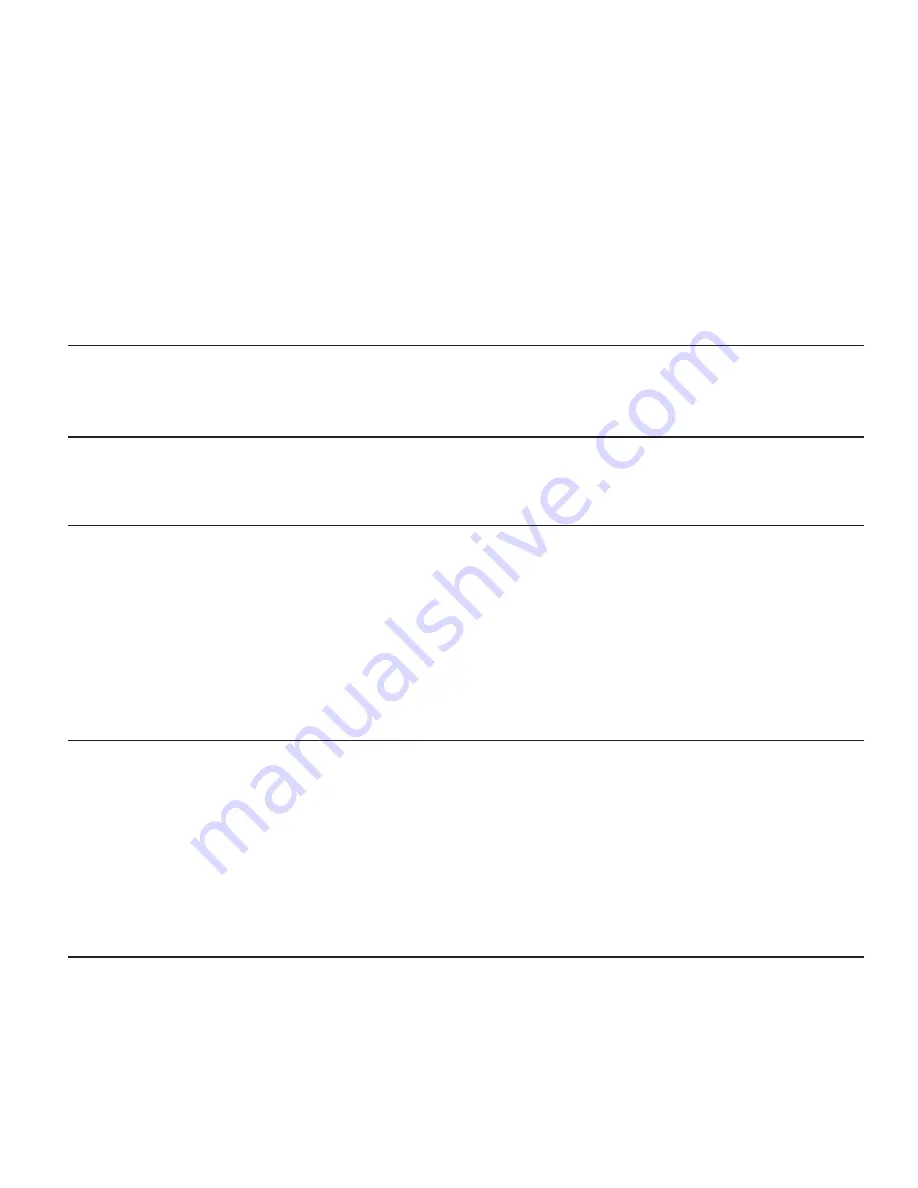
SECTION IV
Troubleshooting
P 4.5
3. The printed image is light
on one end.
4. The printed image has light
or missing characters.
5. The printed characters
have wide lines which also
may be dark on the edges
and light in between.
6. The printed characters are
irregular and fuzzy.
7. The print image is
smeared.
8. The ink is smeared on the
back side of the closure.
A. The ink roll is tipped.
B. The printhead is tipped.
A. The height of the type is
uneven.
A. The print force is too
heavy.
A. The type is dirty.
A. The closure track is dirty.
B. The ink roll is not working
properly.
A. The type is printing on the
closure track when no
closure is at the print
location.
Refer to Section III, Adjustments, Part R. INK-
ING FORCE-SIDE TO SIDE.
Refer to Section III, Adjustments, Part S. PRINT
FORCE-SIDE TO SIDE.
With usage type wears. For the bandheads,
some of the most-used characters are repeated
on some bands. Replace the bandhead if
needed. For the type block, replace worn type.
Turn the print force knob 1/4 turn clockwise at a
time and test the results. Continue adjusting
the print pressure until the printed image be-
comes light and then back up the knob 1/4 turn.
Clean the type with a cloth or tissue. Isopropyl
alcohol swabs work well. For the gripline block
printer, remove the block from the printer lever.
For the band printer, remove the ink roll while
cleaning the type or rotate the printhead by
hand to gain better access to the typeface.
Store the closures in an area where they will
stay clean and not gather dust and debris. Al-
ways keep the printer cover closed. Do not
soak type in alcohol or other solvents as it will
swell the type and make it unusable.
If the print image extends to the edge of the clo-
sure, it will smear in the closure track. Once
the ink starts to smear, the problem will worsen
rapidly. Refer to Section III, Adjustments, Part
B. TOP CLOSURE TRACK REMOVAL and
clean the top and bottom of the closure track
grooves with a tissue or soft cloth. Isopropyl al-
cohol works well for this.
Do not attempt to recondition a used ink roll by
adding solvent or stamp pad ink to the roll.
Refer to Section II, Operation, Part B. LOADING
A ROLL OF CLOSURES.
PROBLEM
SYMPTOM
CORRECTION
086B 02 18
Summary of Contents for 086B-100
Page 14: ...This page intentionally blank ...
Page 36: ...This page intentionally blank ...
Page 41: ...SECTION V Parts Identification P 5 5 PARTS COMMON 2 Figure 5 3 PARTS LIST 086B 02 18 ...
Page 42: ...SECTION V Parts Identification P 5 6 ELECTRICAL COMPONENTS Figure 5 4 086B 02 18 ...
Page 43: ...SECTION V Parts Identification P 5 7 ELECTRICAL COMPONENTS Figure 5 4 PARTS LIST 086B 02 18 ...
Page 44: ...SECTION V Parts Identification P 5 8 086B MODEL 100 LOK TRACK Figure 5 5 086B 02 18 ...
Page 48: ...SECTION V Parts Identification P 5 12 086B MODEL 100 ROLL SUPPORTS Figure 5 7 086B 02 18 ...
Page 53: ...SECTION V Parts Identification P 5 17 086BP BAND PRINTER ARM Figure 5 9 PARTS LIST 086B 02 18 ...
Page 57: ...SECTION V Parts Identification P 5 21 086BP BLOCK PRINTER Figure 5 11 PARTS LIST 086B 02 18 ...
Page 59: ...SECTION V Parts Identification P 5 23 086BP PRINTER LINKAGE Figure 5 12 PARTS LIST 086B 02 18 ...
Page 62: ...This page intentionally blank ...
Page 64: ...SECTION VI Wiring P 6 2 086B WIRING DIAGRAM FOR MODEL 700P Figure 6 2 086B 02 18 ...