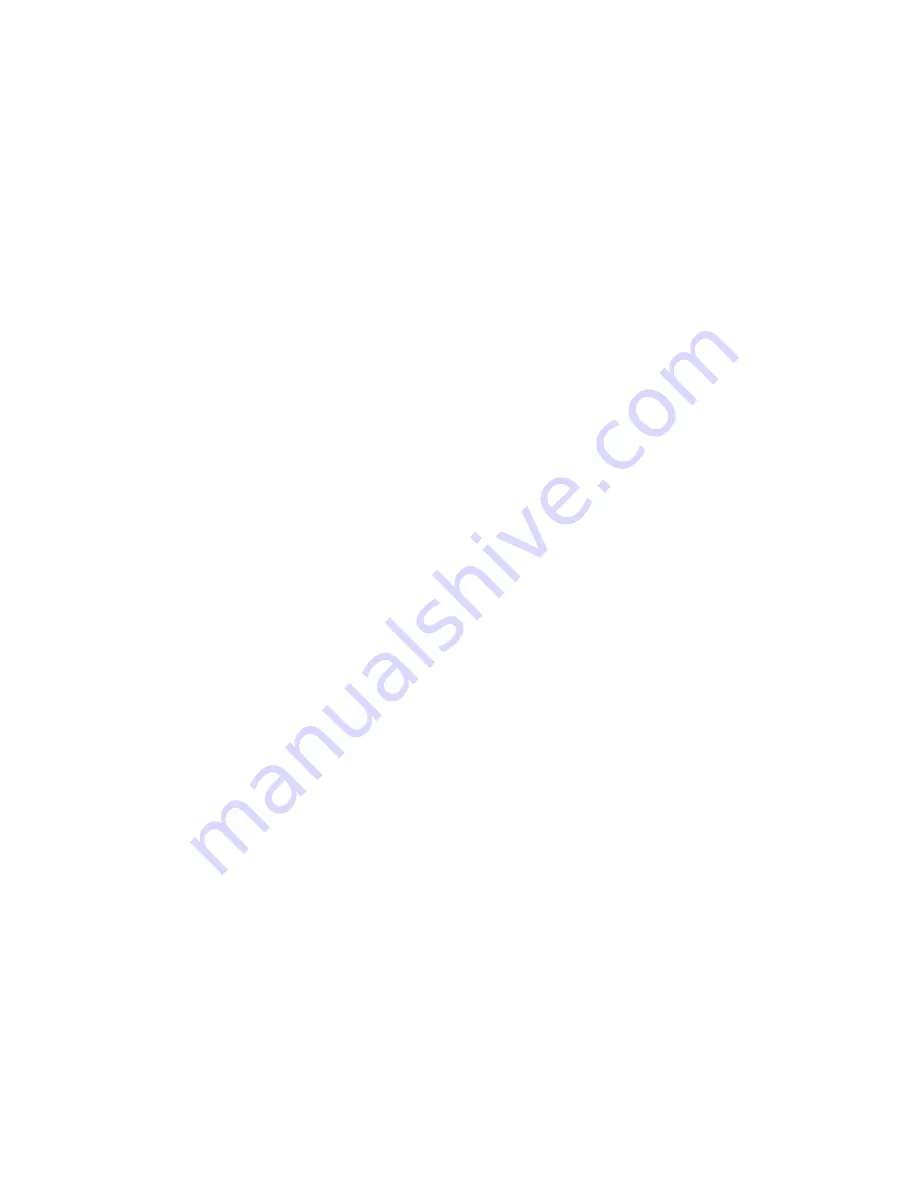
28
c
HAPTER
2:
Cooling System Design and Temperature Control
Model 372 AC Resistance Bridge and Temperature Controller
The Model 372 does not use a bridge configuration for resistance measurement. Its
measurement technique is described in the next paragraph. Side-by-side testing
demonstrated that the precision circuits in the Model 372 would not benefit from a
bridge configuration unless the reference resistors were cooled. This path was not
chosen because installation is more complicated than most applications require. The
name “bridge” was retained to reflect the instrument’s heritage of precision resis-
tance measurements.
2.5.2 Resistance
Measurement
The Model 372 uses a four lead, AC sine wave measurement technique to achieve the
best possible accuracy with the lowest possible excitation. Similar circuits are used
extensively in small signal measurement because they are flexible and can extract
small signals from relatively noisy environments.
The Model 372 uses current excitation because controlled current is very stable and
predictable. Current can also be scaled easily, which is necessary to achieve low exci-
tation. The Model 372 has 21 current settings down to 3.16 pA for the measurement
input and 6 current settings down to 316 pA for the control input. These currents
have low noise and almost no DC component to self heat the measured resistor. For
the measurement input, two excitation modes are available to best utilize the fea-
tures of the current source in different applications. One lower current setting, 1 pA, is
available but not specified because leakage and bias currents in the measurement
circuits can be a large percentage of the excitation current. The 1 pA current setting
should be used for relative measurements only.
Precision resistance measurements use a four lead method to eliminate the effect of
nominal lead resistance. Excitation current is driven on one pair of leads while the
resulting signal voltage is measured on the second pair. Measurement errors from
lead resistance are proportional to current flowing in the voltage leads. Instrument
voltage inputs are expected to have high impedance to prevent the unwanted current
from flowing. The Model 372 has very high input impedance to both normal mode
voltages (created by current source excitation) and common mode voltages (created
by induced noise on the leads).
Offset voltages occur in every electronic circuit both in signal amplifiers and in lead
wire connections that create thermal EMF voltages. Offset voltages affect accuracy
more when the excitation is small because they are a larger percentage of the mea-
sured voltage. AC measurements allow AC filters that greatly reduce amplifier offsets
at each stage, allowing higher amplifier gain and greater sensitivity than DC tech-
niques. The AC technique is also naturally bipolar allowing any remaining thermal
EMF or offset voltages to be averaged out of the resistance measurement. A relatively
low frequency of excitation, 13.7 Hz, was chosen to reduce the effects of lead capaci-
tance on the measurement. In a typical cryostat, lead heat sink requirements and lim-
ited space make it difficult to reduce capacitance enough to operate at significantly
higher frequency.
Environmental noise can limit the resolution of low excitation measurement. Well-
designed filtering is necessary to reclaim the desired signal from the noise. The Model
372 takes advantage of the AC filtering technique called phase sensitive detection
that is used in lock-in amplifiers. This technique has no DC equivalent. Even with
phase sensitive detection it is still necessary to shield these leads from environmental
noise. The Model 372 facilitates appropriate shielding techniques in addition to offer-
ing more active noise reduction circuits.