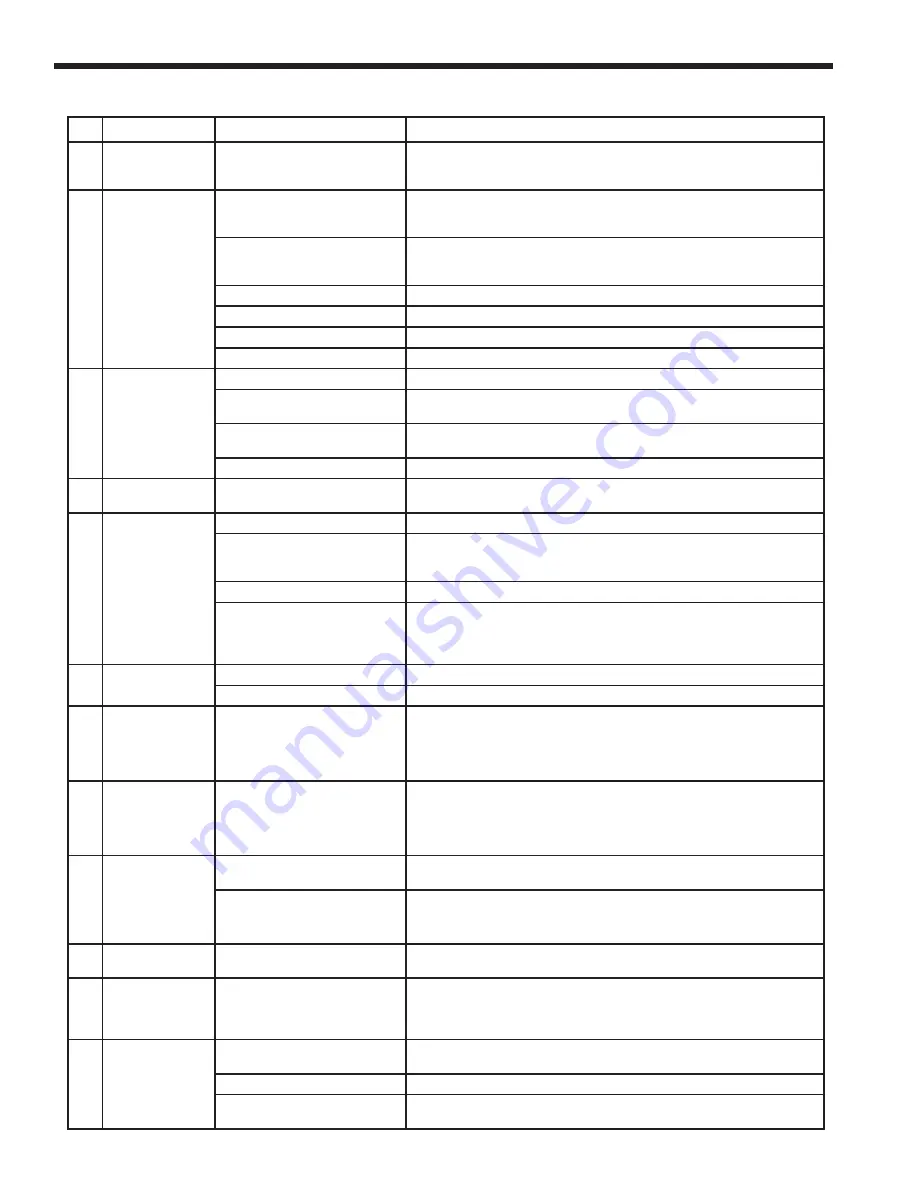
Page 44
#
Symptom
Cause
Remedy
1
Boiler Pump not
operating
No power.
Pump defective.
Incorrectly wired.
Check circuit breakers and power source. Replace. Recheck wiring
diagrams (System pump will not work if below 160ºF or if DHW call)
2
Pilot outage
Inlet gas pressure too low.
Consult gas utility company. Inlet gas pressure to boiler should be 5.5" (1.4
kPa) to 10.5" (2.6 kPa) water column on natural gas. 10.0" (2.5k Pa) to
13.0" (3.2 kPa) on propane gas.
Inlet gas pressure too high
causing an unstable blowing
pilot.
Pressure should be regulated within limits shown above.
Damaged pilot.
Replace.
Dirty pilot.
Blow dust or lint out of pilot.
Plugged or undersized pilot.
Replace pilot orifice.
No power from ignition control.
See Section 11.D on page 45 Refer to Ignition Section in the flow charts
3
Flame roll-out on
start-up
Blocked outlet.
Check flue damper operation.
Pilot out of position (delayed
ignition).
Correct pilot position.
Blocked heat exchanger or flue
or dirty burners or orifices.
Clean and correct as necessary. Check orifice alignment.
Refractory tile out of place.
Correct or replace tile as necessary.
4
Flame has lazy
yellow tip
Low primary air.
Correct manifold pressure according to rating plate. Correct orifice size if
necessary (see parts list). Clean burner ports if dirty. Check heat exchanger.
5
Not enough heat
Inadequate gas supply.
Gas meter too small. Gas line from meter to boiler too small.
Low manifold gas pressure.
Gas pressure on boiler manifold. Must be adjusted to 4.0" (1.0 kPa) W.C.
natural gas. 9.0" (2.2 kPa) W.C. propane. If the supply pressure is correct
the gas valve regulator may be bad and need replacing.
Boiler size inadequate
Replace with a boiler of a higher input.
Burned Copper. Boiler was
dry fired and copper has been
damaged causing a reduced
efficiency.
Replace heat exchanger.
6
Pump noisy
Air in volute.
Bleed air from volute. Check pump alignment.
Worn bearings.
Replace worn parts.
7
Boiler pounding or
knocking
Water flow too low through boiler.
Check temperature rise between inlet and outlet boiler piping. 15°F (8°C) to
25°F (14°C) temperature rise is recommended. If temperature rise is over
25°F (14°C), increase pipe size or pump capacity or locate obstruction.
Check for stuck closed zone valves. Check for zone pumps not operating.
Check for closed valve in system.
8
Boiler condensing
Low water temperature.
Flue product moisture will condense at the start-up until the boiler
water temperature reaches the normal operating conditions. Check for
proper wiring for anti-condensing protection. Install LLH or other piping
arrangement to prevent low return water temperatures from reaching the
boiler.
9
Pump cavities
or low water
pressure at boiler
gauge or bubbles
in system at high
temperature
Defective fill valves or pressure
regulator.
Replace and ensure a minimum of 12PSI.
Expansion tank piped incorrectly. Re-pipe expansion tank to suction side of pump.
10
Pressure relief
valve opens
Waterlogged expansion tank.
Check charge in expansion tank. Replace or refill with proper charge of air.
11
Pilot is lit and
ignition light is on,
but main burners
will not come on.
Main gas valve (MV) terminal is
getting 24V power, gas valve is
bad.
Check wiring and control, replace control if flame light is lit and no power
is going to the MV terminal. Replace gas valve if power is present at MV
terminal and valve isn’t opening.
12
Boiler short cycles
Heat anticipator in room
thermostat set too low.
Increase setting (1.0 is usually satisfactory)
Low water flow through boiler.
Increase size of pump or increase piping size.
Hi-limit may be set too low.
Increase differential. Adjust Economy mode or Reset curve. High limit
should be set between 180-220F. See 8.B on page 32
11.C Troubleshooting Table
LAARS Heating Systems