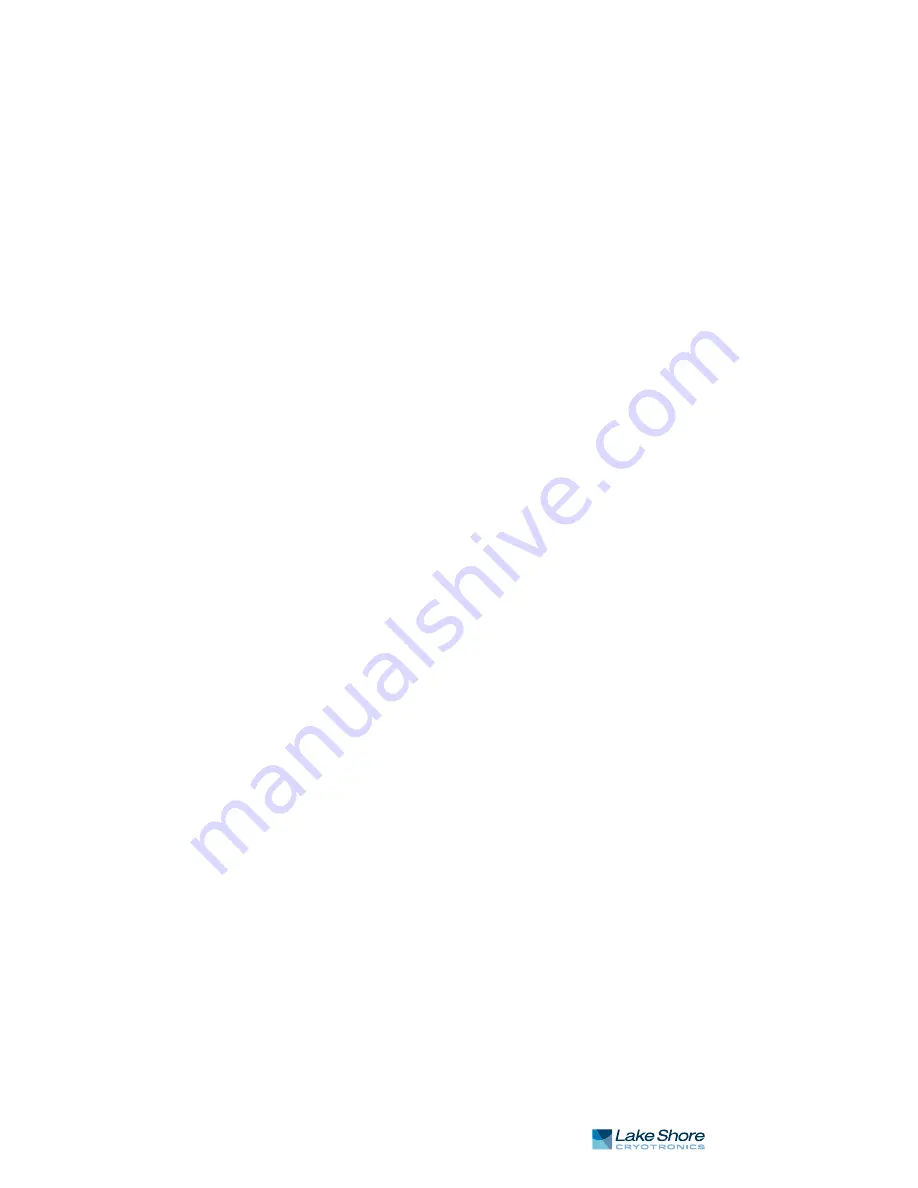
2.7.4 Lead Resistance
37
|
www.lakeshore.com
A familiar form of self-heating is sensor self-heating in resistive temperature detec-
tors (RTDs), but the same principles apply to any resistor being measured. Specifica-
tions for the Model 372 include typical sensor characteristics for a Germanium RTD
that estimates the thermal resistance of the sensor. This example demonstrates how
excitation current must be reduced to compensate for the increase in thermal resis-
tance at lower temperature. Otherwise self-heating would become a significant part
of the overall accuracy. Calculations like this are difficult to do for two reasons, first,
manufactures do not always publish specifications on thermal resistance and second,
the actual thermal resistance is very dependent on installation. An explanation of
how to calculate thermal resistance of a temperature sensor is given in the
Lake Shore Temperature Measurement and Control Catalog, Appendix A.
With an estimate of thermal resistance, the effect of increased excitation current can
be predicted. If self-heating behavior does not match the prediction, noise power may
be high enough to heat the resistor.
2.7.4 Lead Resistance
Measurement leads in cryogenic systems routinely have resistance of tens or even
hundreds of ohms. Lead wire is chosen for its thermal properties first and electrical
resistance is a secondary consideration. The Model 372 measurement circuits can
tolerate significant lead resistance without measurement error. A lead resistance
specification of 100
)
plus 10% of resistance range (for each of the four leads) is
given for most excitation currents. This lead resistance will give a measurement error
that is small compared to the specified accuracy on the resistance range, and in most
cases the error is not measurable. The lead resistance specification is reduced to 10
)
plus 10% of resistance range for the highest current excitations. At the higher cur-
rents, lead resistance of 100
)
can create drops of several volts in each lead. These
large voltage swings will measurably affect the millvolt and microvolt resistor mea-
surements. If lead resistance exceeds the specified values, the instrument will mea-
sure with reduced accuracy until the compliance voltage of approximately 7 V RMS is
reached. Keep the resistance in all of the leads similar whenever possible to maintain
measurement balance.
2.7.5 Current Leakage
Lead wiring cannot be taken for granted when determining accuracy of cryogenic
resistance measurements. Cryostats are notorious for having bundles of long, thinly
insulated leads tightly wrapped around every available heat sink area. Shorts are
inevitable. Lead wires should be “ohmed out” on a regular basis to test for short cir-
cuits that develop over time and thermal cycling.
2.7.6 Cable
Capacitance
Cable capacitance and measured resistance act together as a low-pass filter to atten-
uate the desired measurement signal and shift its phase. Low excitation frequencies
were chosen for the Model 372 to minimize this effect but capacitance can still con-
tribute to measurement error when resistance is high. Driven guards should be used
when measuring resistance above 100 k
)
, but they often cannot be used inside of the
cryostat and are not available for scanner input leads.
2.7.6.1 Parasitic Capacitance Resistance Compensation
While the driven guards provide an excellent means of compensating for cable
capacitance, they do not eliminate it. That, combined with the inability to guard the
lines from the scanner to the resistive load in the cryostat means a parasitic
capacitance, will still be present. This parasitic capacitance siphons current intended
for the resistor, and results in a lower voltage being measured across the resistor. The
end result is an artificially low resistance reading.
The Model 372 provides a complex sensor reading to allow the user to differentiate
between the resistive (real) component and the reactive (imaginary) component of its