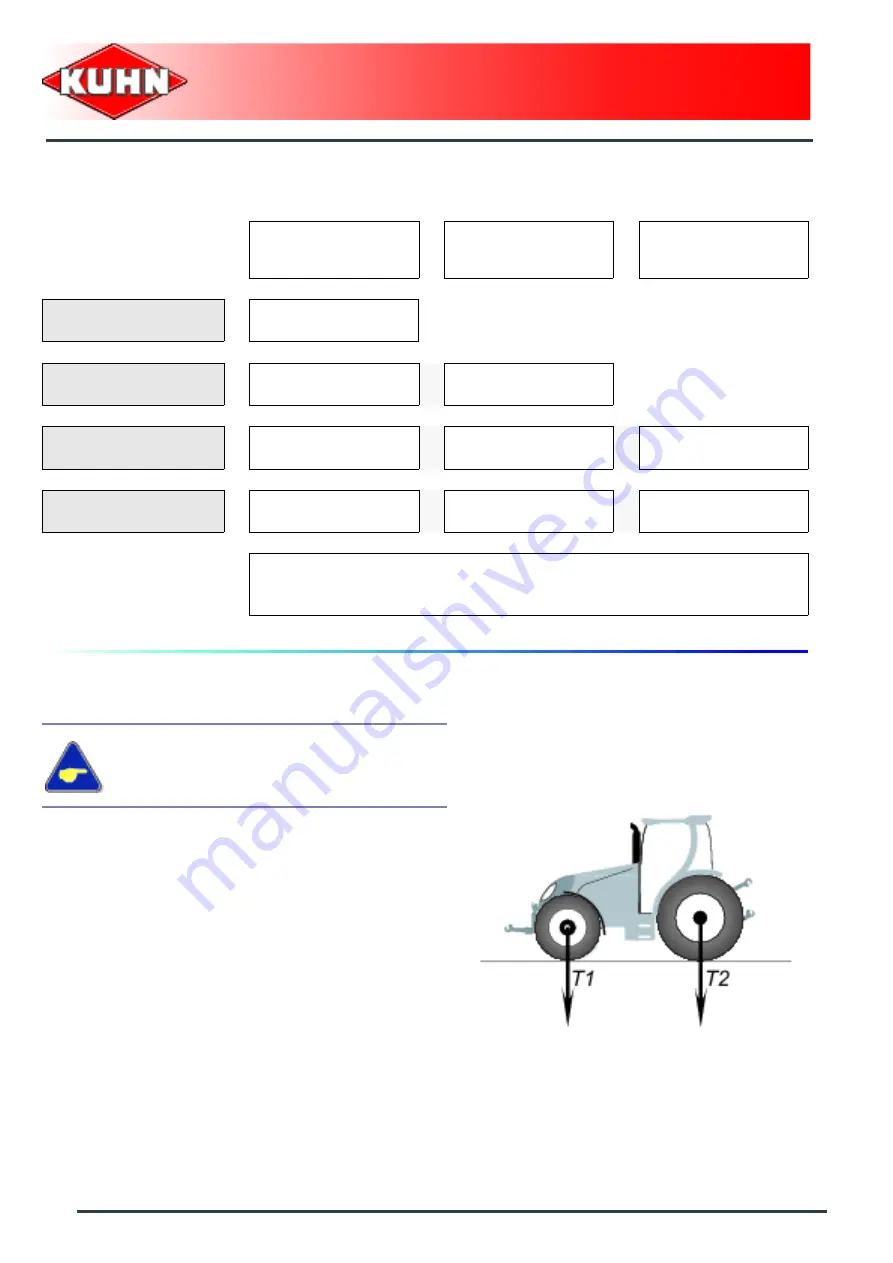
Mounted field sprayers
178
OMNIS
Appendix
Table:
Determining the machine weight (M2) and
the position of its centre of gravity (d)
Tractor only:
Actual value obtained
by calculation
Value authorized
according to
operator's manual
Double value of the
authorized capacity
per tyre (2 tyres)
Minimum front/rear
ballasting
kg
Total weight
kg
≤
kg
Load on front axle
kg
≤
kg
≤
kg
Load on rear axle
kg
≤
kg
≤
kg
The minimum ballasting must be made by fitting a tool or an additional mass to the
tractor.
The values obtained must be below or equal the authorized values.
If the data required to calculate the total
weight, axle loads and minimum ballasting
are not supplied, use the following method.
Summary of Contents for Omnis 1000
Page 1: ...GN007AGB C OPERATOR S MANUAL Mounted field sprayers OMNIS GN007AGB C English 06 2010 ...
Page 2: ......
Page 8: ...Mounted field sprayers 6 OMNIS Identification of the machine 2 Rear view ...
Page 28: ...Mounted field sprayers 26 OMNIS Safety ...
Page 183: ...Limited warranty Mounted field sprayers OMNIS 181 Limited warranty ...
Page 184: ...Mounted field sprayers 182 OMNIS Limited warranty ...
Page 185: ......
Page 186: ......
Page 187: ......
Page 188: ......