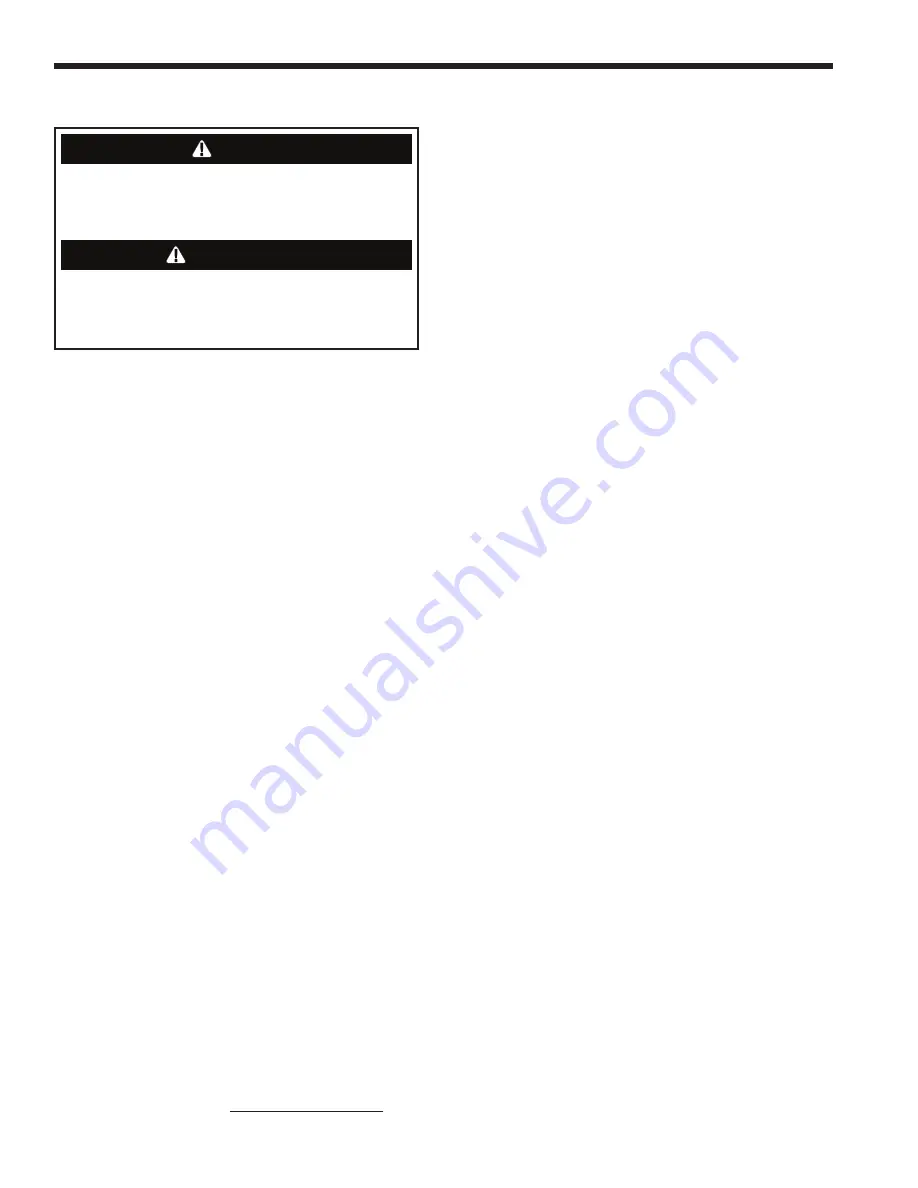
Page 42
these basic items listed be inspected by a qualified
service technician every year.
a. Water temperature controls.
b. Pilot safety system.
c. Automatic gas valves.
d. Low Water Cut Off (ensuring the sensor well is
cleaned of exterior residue periodically based
on system conditions)
e. Mechanical flue damper operation.
f. Pressure Relief Valve. The pressure relief
valve lever must be tripped at least once a
year to ensure that the waterways are clear.
When manually operating lever, water will
discharge through drain line and precautions
must be taken to avoid contact with the hot
water and to avoid water damage.
10. Inspect the heat exchanger for fouling. Fouling
on the external surfaces of the heat exchanger
is caused by incomplete combustion, and is a
sign of venting and/or combustion air problems
or too cold of a return water temperature. The
heat exchanger can be inspected by using a
flashlight and placing a mirror under the burners.
An alternate method is to remove the top panel
to inspect the exchanger from above. This boiler
has easy access through the top cover and the
flue collector for inspection of the heat exchanger.
It is critical to ensure that the flue collector sits in
the proper position so that no flue products will
escape into the living area of the building.
If cleaning is required:
a. Shut off all power to the boiler.
b. Remove the top, flue collector, and heat
exchanger baffles.
c. Remove the burners.
d. Use a hand-operated spray bottle filled with
water, and a wire brush to clean soot and
loose scale from the underside of the heat
exchanger. DO NOT USE COMPRESSED
AIR, HIGH PRESSURE WATER, OR A
GARDEN HOSE.
e. Clean any fallen debris from the bottom of the
unit.
f. Check to make sure the burner ports and pilot
assembly are free of debris before returning
the burners to their original positions.
g. Reassemble the boiler in reverse order,
making sure to replace the heat exchanger
baffles and flue collector into the proper
location.
10.B
Maintenance
WARNING
The Warranty does not cover damage caused by
lack of required maintenance, lack of water flow,
or improper operating practices.
AVERTISSEMENT
La garantie ne couvre pas les dommages causés
par l'absence d'entretien, absence de débit d'eau,
ou pratiques de fonctionnement irrégulières
1. Lubricate any motor bearings that are not sealed
bearings per the instructions.
2. If a strainer is employed in a pressure reducing valve
or the piping, clean it annually or as needed.
3. At start-up, and periodically thereafter, the burner
and pilot flames should be observed. If the flame has
the appearance of “sooting” tips, check for debris
near the orifices. Clean any debris from orifice area
and remove burners to ensure they are debris free
inside and out. If this doesn’t clear the issue the heat
exchanger likely needs cleaning.
4. Ensure vent damper motors open and close by
watching the connecting rod between the stack and
the motor housing. The boiler should never start if
the damper is not in the open position. If it does, it is
critical to safe operation that this gets repaired.
5. Inspect the venting system for obstruction, leakage
or corrosion at least once a year. Any venting system
issues must be repaired before restarting the boiler.
6. Keep the boiler area clear and free from combustible
materials, gasoline, and other flammable vapors and
liquids.
7. Be sure that all combustion air and ventilation
openings are unobstructed.
8. If the boiler is not going to be used for long periods
of time in locations where freezing occurs, it should
be completely drained of all water. To accomplish
this, there is a drain valve on the right side of the
boiler which can be opened. This will drain the right
side of the boiler. There are two plugs located on
the left side of the heater which can be accessed
by removing the side panel which must be removed
to drain that side.
BOTH SIDES MUST BE
DRAINED.
See Section 9.E on page 40
9 . The gas and electric controls on the boiler are
engineered for long life and dependable operation,
but the safety of the equipment depends on their
proper functioning. It is
strongly recommended that
LAARS Heating Systems