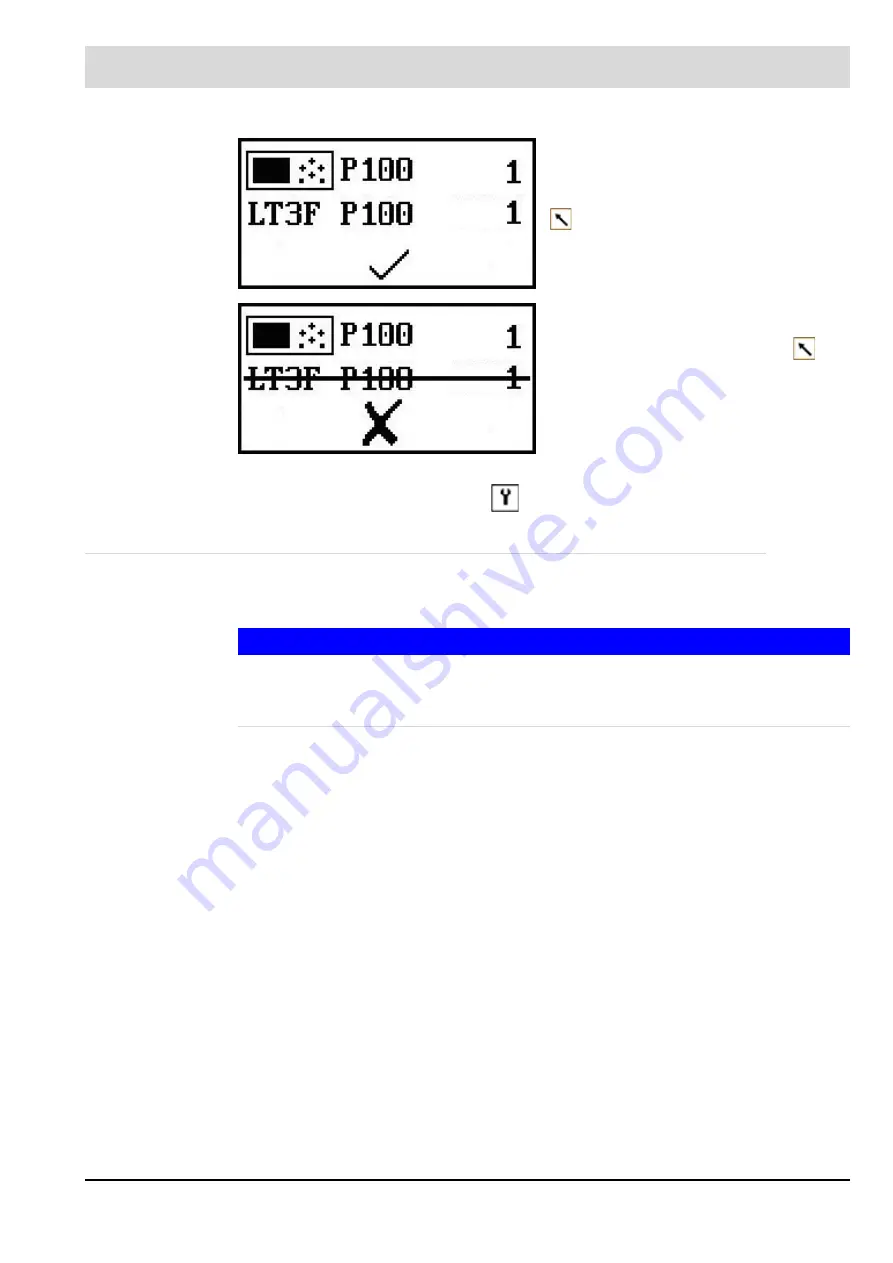
24
5
Maintenance
•
The status line shows this symbol
.
5.1.6
Response of the Internal Resistance Regulation
The internal ceramic resistance between the reference and O
2
electrodes (R
ki
O
2
) is a function
of the sensor temperature, which is constantly regulated for a perfect function of the probe.
NOTICE
The optimum operating point of the LS2 lies at a point R
ki
O
2
about 15
This value must be reached before the first offset calibration or after a probe replacement is
triggered.
If the measured R
ki
O
2
deviates too strongly from the optimum setpoint value R
ki
S = 15
(see menu 213) the installation situation of the probe must be changed for optimum operation:
R
ki
O
2
> 15
•
The probe does not become hot enough:
–
The probe was installed in a cold spot and is thus cooled.
Determine a new installation site.
–
If necessary check whether a R
ki
O
2
of 15
is reached when it is disassembled.
If a too high R
ki
O
2
is assumed by the internal resistance regulation, the probe func-
tions outside of its optimum operating point.
R
ki
O
2
< 15
•
The internal resistance regulation automatically sets the R
ki
setpoint value to 15
:
–
After 30 minutes in fault-free measurement operation and subsequent offset calibra-
tion
–
After 120 minutes in fault-free measurement operation without an offset calibration
Wait until the display shows the transmis-
sion’s end.
Return to the SETTINGS menu with the key
.
If the procedure is cancelled or in case of
timeout this display is shown. BACK
to
the SETTINGS menu.
Summary of Contents for KS1D
Page 2: ......
Page 56: ...55 11 Appendix 11 2 EU Declaration of Conformity ...
Page 57: ...56 11 Appendix ...