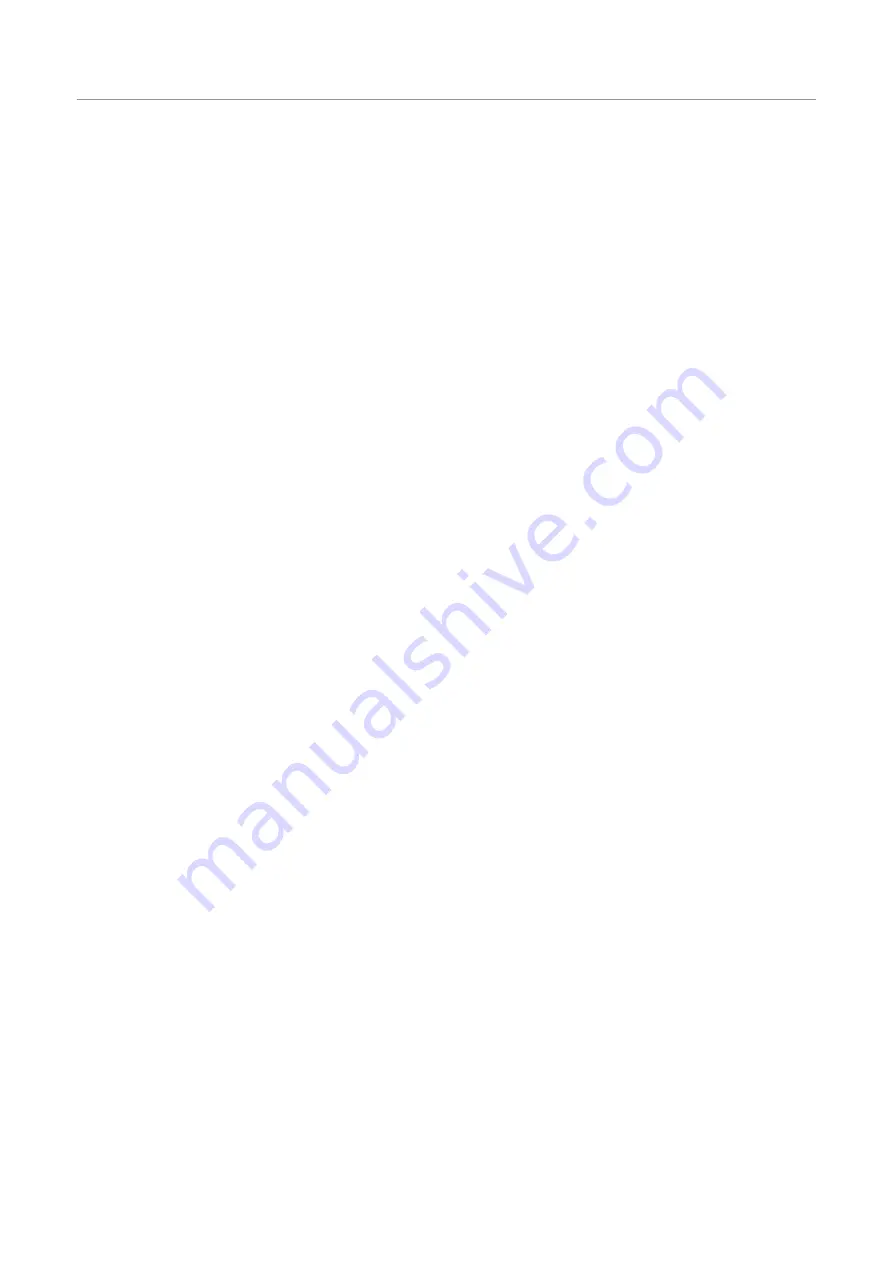
0-2
InTroDuCTIon
0.1 - InTroDuCTIon
The purpose of this workshop manual is to provide instruction for repair technicians and a practical guide to improving the quality
of repairs. This manual enables repair technicians to acquire a thorough knowledge of the machine, indicating the correct methods
for fault diagnosis, for working in safety and for accurate dimensional checks and visual inspections. The instructions also indicate
the products to use, the tightening torques and the adjustment data. The technical material contained in this manual is reserved to
Authorised Dealers and Service Centres who will be duly informed of any technical changes to the machines in question through the
issue of documents regarding modifications, updates and supplements for optional equipment. All technicians and their colleagues
are expressly forbidden from reproducing any part of this manual in any form or from communicating the contents to third parties
without the express written permission of the Manufacturer, who remains the sole owner of this document with all rights reserved in
accordance with applicable laws.
0.1.1 - safety notes
To ensure that machines entrusted to Authorised Service Centres for repair or overhaul continue to function correctly, it is very impor
-
tant that all repair work is carried out in the prescribed manner. The procedures for checks and repairs indicated in this manual are
safe and effective. Some of the operations described require the use of special tools and equipment; these tools have been specifally
designed for the intended purpose and may be ordered directly from the Manufacturers. DO NOT USE MAKESHIFT TOOLS; not
only is there a risk of personal injury, but such tools are rarely suited to the purpose for which they are used. In potentially hazardous
situations, always give priority to personal safety and take the necessary actions to eliminate the danger
0.1.2 - general safety rules
l
Even if you have a thorough knowledge of the machine as regards its components, operation and controls, always take spe
-
cial care when carrying out the following operations; Remember that the machine you are working on is in need of repair or
overhaul and consequently may not always behave as expected.
l
Before starting work, clean the tractor thoroughly to remove all mud, dust and road dirt. Also clean the cab to remove all traces
of oil, snow and ice from the access steps and grab rails.
l
When climbing up to or down from the cab, always ensure you maintain three points of contact at a time (foot or handholds)
in order to keep your balance and prevent accidental falls.
l
Always take special care when carrying out fault diagnosis operations; these operations often require two persons, who must
never stand in front of the wheels when the engine is running.
l
When carrying out checks and repairs, wear close-fitting clothing, safety goggles and protective gloves that are suitable for
the task (cleaning, draining fluids, repairs). When working near moving parts, long hair should be gathered up and tied back
safely under a cap to prevent the risk of entanglement and severe injury.
l
Do not allow anyone who is not directly involved in the work to come near the tractor; ensure that they remain at a safe dis
-
tance.
l
Keep well clear of moving parts; when the engine is running, some moving parts are not easily visible and therefore present a
risk of entanglement, even if protected by safety guards.
l
Ensure that the area is well ventilated before starting the engine in order to avoid the formation of dangerous concentrations
of toxic gases; always connect suitable fume extraction equipment to the exhaust pipe.
l
Do not start the engine with the safety guards removed under any circumstances; all repair and adjustment operations must
be carried out with the engine stopped.
l
Do not top up fuel, oil or coolant levels when the engine is running.
l
Never smoke and ensure there are no naked flames nearby when topping up fuel or oil. Always remove the battery from the
machine before recharging.
l
Before checking or removing the battery, stop the engine and remove the key from the starter switch.
l
Remove the battery and recharge in a well-ventilated area where the temperature exceeds 0°C.
l
When checking or recharging the battery, do not smoke or allow naked flames in the vicinity as the hydrogen gas given off by
the battery is highly explosive.
l
The liquid (electrolyte) contained in the battery is very harmful if it comes into contact with the skin and the eyes; for this rea
-
son, always wear gloves and safety goggles with side shields when checking or topping up the battery. Should any electrolyte
accidentally come into contact with your skin, wash the affected areas immediately with plenty of fresh water; if electrolyte
comes into contact with your clothing, this should be removed as soon as possible. In case of accidental ingestion of electro
-
lyte, drink copious amounts of water, milk or vegetable oil and take antacids such as magnesium, bicarbonate, etc. and seek
medical attention immediately.
l
Before working on the electrical systems, always disconnect the battery terminals.
Summary of Contents for R7.190 DCR
Page 1: ...Workshop manual R7 190 DCR ZKDS7902W0LL10010 R7 210 DCR 10010...
Page 2: ...Find manuals at https best manuals com...
Page 10: ...X CONTENTS PAGE LEFT INTENTIONALLY BLANK Find manuals at https best manuals com...
Page 11: ...0 1 0 Introduction...
Page 22: ...0 12 Introduction PAGE LEFT INTENTIONALLY BLANK...
Page 23: ...10 1 10 Technical characteristics...
Page 41: ...This as a preview PDF file from best manuals com Download full PDF manual at best manuals com...