanitizing procedures for each valve and each circuit.
2.6
CLEANING AND SANITIZING BEVERAGE COMPONENTS - BAG-IN-BOX SYSTEMS
NOTE
Extended lengths of product lines may require more time for flushing and rinsing lines than
stated below.
A. Disconnect syrup quick disconnect coupling from syrup packages and connect coupling to a bag
valve removed from an empty Bag-in-Box (BIB) package.
B. Place syrup inlet line in a clean container filled with clean, potable, room temperature water.
C. Activate valve until water is dispensed. Flush and rinse line and fittings for a minimum of
60 seconds to remove all traces of residual product.
D. Following the instructions as described in 2.2 above, mix appropriate amount of cleaning
solution in a clean container. Place syrup inlet line in container filled with cleaning solution.
E. Activate valve and draw cleaning solution through lines for a minimum of 60 seconds. This
will ensure line is flushed and filled with cleaning solution. Allow line to stand for at least