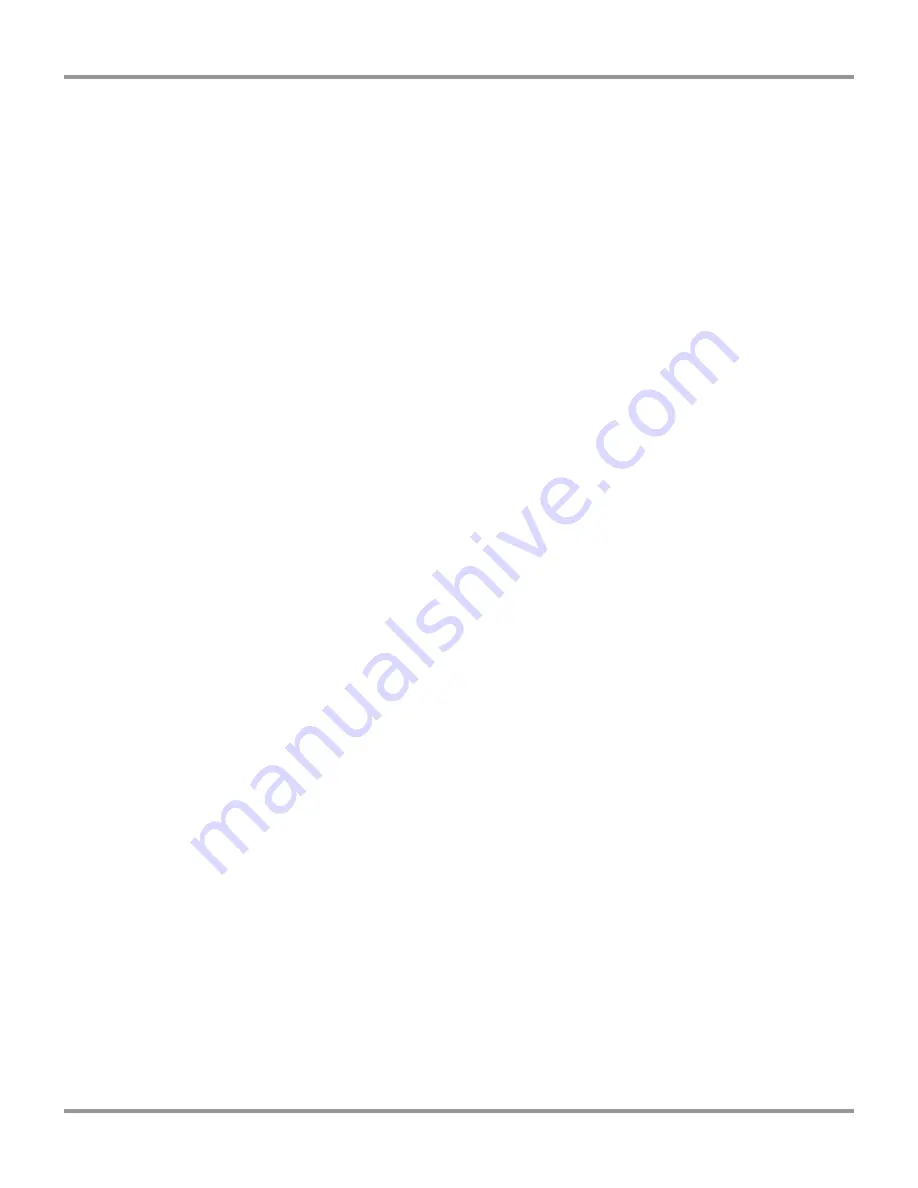
Chapter 6: Troubleshooting
Product Service 1-800-522-7658
34
Original instructions
If vacuum problems continue, consider obtaining a second vacuum gauge capable
of reading a vacuum of 0.010 mbar. It is often useful in determining if the
vacuum pump is operating properly and the vacuum sensor reading is accurate.
4.
Isolate the pump by disconnecting the vacuum hose from the Freeze Dry
System. Deadhead the pump by inserting the vacuum sensor from a
secondary vacuum gauge into the end of the vacuum hose and observe the
vacuum reading obtained. Confirm that the pump is capable of achieving
an ultimate vacuum less than 0.010 mbar or approximately 10 microns. If
an inadequate vacuum reading is obtained, the pump has most likely failed
and may need to be replaced or rebuilt.
Gaskets, Tubing, Connections, Sample
Valves
1.
Check all sample valves on the optional 6 port manifold (if installed) and
ensure all valves are closed or in the vent position.
2.
Check the drain line on the Freeze Dryer and ensure that the quick connect
drain fitting is disconnected from the quick connect drain coupling.
3.
Check all rubber vacuum tubing for signs of deterioration or cracking.
4.
Check all connections and make sure they are secure and leak tight.
5.
Check the Freeze Dry System collector lid gasket and the Stoppering Tray
Dryer door gasket for indentations, cracks or tears. Clean gaskets using a
soft, lint free cloth or paper towel.
6.
The Stoppering Tray Dryer chamber and base unit collector chamber must
be dry.
7.
When checking the sample valves, (if the system is so equipped), pull as
much vacuum as possible. If a vacuum indication is displayed, wiggle or
rotate the valves and watch the gauge for any fluctuations. Fluctuations
can indicate a potential vacuum leak. If the valve seems to be in good
condition, remove the valve and apply a thin coat of vacuum grease to the
stem and the outside sealing surface of the valve body, and reinstall the
valve. If the valve still seems to be the source of the problem, remove the
valve and stopper the hole with a rubber stopper (#6). Continue checking
the other valves.