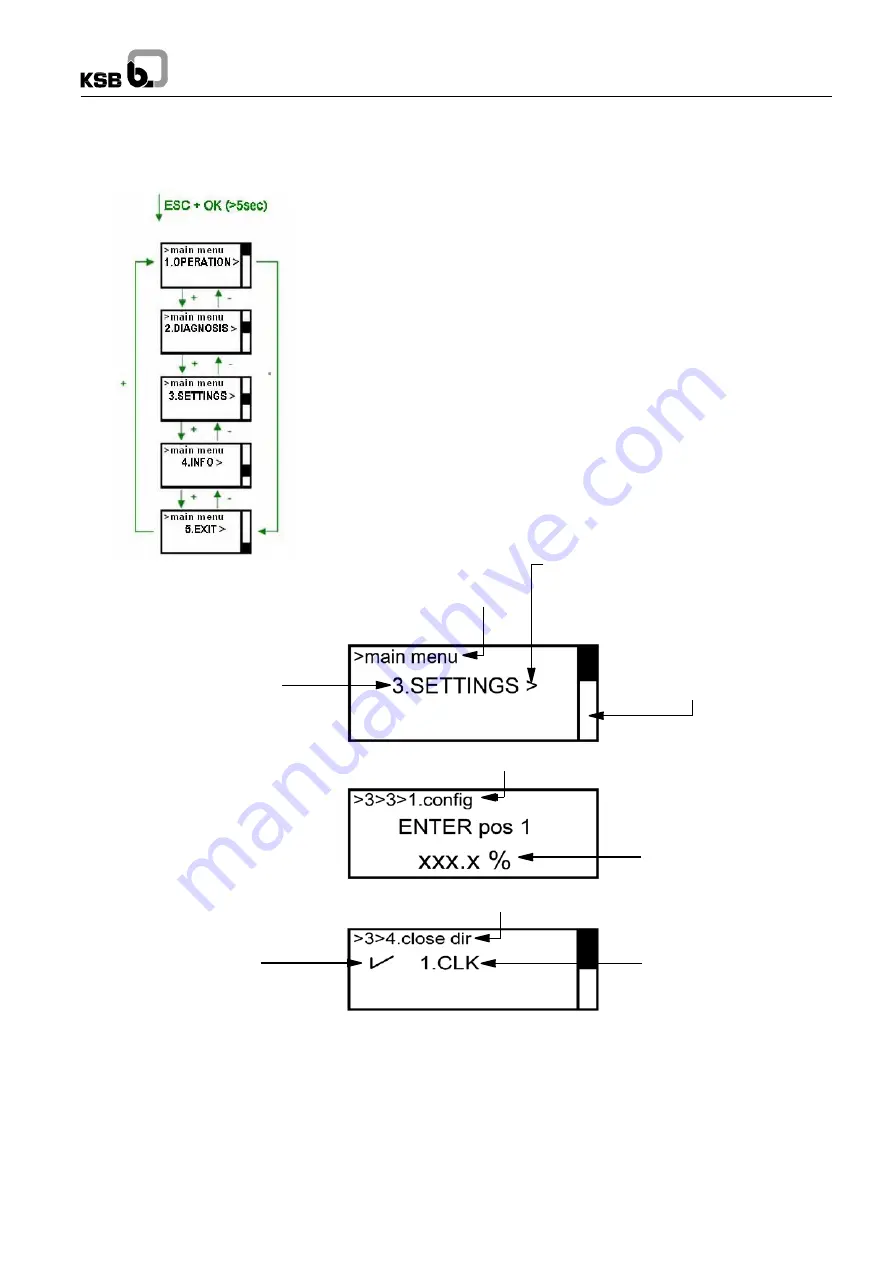
23
SMARTRONIC MA
VI - 3 Submenu screen
To access the submenus:
- Press buttons <OK> and <ESC> simultaneously for 5 seconds.
- Navigate with the <+> and <-> buttons.
- Validate with <OK>.
- Cancel with <ESC>.
Indicates the presence
of a submenu
Path
Submenu title
Scrollbar level
Path
Parameter value
Path
Parameter validation
Parameter